Introduction
Within This Page
This section addresses the mitigation of explosion effects on the exterior envelope of a new building designed to meet federal anti-terrorist design requirements. The recommendations given are primarily focused on meeting the ISC Security Design Criteria but are also useful for understanding the anti-terrorist design requirements of other government agencies including the U.S. Department of Defense and U.S. Department of State. Although the concepts presented are for new buildings, many of the same concepts may be applied to retrofit of existing buildings. Additional information regarding hardening of existing buildings may be found in WBDG Retrofitting Existing Buildings to Resist Explosive Threats.
The primary design objective is to save the lives of those who visit or work in these government buildings in the event that an explosive terrorist attack occurs. In terms of building design, the first goal is to prevent progressive collapse which historically has caused the most fatalities in terrorist incident targeting buildings. WBDG page Physical Security: Building Design to Resist Explosive Threats provides further discussion on this topic. Beyond preventing progressive collapse, the goal is to provide design solutions which will limit injuries to those inside the building due to impact of flying debris and air-blast during an incident, and to limit harm to innocent civilians near the building perimeter. Finally, we seek to facilitate the rescue/recovery efforts by limiting the debris blocking access to the building and potential falling debris hazards which could harm rescue workers. In some cases, secondary objectives may need to be considered such as maintaining critical functions and minimizing business interruption.
Existing criteria documents vary in the level of detail that they provide, and all have room for interpretation. A 'blast consultant' with expertise in structural dynamics and experience with the governing criteria documents can be a valuable resource for the team throughout design and construction. Often blast consultants are required for projects which meet anti-terrorist design criteria if explicit computation of structural response to explosive loads is required. Design criteria will give the requirements that this specialist needs to meet such as the number of years of experience and formal technical training in structural dynamics.
The recommendations in this section are solution focused. They are intended for designers who are tasked with implementing federally mandated anti-terrorist design criteria into projects, recognizing that these requirements need to be balanced and integrated with many other design constraints such as sustainability, construction and life-cycle costs, constructability, architectural expression, and natural hazards protection. Security design needs to be part of an overall multi-hazard approach to the design, to prevent the solution for explosion effects from worsening the behavior of the building for other hazards. Conversely, multi-use solutions which improve the building performance for blast and other considerations such as sustainability are to be encouraged (See WBDG Resource Page Balancing Security/Safety and Sustainability Objectives).
To maximize the benefit provided by the recommendations, anti-terrorist considerations should be implemented at the earliest planning and design stages possible. This will enable the resulting design to maximize protection while integrating with other design considerations.
Description
In this sub-section the threat, loads and damage resulting from explosions are explained. Both vehicle and hand delivered weapons targeting the exterior envelope are considered.
Threat Definition
The primary threat is a stationary vehicle weapon located along a secured perimeter line surrounding the building (see Figure 1). Depending on the accessibility of the site to vehicles there may be more than one line of defense to consider. The outermost perimeter line is often a public street secured against vehicular intrusion using barriers and with limited secured access points. Vehicle weapon sizes vary depending on the specific criteria used and may be obtained from the federal agency client on a 'need to know' basis.
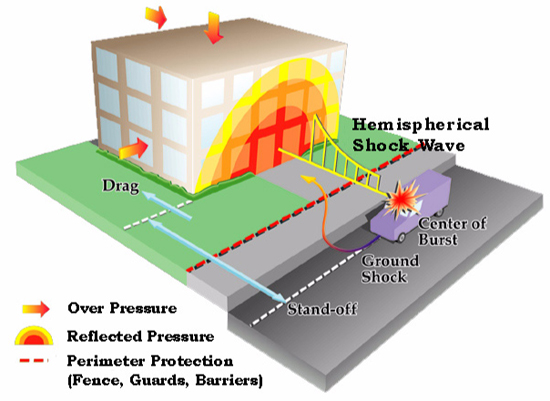
Figure 1. Vehicle Weapon Threat. Image Credit: FEMA 427, Primer for Design of Commercial Buildings to Mitigate Terrorist Attacks (2003)
This threat is to be considered on all sides of the building with a public street or adjacent property lines along the secured perimeter line. Because air-blast loads decay rapidly with distance, the highest loads are at the base of the building and decay with height. The benefit of these reduced loads is usually not realized in terms of reduced design requirements except for high rise structures.
Although some government design criteria require building setbacks that may vary from tens to hundreds of feet, setback requirements are difficult to enforce in dense urban environments and many criteria have gravitated away from these requirements. Instead, these criteria specify performance objectives that must be achieved regardless of the available setback distance. In most cases shorter setback distances will translate into more severe design requirements for the exterior envelope. In other cases, a waiver may be required to proceed with the design.
Sometimes the criteria document will consider the stationary vehicle threat of a weapon that manages to pass through security screening along the perimeter. For instance, this threat may be located in an employee parking stall near the building, or at the loading dock. This weapon is typically smaller than the weapon considered along the outermost perimeter line because the vehicle entering the screened area is assumed to have been inspected. The size of the weapon is based on the maximum weight of explosives that could be carried in the vehicle without attracting attention. A minimum separation distance between secured surface parking areas and the building is desirable whenever the available real estate permits.
A secondary threat that is sometimes considered is a hand carried weapon placed directly against the exterior envelope. This weapon may be carried in a briefcase, backpack or hand truck depending on the level of security screening provided outside the building.
Note that some design criteria documents assume that no weapon is able to pass through the outmost security point based on the operational measures implemented. This will need to be verified prior to proceeding with design. In this case, only the vehicle weapon is considered outside the secured perimeter line.
Blast Loading
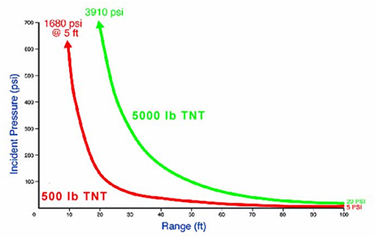
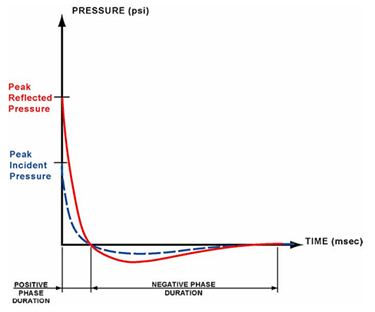
Figure 2. Air-blast pressures as a function of weapon size and distance.
Figure 3. Air-blast as a function of time.
Image Credit: FEMA 427, Primer for Design of Commercial Buildings to Mitigate Terrorist Attacks (2003)
Explosive pressures used for design are typically much greater than conventional loads. Fortunately, they decay extremely rapidly with time and space. As a rule of thumb, the pressures generated increase linearly with the size of the weapon, measured in equivalent pounds of TNT, and decrease exponentially with the distance from the explosion (see Figure 4). The duration of the explosion is extremely short, measured in thousandths of a second, or milliseconds (see Figure 5). Effects of shock wave expansion and engulfment of the building are shown in Figure 4.
