Introduction
Within This Page
Combined heat and power (CHP), or cogeneration, is the simultaneous