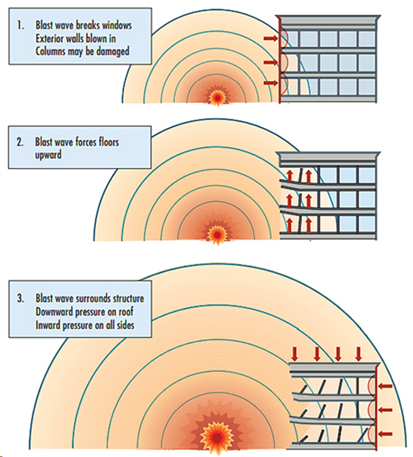
Figure 4. Sequence of air-blast effects Image Credit: BIPS 06 / FEMA 426 Reference Manual to Mitigate Potential Terrorist Attacks Against Buildings (Source: Naval Facilities Engineering Service Center, User's Guide on Protection Against Terrorist Vehicle Bombs, May 1998)
Pressure acting on the side of the building facing the explosion is amplified by factors that can be ten times the incident pressure. This pressure is referred to as the reflected pressure. Since it is not known which sides of the building the explosion will act on typically, all sides need to be designed for the worst case.
Air-blast pressures have a negative or suction phase following the direct or positive pressure phase. The negative phase pressures can govern response in low pressure regions causing windows to fail outward or sloped roof systems to fall off the building.
Slender members such as exposed columns which have less surface area for the air-blast to act on tend to be more sensitive to drag effects rather than direct pressure loading because the air-blast tends to "wrap-around" these members lessening the time that the reflected air-blast is acting.
Rebound of the exterior envelope components following the explosion can pull the façade members off the building exterior. Note that this effect is different from the negative pressure effects discussed above. Rebound refers to the reversal of structural motion due to vibration rather than the reversal of loading direction. Since the design objective is to protect occupants, failure of the exterior envelope in the outward direction may be acceptable provided that the hazards of falling debris post-event and blocked egress points are avoided.
Immediately below the weapon, a crater will be formed which may cause damage to underground portions of the building which cause damage to the foundation and the sub-surface roof and foundation walls which extend beyond the line of the superstructure.
In addition to the propagation of a pressure wave through the air, a proportion of the energy of the weapon is transmitted through the soil. This effect is analogous to a high intensity, short duration earthquake which can disturb the functionality of computers and mechanical/electrical equipment. For above ground explosions, this effect is negligible and is generally neglected in design.
- Simple geometries, with minimal ornamentation (which may become flying debris during an explosion) are generally recommended unless advanced structural analysis techniques are used to evaluate the design. Ornamentation should be a lightweight and ductile material that is less likely to become lethal projectiles in the event of an explosion.
Air-blast parameters for a defined weapon size and distance from the exterior envelope may be determined by using charts found in military handbooks or by using government sponsored software products such as CONWEP or ATBlast.
Design Philosophy
To reduce the hazards associated with fragments being propelled into the building interior the envelope system is designed by keeping in mind the concepts of balanced design (discussed later in this page), ductile response, and redundancy. The use of dynamic non-linear structural analysis methods is also beneficial when designing the exterior envelope of a building to resist air-blast effects.
Intuitively, it may seem that heavier stiffer systems are preferable to thinner more flexible systems. However, lighter systems are generally preferable for mitigating explosive effects, provided that they are designed to be ductile, redundant, balanced, and can resist the design load with the required response. Although heavier systems have added mass which is advantageous in mitigating the effects of explosions, they may be more prone to brittle failure if not properly designed and can impart significantly larger loads into the supporting structure behind the envelope. The larger loads may cause structural failures and perhaps initiate progressive collapse. These more robust solutions have their place in high-risk buildings or in localized areas closest to the threat. However, the lighter more flexible systems tend to be preferred solutions in the majority of civilian buildings being designed to resist air-blast effects today. By permitting some permanent damage to the exterior envelope, which does not significantly increase the hazard to the occupants, it is possible to design lighter, more cost effective, systems that absorb energy through deformation, and transmit lower forces into the connections and supporting structure, thus reducing the potential for more serious structural failures.
Design Methods
The typical design approach for incorporating blast resistance is to first design the building for conventional loads, then evaluate the response to explosive loads and augment the design, if needed, making sure that all conventional load requirements are still met. This enables the design to meet all the requirements for gravity and natural hazards in addition to air-blast effects.
Blast mitigation may make the design more hazardous for other types of loads and therefore an iterative approach may be needed. As an example, for seismic loads, increased mass generally increases the design forces, whereas for explosion loads, mass generally improves response. Careful consideration between the blast consultant and the structural engineer is needed to provide an optimized response.
As an air-blast is a high load, short duration event, the most effective analytical technique is dynamic analysis, allowing the element to go beyond the elastic limit and into the plastic regime. Analytical models range from handbook methods to equivalent single-degree-of-freedom (SDOF) models to finite element (FE) representation. For SDOF and FE methods, numerical computation requires adequate resolution in space and time to account for the high-intensity, short-duration loading and non-linear response. Difficulties involve the selection of the model, the appropriate failure modes, and finally, the interpretation of the results for structural design details. Whenever possible, results are checked against data from tests and experiments for similar structures and loadings.
Exterior envelope components such as columns, spandrels and walls can often be modeled by a SDOF system and then solving the governing equation of motion by using numerical methods. Handbook methods may be used to evaluate the peak displacement response of structural components using graphs that require only that the designer define a few parameters including the ultimate resistance, fundamental period, and elastic limit deflection. Other charts are available which provide damage estimates for various types of construction based on peak pressure and peak impulse based on analysis or empirical data. Military design handbooks typically provide this type of design information. The design of the anchorage and supporting structural system may be evaluated by using the ultimate flexural capacity of the member.
For SDOF systems, material behavior may be modeled using idealized elastic, perfectly-plastic stress-deformation functions, based on actual structural support conditions and strain rate enhanced material properties. The model properties selected provide the same peak displacement and fundamental period as the actual structural system in flexure. Furthermore, the mass and the resistance function are multiplied by mass and load factors, which estimate the actual portion of the mass or load participating in the deflection of the member along its span.
For more complex elements, the engineer must resort to finite element numerical time integration techniques and/or explosive testing. The time and cost of the analysis cannot be ignored in choosing design procedures. Because the design process is a sequence of iteration, the cost of analysis must be justified in terms of benefits to the project and increased confidence in the reliability of the results. In some cases, an SDOF approach will be used for the preliminary design and a more sophisticated approach, using finite elements, and/or supported by explosive testing may be used for the final verification of the design.
A dynamic non-linear approach is more likely to provide a section that meets the design constraints of the project compared with a static approach. Elastic static calculations are likely to give overly conservative design solutions if the peak pressure is considered without the effect of load duration. By using dynamic calculations instead of static, we are able to account for the very short duration of the loading. Because the pressure levels are so high, it is important to account for the short duration to mitigate response. In addition, the inertial effect included in dynamic computations greatly improves response. This is because by the time the mass is mobilized, the loading is greatly diminished, enhancing response. Furthermore, by accepting that damage occurs we are able to account for the energy absorption of ductile systems that occurs through plastic deformation. Finally, because the loading is so rapid, we are able to enhance the material strength to account for strain rate effects.
Response is evaluated by comparing the ductility (i.e., the peak displacement divided by the elastic limit displacement) and/or support rotation (the angle between the support and the point of peak deflection) to empirically established maximum values which have been established by the military through explosive testing. Note that these values are typically based on limited testing and are not well defined within the industry at this time. Maximum permissible values vary depending on the material and the acceptable damage level. Some criteria documents do provide the design values that need to be met. Other criteria are silent on this topic or make a general reference to a source document.
Acceptable Damage Levels
Levels of damage computed by means of analysis may be described by the terms: superficial, moderate, heavy, and hazardous depending on the peak ductility, support rotation and collateral effects. These four levels of damage are correlated to four Levels of Protection (LOP): High, Medium, Low and Very Low. Structures that are not minimally designed to the Very Low LOP may fail catastrophically or building components may become airborne debris in response to the specified blast loading. These levels of performance are quantified for different materials of construction in The American Society of Civil Engineers publication Blast Protection of Buildings (ASCE 59-22).
Generally, moderate damage (medium LOP) at the "Design Threat" level is a reasonable design goal for new construction. For buildings that need to remain operational post-event or are designated as high risk, minor damage may be the more appropriate damage level.
Applications
The building envelope is the most vulnerable building system in response to an exterior explosive threat because it is likely to be closest to the weapon, and it is the critical line of defense for protecting the occupants of the building. Laminated glass is perhaps the single most effective measure to reduce extensive injuries. However, hardening of the façade is typically the single most costly and controversial component of blast protection, and may produce a dramatic change to the exterior appearance of the structure such as smaller window sizes and more rugged attachments. Moreover, given the large surface areas of most buildings, modest levels of protection may not be cost-effective. Therefore, it may be best to concentrate on improving the post-damaged behavior of most of the façade rather than focus on the most highly loaded façade elements.
Regardless, early consideration of man-made hazards helps with identification of the security objectives as well as prioritization of higher risk. In the end, incorporation of security measures early in the design phase may significantly reduce the overall cost of protection and the inherent protection level provided to the building. If protection measures are considered as an afterthought, the cost is likely to be greater because more areas will need to be structurally hardened due to poor planning.
Walls
The exterior walls of a building are subject to reflected blast pressures from an explosive threat located at the secure perimeter, and at a minimum should be designed to fail in a ductile mode. Depending on the wall construction and materials being used, the security standards will provide performance criteria to which the walls are to comply. Where walls support windows and doors, the additional tributary loading will need to be accounted for in the design of the surrounding wall structure with consideration for balanced design. The balanced design philosophy is for the glazing to fail at lower pressures than the surrounding support system to prevent a whole unit from entering the building. This is discussed further in the glazing section.
It may be advantageous to consider the reduction in pressure with height due to the increase in distance and the angle of incidence at the upper levels of a high-rise building. If pressure reductions are taken into account at the upper floors, minimum requirements such as balanced design, ductile response and redundancy are to be met to reduce the hazard to occupants in case the actual explosion is greater than the design threat. Various types of wall construction are considered below.
Cast-In-Place Reinforced Concrete
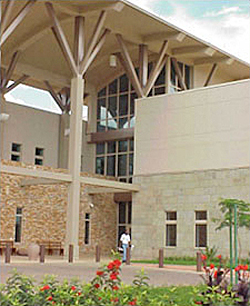
Figure 5. U.S. Embassy, Kampala, Uganda
Cast-in-placed (CIP) reinforced concrete is the most commonly used material to mitigate explosive threats due to a number of attributes that are desirable in blast design. It has significant mass, which improves response to explosions because the mass is often mobilized only after the pressure wave is significantly diminished, reducing deformations. Members can be readily proportioned and reinforced for ductile behavior, and its construction is unparalleled in its ability to achieve continuity between members. Due to its ability to provide the highest level of protection, this is the material used for construction of walls of military bunkers, new U.S. embassies, and other high-risk facilities vulnerable to large explosive threats (see Figure 5). The military has performed extensive research and testing of CIP concrete performance under blast applications.
CIP concrete is also recommended for portions of lower risk buildings that do not meet required minimum setbacks or which house critical functions such as primary egress paths or high occupancy areas.
Note that for reinforced concrete to respond favorably to explosion loads, it must be detailed in a ductile manner such as is done in seismic zones. Non-ductile concrete design such is used in non-seismic design can perform badly, as is witnessed by the collapse of the Alfred P. Murrah Building in Oklahoma City. Some attributes of ductile design for blast design are as follows:
- Use symmetric reinforcement on both faces.
- Span the wall floor to floor rather than from column to column.
- Stagger splices away from high stress areas.
- Space bars no more than one wall thickness apart, but no less than one half the wall thickness apart.
- Use ductile special seismic detailing at connections.
- Use development lengths to develop the ultimate flexural capacity of the section.
- For progressive collapse prevention, consider the loss of exterior wall that measures vertically one floor height and laterally one bay width.
- Use closed ties or spiral reinforcing along the entire length of beams and columns including connections with a minimum bend angle of 135 degrees and a spacing not exceeding d/2.
Pre-cast Concrete
Pre-cast panels are commonly used for building enclosures due to speed of construction, controlled construction process, and aesthetic flexibility. Typically, design of the pre-cast panels is delegated to a pre-cast designer who should work with an in-house designer or a blast consultant to determine panel reinforcing as well as the blast reactions for which the supporting structure is to be designed. This requires coordination between the design and construction team early in the design process in order to plan for member sizes, thickness and configuration of panels, location of panel connections, and to account for sufficient reinforcing to support the panels. This coordination process should be considered for conventional design and then validated and enhanced for the explosive threat loading. The following are recommendations and considerations in designing pre-cast elements for air-blast resistance.
Thickness: The thickness of the pre-cast panels should allow for adequate reinforcing with sufficient concrete cover on the reinforcing steel. Typically, the thickness should be no less than 5-inches, exclusive of reveals. two-way reinforcing bars to increase ductility and reduce the chance of flying concrete fragments.
Reinforcement: Two-way, symmetric reinforcement is recommended to accommodate large deformations and rebound loads. For thin panels where it is difficult to place two layers of reinforcement, the use of two layers of heavy wire mesh, one layer of two-way reinforcement along the centerline, or staggered bars on either face may be considered. If a single layer of reinforcement is used, it is critical to design the section so that the steel yields before the concrete fails in compression to obtain a ductile response. Enhanced protection may be provided by placing Fiber Reinforced Polymers, geotextile materials, Kevlar, or similar materials on the inside face to provide confinement, fragment restraint and added tensile capacity. If reinforcing bars are used, a layer of wire mesh on the interior face may help to further restrain concrete fragments from entering the space. Closely spaced bars also help fragment restraint, but care must be taken not to unnecessarily increase the ultimate flexural capacity so as to keep the reaction loads to a reasonable level. Note that centerline reinforcement will not work in the rebound direction due to the failure of the tension concrete during the positive phase. If the primary objective is to protect occupants and not passersby, then this may be acceptable. Above major egress points however, where debris outside the building presents an obstacle to ingress and egress post event, added protection is desirable.
Load bearing systems: For load bearing pre-cast systems, panels need to be designed to span over failed areas by means of arching action, strengthened gravity connections, secondary support systems or other means of providing an alternate load path.
Connections: Ductile connections should be used. In the event the actual air-blast loading is higher than the design load, the connections and supporting structure needs to be able to accept the loads transmitted by the panel loaded to its ultimate flexural capacity. Reaction loads from the windows at ultimate capacity are to be included in the calculation of connection design loads. Using this approach, every panel with a different configuration will have a different set of loads used for designing the connections. Note that small panels will have higher reaction loads than larger panels using this method due to their increased stiffness. Standardizing the panel sizes greatly simplifies the connection load determination.
Also, the connections need to provide sufficient lateral restraint for the panels to accept large deformations. Depending on the design details of the connection used, lateral restraint design will require consideration of in-plane shear, buckling, flexure and/ or tension loads in the design. Punching shear through the panel also needs to be checked for the ultimate flexural capacity of the panel. The connection should provide a direct load path from the panel into the supporting structure to minimize P-delta effects. In seismic areas where connector rods are used to permit large in-plane motion it is recommended that buckling due to out-of-plane motion be checked. Floor-to-Floor panels with continuous, bearing type connections directly into the floor diaphragms are preferred. Multi-story panels directly bearing on the floor diaphragms may also be considered. Connections into exterior columns or spandrel beams are discouraged to avoid the possibility of initiating structural collapse of the exterior bay. Redundant gravity connections are strongly recommended to prevent falling debris if a single connection fails.
Connections should be checked for rebound loads. It is conservative to use the same load in rebound as for the inward pressure. More accurate values may be obtained through dynamic analysis or charts provided in military handbooks.
Specifications: Specifications for pre-cast elements can be either in the form of a performance requirement, with the air-blast pressures and required performance provided, or as a prescriptive specification with equivalent static pressures provided. The equivalent static pressures are computed based on the peak dynamic response of the panel for the defined threat. The performance specifications give the pre-cast contractor more flexibility to provide the systems with which they are most familiar. However, it requires that the contractor either have in-house dynamic analysis capability or have a relationship with a blast engineer who can work with them to customize the most cost-effective system.
On the other hand, static equivalent pressures are based on the specific panel's response to the air-blast load. Changing dimensions, reinforcement, or supported elements would require recalculation of the static equivalent load and are therefore not recommended. However, when using the static equivalent loads, the designer may proceed normally with the lateral design process, using a load factor of one. Note that equivalent static values are different from quasi-static values which assume a displacement ductility less than one. The equivalent static values are based on computations that are non-linear, with ductilities in excess of one.
For structural pre-cast systems, the connections are the critical issue to be addressed. Connections need to have adequate development lengths and strength to permit the panel to reach its ultimate flexural capacity. Extensive use of transverse walls or an 'egg crate' type of design is an effective way to achieve the needed lateral support (see Figure 7). Special seismic detailing is recommended for structural pre-cast connections.
Masonry
While CIP concrete walls are the material of choice, reinforced masonry, or concrete masonry unit (CMU) walls are common for new blast resistant construction. For blast applications, masonry walls should be grouted and reinforced to produce a ductile response. Typically, vertical centered and regularly spaced reinforced bars will be sufficient for moderate blast loads. For higher blast loads, thicker masonry walls with reinforcing on each face of the wall in each void will be required. Connections into the structure at top and bottom are to resist the ultimate lateral capacity of the wall. For infill walls, avoid transferring loads into the columns if they are primary load carrying elements. The connection details may be very difficult to construct. It will be difficult to have all the blocks fit over the bars, near the top, and it will be difficult to provide the required lateral restraint at the top connection. A preferred system is to have a continuous exterior CMU wall that laterally bears against the floor system. For infill walls, use development lengths that develop the full capacity of the section.
Brick load bearing walls resist blast mostly through mass and so thicker solid walls on the order of 18 inches or so can perform well at pressure levels less than 10 psi or so. Brick walls with Dynamic structural response are computed by using a kinematic model with bearing providing resistance at the hinge points.
Unreinforced masonry is considered a brittle material that may generate highly hazardous flying debris in the event of an explosion and reinforcement is typically provided for new construction.
Metal Stud Systems
Back-to-back metal stud systems may be used for conditions with low to mid-range blast load intensities. These metal studs should be mechanically attached to minimize lateral torsional effects. To catch exterior cladding fragments, attach a wire mesh, steel sheet, or Fiber Reinforced Polymer to the blast loaded side of the metal stud system. However, appropriately sized and spaced single stud wall systems may be designed to resist moderate blast load intensities and relatively short floor to floor heights.
The supports of the wall should be designed to resist the ultimate lateral out-of-plane bending capacity load of the system. This typically requires special connectors to develop the blast reactions. Design guidance for cold-formed steel stud can be found on The Steel Network and by the Cold-Formed Steel Engineering Institute. Special care is required at the connections to prevent failure prior to the stud reaching its ultimate capacity. Deeper, thicker channels are preferred. Additional lateral support using angles or other methods may be needed along the interior to prevent failure.
Enhanced protection may be provided by placing Fiber Reinforced Polymers, geotextile materials, Kevlar or similar materials on the inside face cladding to provide confinement, fragment restraint and added tensile capacity. These materials are to bear directly against the metal studs.
Timber
The use of timber framing is not generally recommended for blast resistant design due to its lack of desirable attributes under explosive threats. However, there is growing research and testing being conducted out of Canada and parts of the United States in particular for engineered lumber such as cross laminated timber (CLT).
Non-Structural Elements
Brick veneers, bris soleil, sunshades and other non-structural elements attached to the building exterior are to be avoided to limit flying debris and improve emergency egress by ensuring that exits remain passable. If used they should be designed using lightweight materials with connections designed to resist the capacity of the element.
Fenestration
Windows are typically the most vulnerable portion of any building. Flying debris from glass shards often account for the largest percentage of injuries in an explosive event. Mitigating these effects is a critical component in the design of blast resistant buildings. Security criteria generally specify either the explosive threat or the loading pressure and impulse to which the blast mitigating windows must be designed. Except for very thick lites, most glazing materials and components will likely be damaged by the blast overpressures. It may be impractical to design all the windows to resist a large-scale explosive attack, and more desirable to limit the amount of hazardous glass breakage to reduce the injuries. Therefore, in addition to the magnitude of blast loading, security criteria dictate the level of damage that is acceptable based on the performance of the window in response to blast loading. For a large-scale vehicle weapon, the pressure range associated with acceptable levels of damage is expected on the sides of surroundings buildings not facing the explosion, or for smaller explosions where pressures drop more rapidly with distance. Generally, we do not know which side of the building the attack will occur on, so all sides need to be protected.
In addition to designing the windows for the applicable blast pressures, there are several architectural approaches that can also be taken. One way is to reduce the number and size of windows, in particular, at the lower levels where pressures are generally higher. If blast resistant walls are used, then fewer and/or smaller windows will cause less air-blast to enter the building thus reducing the interior damage and injuries. Additional approaches include an internal atrium design with windows facing inward not outward; clerestory windows which are close to the ceiling, above the heads of the occupants; and angling the windows away from the curb to reduce the pressure levels.
Window protection should be evaluated on a case-by-case basis by a qualified blast consultant to develop a solution that meets established objectives. A number of generic recommendations are given in Figure 6 for the design of the window systems to reduce injuries to building occupants.
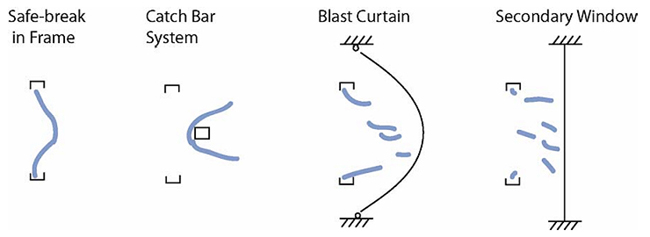
Figure 6. Preferred failure modes for windows. Credit: FEMA 427, Primer for Design of Commercial Buildings to Mitigate Terrorist Attacks (2003)
Glass Design
Glass is often the weakest part of a building, breaking at low pressures compared to other components such as the floors, walls, or columns. Past incidents have shown that glass breakage and associated injuries may extend many thousands of feet in large external explosions. High-velocity glass fragments have been shown to be a major contributor to injuries in such incidents. For incidents within downtown city areas, falling glass poses a major hazard to passersby and prolongs post-incident rescue and clean-up efforts by leaving tons of glass debris on the street. At this time, exterior debris is largely ignored by existing criteria.
Hazard Levels or Performance Condition: As part of the damage limiting approach, glass failure is not quantified in terms of whether breakage occurs or not, but rather by the hazard it causes to the occupants. A description of the hazard rating levels is provided in Table 1 and graphically depicted in Figure 7. Select security criteria will refer to glass performance conditions which correlate to the aforementioned hazard rating levels. The glass performance condition is defined based on empirical data from explosive tests performed in a cubical space with a 10–foot dimension. The performance condition ranges from 1 which corresponds to not breaking, to 5 which corresponds to hazardous flying debris at a distance of 10 feet from the window. Generally, a performance condition 3 (Low Hazard) or 4 (Moderate Hazard) is considered acceptable for buildings that are not at high risk of attack.
Table 1. Hazard Ratings and Descriptions for Windows
Hazard Rating Description | Description of Fenestration Glazing Response |
---|---|
No Break | The glazing is observed not to fracture and there is no visible damage to the glazing system or glazing retrofit system |
No Hazard | The glazing is observed to fracture but is fully retained in the facility test frame or glazing system frame and the rear surface (the side opposite the airblast loaded side of the specimen) is unbroken. |
Minimal Hazard | The glazing is observed to fracture and the total length of tears in the glazing plus the total length of glazing pullout from the frame is less than 50% of the glazing sight perimeter. Also, there are three or less perforations or indents anywhere in a vertical witness panel located 3 m (120 in.) from the interior face of the specimen and there are fragments with a total mass of 15 g (0.033 lbm) or less on the floor of the witness area between 0 to 1 m (0 to 40 in.) from the interior face of the specimen and no fragments in the witness area greater than 1 m (40 in.) from the interior face of the specimen. |
Very Low Hazard | The glazing is observed to fracture and fragments are located 1 m (40 in.) or less from the original interior surface of the specimen. Also, there are six or less perforations anywhere in a vertical witness panel located 3 m (120 in.) from the interior face of the specimen and there are fragments with a total mass of 15 g (0.033 Ibm) or less on the floor of the witness area between 1 and 3 m (40 and 120 in.) from the interior face of the specimen. |
Low Hazard | The glazing is observed to fracture, and fragments generally fall between 1 and 3 m (40 and 120 in.) of the interior face of the specimen. Also there are 25 or less perforations 50 cm (20 in.) or less above the floor of a vertical witness panel located 3 m (120 in.) from the interior face of the specimen and 10 or less perforation high than 50 cm (20 in.) in a vertical witness panel located 3 m (120 in.) from the interior face of the specimen. For perforations in the vertical witness panel, up to 5 of the perforations may penetrate through the full thickness of the fail backed insulation board layer of the witness panel as defined in Test Method F1642. |
Moderate Hazard | The glazing is observed to fracture, and fragments generally fall between 1 and 3 m (40 and 120 in.) of the interior face of the specimen with numerous perforations and penetrations lower than 50 cm (20 in.) in a vertical witness panel located 3 m (120 in.) from the interior face of the specimen. Also there are 25 or less perforations 50 cm (20 in.) or higher above the floor of a vertical witness panel located 3 m (120 in.) from the interior face of the specimen. For perforations, in the vertical witness panel, up to 5 of the perforations may penetrate through the full thickness of the foil backed insulation board layer of the witness panel as defined in Test Method F1642. |
High Hazard | Glazing is observed to fracture and there are more than 25 perforations in the area of a vertical witness panel located 3 m (120 in.) from the interior face of the specimen and higher than 50 cm (20 in.) above the floor or there are more than 5 perforations in the same witness panel area with fragment penetration through the full thickness of the foil backed insulation board layer of the witness panel as defined in Test Method F1642. |
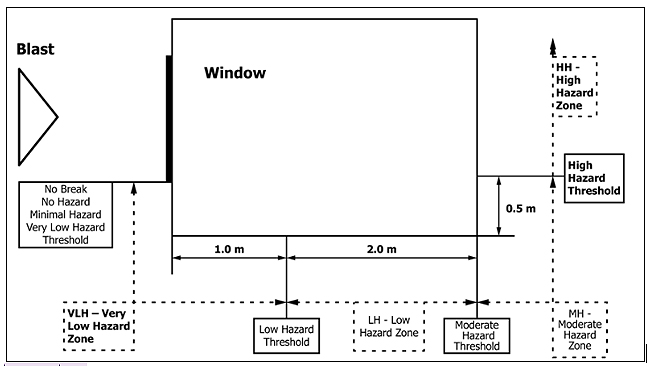
Figure 7. Illustration showing hazard threshholds for windows. Credit: ASTM F1642-17 Standard Test Method for Glazing and Glazing Systems Subject to Airblast Loadings
Window Glazing: Typical annealed glass windows break at low pressure and impulse levels and the shards created by broken windows are responsible for many of the injuries incurred due to large scale explosive attack. The preferred solution for new construction is to use laminated annealed (i.e., float) glass with structural sealant around the inside perimeter. For insulated units, only the inner pane needs to be laminated. The lamination holds the shards of glass together in explosive events, reducing its potential to cause laceration injuries. The structural sealant helps to hold the pane in the frame for higher loads. Annealed glass is used because it has a breaking strength that is about one-half that of heat strengthened glass and about one-fourth as strong as tempered glass thus reducing the loads transmitted to the supporting frame and walls. Using annealed glass becomes particularly important for buildings with light weight exterior walls using for instance, metal studs, dry wall, and brick façade. Use the thinnest overall glass thickness that is acceptable based on conventional load requirements. The preferred interlayer thickness is 60 mil unless otherwise specified by the criteria. This layup has been shown to perform well in low pressure regions (i.e., under about 5 psi). If a 60–mil polyvinyl butaryl (PVB) layer is used, the tension member forces into the framing members need to be considered in design.
To make sure that the components supporting the glass are stronger than the glass itself (balanced design), we specify a window breakage strength that is high compared to what is used in conventional design. The breakage strength in window design may be specified as a function of the number of windows expected to break at that load. For instance, in conventional design, it is typical to use a breakage pressure corresponding to 8 breaks out of 1000. Where we are certain of a lot of glass breakage, a pressure corresponding to 750 breaks out of 1000 is used to have increased confidence that the frame does not fail too. Design criteria vary broadly depending on the specified number of breaks to use for design. Glass breakage strengths may be obtained from window manufacturers. Smaller glass panes generally have higher capacities than larger panes which can significantly increase the loads transmitted to the frames. One way to reduce the loads transmitted to the frames is the use of false or non-structural mullions.
Laminated glass is typically used to improve the post-damage behavior of the glazing systems for new construction whereas anti-shatter film is typically applied to existing glazing. While these features may do little to improve the strength of the glass, they hold the shards of glass together and better protect the occupants from hazardous debris (see also WBDG Glazing Hazard Mitigation). The effectiveness of Mylar films depends on the method of application and the thickness of the film. Common film systems range from a simple edge-to-edge (daylight) application to a wet glazed adhesion, to a mechanical attachment to the existing window frame. Mechanical attachments are most effective when they are anchored to the underlying structure. Regardless of the method, there are architectural issues and life-cycle costs associated with the use of anti-shatter films.
There are several government sponsored software products available to evaluating the response of window glass, including SBEDS_W and WINGARD. These codes are made available to government contractors who have government projects requiring this type of analysis.
Glass block is generally not recommended because of the heavy projectiles these walls may create due to failure at the mortar lines. However, there are blast rated glass block products that are available in which each glass block is framed by a steel grate system. Glass walls or windows should generally be avoided at emergency exits to facilitate egress. Projectile impact loads are not typically considered for air-blast as they are for wind loads. However, Dade County certified windows for hurricanes may have a higher level or inherent blast resistance compared with other conventional window types. Impact resistant systems need to be checked to determine whether they meet the air-blast design criteria. Inoperable window solutions are generally recommended for air-blast mitigating designs. However, there are operable window solutions that are conceptually viable. For instance, designs where the window rotates about a horizontal hinge at the head or sill and opens in the outward direction. For this design, the window will slam shut in an explosion event. If this type of design is used, the governing design parameter may be the capacity of the hinges and/or hardware.
Recognizing that designing the entire façade for the maximum blast pressures may not be practical, certain security criteria will allow for a reduced 90% of the façade to meet the performance criteria. Still, glazing systems that are capable of resisting a specified overpressure require a cascade of costly upgrades to the façade, including thick laminated glass assemblies, and relatively heavy frames. There are also major construction challenges such as reinforcement and steel embedment that may get in the way of new cast-in-place reinforced concrete wall construction, and the substantial anchorage required to accommodate the large reaction forces. Moreover, attaching these window systems to existing walls may even be a physical impossibility, see WBDG Retrofitting Existing Buildings to Resist Explosive Threats. Since the improved capacity may fall short of the pressures associated with a realistic terrorist threat, the protective design engineer for new construction with low threat criteria and limited budgets for blast protection may decide to select the weakest laminated glazing that satisfies wind and serviceability requirements. The improved post failure behavior associated with this limited approach provides the occupants with a measure of protection at a reasonable cost.
Mullion Design
The frame members connecting adjoining windows are referred to as mullions. These members may be designed in two ways. Either a static approach may be used where the breaking strength of the window glass is applied to the mullion, or a dynamic load may be applied using the peak pressure and impulse values. A static approach may lead to a design that is not practical. Using this approach, the mullion can become very deep and heavy, driving up the weight and cost of the window system. It may also not be consistent with the overall architectural objectives for the project.
Sometimes cables or steel bars or tubes are placed behind the glass to prevent the glass from entering the interior. The State Department refers to this as the 'muntin' system when the glass bears against steel bars arranged in a cruciform shape. The Defense Department refers to a similar system with a single bar placed behind the glass as a 'catch-bar' system. For these types of systems the steel members are attached using full penetration welds and are able to experience large ductile deformations. Structural wood mullions have negligible resistance and should not be used for blast mitigating designs.
Frame and Anchorage Design
Equally important to the design of the glass is the design of the window frames. For the window to properly fail, the glass must be held in place long enough to fail. Short of that, the glazing will dislodge from its housing and cause serious damage or injury. The bite, including the possible use of structural silicone sealant, must be adequate to retain the failed glass within the frame. The window bite (i.e., the depth of window captured by the frame) needs to be at least ½ inch. The structural sealant recommendations should be determined on a case-by-case basis. In some applications, the structural sealant may govern the overall design of the window systems. In most conventionally designed buildings, the frames will be aluminum. In some applications, where the windows are designed to resist high pressures, steel bar inserts, cable inserts or built-up steel frames may be used. Also, in lobby areas where large panes of glass are used, a larger bite with more structural sealant may be needed.
Depending on the façade, the framing may be designed to span from floor to floor or tie into wall panels and must be capable of resisting the glass reaction forces. Some design modifications may be required to the connections, details, and member profiles to optimize the performance. In some cases, member depths or wall thicknesses may be increased and in other cases, members may be reinforced with steel bars or channels.
For reinforced concrete construction designed to resist high pressure loads, as is typical for embassy construction, anchorage of the steel window frames is provided by steel studs welded to a steel base plate. For this type of construction, the frame is typically constructed using a steel stop at the interior face and an angle with an exposed face at the exterior face. The frame is attached to the base plate using high strength fasteners. Coordination is required to properly arrange the fastener locations for the steel frame, the steel studs, and the rebar cage. For masonry walls, metal straps are recommended for anchoring the window into the wall.
The frame system may either be designed to resist the reaction forces associated with the magnitude of the blast loading or it may be designed to exceed the capacity of the glazing. This is often referred to as balanced design, capacity design or the "glass fail first" criteria. The balanced design philosophy means that the glass will fail at pressure levels that do not exceed that of the frame, anchorage and supporting wall system. If the glass is stronger than the supporting members, then an entire panel may enter the building as a single unit, possibly with the frame, anchorage and the wall attached. This failure mode is considered more hazardous than if the glass fragments enter the building, and by using a damage limiting approach, the damage sequence and extent of damage is controlled.
Supporting Wall Design
A similar approach may be used for checking the supporting wall response. It does not make sense and is potentially highly hazardous to have a wall system that is weaker than windows that it is supporting. If the walls are unable to accept the loads transmitted by the mullions the mullions may need to be anchored into the structural slabs or spandrel beams. Anchoring into columns is generally discouraged because it increases the tributary area of lateral load that is transferred into these members and may cause instability.
Some window/wall designs will require additional support around the windows. For clerestory windows, the supporting wall is acting largely as a cantilever and will need to be supported with vertical braces spanning floor to ceiling. For punched wall systems with narrow pilasters between them, vertical braces may also be needed. For lighter wall systems like metal stud systems, double studs framing the window are recommended.
The balanced design approach is particularly challenging in the design of ballistic resistant and forced entry resistant windows, which consist of one or more inches of glass and polycarbonate. These windows can easily become stronger than the supporting wall. In these cases, windows may need to be designed for the design threat air-blast pressure levels and implicitly accept that for larger loads balanced design conditions will not be met.
Curtain Wall Protection
A curtain wall is a nonbearing exterior enclosure that is supported by a building's structural steel or concrete frame and holds either glass, metal, stone, or precast concrete panels. Lightweight and composed of relatively slender extruded aluminum members, curtain-wall façades are considerably more flexible than conventional, hardened punched window systems. Glass curtain wall systems have been determined to perform surprisingly well in recent explosive tests. These systems have been shown to accept large deformations without the glass breaking hazardously compared to rigidly supported punched window systems. The framing members absorb a portion of the blast energy, and this improves the performance of the glazing.
It is important to consider the inherent flexibility of curtain-wall systems when sizing framing members for blast loads and evaluating the glazing for hazard. This enables the engineer to both ascertain the true blast worthiness of the curtain wall as well as to properly calculate the reduced load transfer into supporting structural elements. The design of curtain-wall systems to withstand the effects of explosive loading depends on the performance of the various elements that comprise the system. Curtain-wall response software, based on more sophisticated finite element methods than simplified Single-Degree-of-Freedom glass fragment hazard analytical approaches, was developed for the Department of Defense, Technical Support Working Group (TSWG) to accurately represent the capacity of the glazing and the supporting frame members. While the glazing may be the most brittle component, the performance of the system, and the reduction of hazard to the occupants depend on the interaction between the capacities of the various elements. In addition to hardening the individual members that comprise the curtain-wall system, the attachments to the floor slabs or spandrel beams require special attention. These connections must be adjustable to compensate for the fabrication tolerances and accommodate the differential inter-story drifts and thermal deformations as well as be designed to transfer gravity loads, wind loads, and blast loads. Generally, the blast loads are significantly greater in magnitude than wind loads.
Energy-Absorbing Catch Systems and Anchors
An alternative approach to blast resistant protective design takes the concept of a flexible curtain-wall system one step further by making full use of the flexibility and capacity of all the window materials to absorb and dissipate large amounts of blast energy while preventing debris from entering the occupied space. Energy-absorbing catch systems (a.k.a. Cable Protected Window Systems (CPWS)) work in such a way that as the glass is damaged it bears against a cable catch system, which in turn deforms the window frames. Extensive explosive testing, as well as sophisticated computer simulations, has demonstrated the effectiveness of these systems.
Energy absorbing anchors similarly dissipate significant portions of the blast energy through the controlled deformation and damage, thereby transferring reduced blast reaction forces to the surrounding walls and structure. The performance of the energy dissipating system may be demonstrated with acceptable explosive (or shock tube) test data, conducted in accordance with ASTM F1642/Fl642M, or through the use of detailed analytical methods that have been validated with test data.
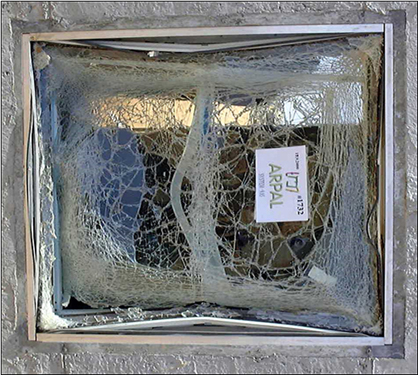
Figure 8. Sample catch system
Other Openings
Doors are handled differently in different criteria. Most criteria neglect the response of door systems. This may be for several reasons. Doors that are capable of resisting air-blast loads can be very expensive and their connections may require for supporting structure to be reinforced. Also, doors are typically in transitory areas where people do not stay for very long. Some concepts for increasing the inherent resistance of doors are as follows:
- Use double steel doors with internal cross braces
- Orient doors to open outward so that they bear against the jamb during the positive pressure loading phase
- Fill the jambs with concrete to increase their strength
- Increase number of fasteners used to connect door into wall system
- Do not station guards or other persons directly behind doors
- Position doors so that they will not be propelled into rooms if they fail
In general sliding glass doors should be avoided. The typical failure mode for these door systems is along the channel supporting the framed glass. If these systems are used, this channel needs to be able to restrain the glass and to have anchors that are designed to resist the strength of the glass.
For revolving doors, use laminated glass and provide an increased bite in the frame. Louvers are another type of opening to consider. These members should be designed with connections that are able to resist the flexural capacity of the louver. A catch system behind the louver is another approach using a well anchored steel grate. Air intakes that are at or close to the ground level should always have grates so that weapons cannot be lobbed into them. Also consider using a sloped grating for horizontal air intakes so that a potential weapon can roll off prior to detonation. Air intakes at or near ground level locations where chemical, biological, or radiological (CBR) attack may occur are to be avoided. (See WBDG Design Guidance Page Security for Building Occupants and Assets)
Roof
The primary loading on the roof is the downward air-blast pressure. The exterior bay roof system on the side(s) facing an exterior threat is the most critical. Roof systems which are low and therefore closer to the explosion will be subject to higher pressures than high roof systems. The air-blast pressures on the interior bays are less intense and may require less hardening. Secondary loads include upward pressure due to the air-blast penetrating through openings and upward suction during the negative loading phase. The upward internal pressures may have an increased duration due to multiple reflections of the internal air-blast wave. It is conservative to consider the downward and upward loads separately.
To provide redundancy, roof bay dimensions less than or equal to 30 feet are preferred. The preferred system is to use cast-in-place reinforced concrete with beams in two directions. If this system is used, beams should have continuous, symmetrical top and bottom reinforcement with tension lap splices. Shear ties should develop the bending capacity of the beams and be closely placed along the entire span. All ties are to have a 135–degree bend minimum. Two-way slabs are preferred.
Somewhat lower levels of protection are afforded by conventional steel beam construction with a steel deck and concrete fill slab. The performance of this system can be enhanced by use of normal weight concrete fill, increasing the gauge of welded wire fabric reinforcement, and making the connection between the slab and beams with shear connector studs. Tension membrane behavior along the edges should be considered in the design of the connections. Since it is anticipated that the slab capacity will exceed that of the supporting beams, beam end connections and supporting columns should be capable of developing the ultimate flexural capacity of the beams to avoid brittle failure. Beam to column connections should be capable of resisting upward as well as downward forces.
Pre-cast and pre/ post-tensioned systems including hollow plank are generally viewed as less desirable due to the lack of ductility. If they are used, a system that has continuous bond with the concrete is preferred, with anchors which are designed to be protected from direct air-blast effects. Also, additional mild reinforcement top and bottom is recommended to provide a ductile response. Connections need to be designed to resist both the direct and uplift forces. Concrete flat slab/ plate systems are also less desirable because of the potential of shear failure at the columns, but these may be feasible for lower levels of protection. Where flat slab/ plate systems are employed, they should include features to enhance their punching shear resistance. Continuous bottom reinforcement should be provided through columns in two directions to retain the slab in the event that punching shear failure occurs. Edge beams should be provided at building exterior.
Lightweight systems, such as untopped steel deck or wood frame construction are considered to afford negligible resistance to air-blast. These systems are prone to failure due to their low capacity for downward and uplift pressure. In general, the roof systems should be designed to resist the actual loads associated with the defined threat. Because roof systems are high up and not exposed to the reflected wave, they are subject to lower pressures than the walls. Sloped roofs may be subject to somewhat higher pressures and are usually of lighter construction than flat roof systems making them particularly vulnerable to air-blast effects. For this reason, sloped systems should be avoided.
Gravel on roof systems may become air-borne debris like what happens for wind loads. However, because of the severity of explosive loads and the short duration compared with wind, this is considered a secondary effect that is not explicitly addressed in the criteria documents.
Skylights in roof systems create a falling fragment hazard to occupants below. These should be designed with a catch system beneath or designed to remain in the frame for the design load. Ideally, skylights should be placed as far from the weapon as possible to keep the pressures low. Similar concepts apply for atria with multistory glass walls. Parapets, roof mechanical room enclosures, and tile roof systems exterior to the building are generally not a primary concern since they are exterior to the building. Generally, these members are designed to sustain heavy damage but not become flying debris. Although roofing aggregate may become a flying hazard, in the context of an explosion event this hazard is not significant enough to warrant much concern.
Details
The following details are from UFC 3-340-02 and can be viewed online in Adobe PDF (Portable Document Format) by clicking on the PDF icon to the right of the drawing title. Download Adobe Reader.
Figure 5–27 Typical connections for cold-formed steel panels
Figure 6–2 Masonry wall with rigid support
Figure 6–5 Special masonry unit for use with reinforcing bars
Relevant Codes and Standards
Federal Guidelines
- Department of Defense (DOD)
- Unified Facility Criteria (UFC)
- UFC 1-200-01, DoD Building Code
- UFC 4-010-01, DoD Minimum Anti-Terrorism Standards for Buildings—Establishes prescriptive procedures for Threat, Vulnerability and Risk assessments and security design criteria for DoD facilities.
- UFC 4-020-01, DoD Security Engineering Facilities Planning Manual—Provides requirements for security and anti-terrorism.
- UFC 4-023-03, Design of Buildings to Resist Progressive Collapse
- Unified Facility Criteria (UFC)
- Department of State
- Overseas Building Operations (OBO) Design Standards including Appendix P: Physical Security Standards Handbook
- Overseas Building Operations—International Codes Supplements (OBO-ISC)
- General Services Administration (GSA)
- Department of Homeland Security (DHS)
- The Risk Management Process—An Interagency Security Committee Standard including Appendix A, Appendix B, and Appendix C— Defines criteria for determining facility security level, determination of the design basis threat, and provides physical security countermeasures for all nonmilitary federal facilities
- Department of Veterans Affairs (VA)
Additional Resources
Publications
- ASTM International, ASTM F1642/F1642M Standard Test Method for Glazing and Glazing Systems Subject to Airblast Loadings
- ASTM International, ASTM F2912 Standard Specification for Glazing and Glazing Systems Subject to Airblast Loadings
- BIPS 05 Preventing Structures from Collapsing by the Department of Homeland Security.
- Bomb Threat Stand-Off Card by the Department of Homeland Security (DHS) and Department of Justice (DOJ)
- Building Security: Handbook for Architectural Planning and Design by Barbara A. Nadel, FAIA, McGraw-Hill, 2004.
- Building Security through Design: A Primer for Architects, Design Professionals, and their Clients by The American Institute of Architects.
- The Comprehensive Plan for the National Capital by the National Capital Planning Commission.
- Design of Blast Resistant Buildings in Petrochemical Facilities by the American Society of Civil Engineers.
- JCAT Counterterrorism Guide for Public Safety Personnel by the Office of the Director of National Intelligence.
- Safety/Security Window Film by the International Window Film Association
- Structural Design for External Terrorist Bomb Attacks by Jon Schmidt.
- Table of distances for storage of explosive materials (high) by the Bureau of Alcohol, Tobacco, Firearms, and Explosives.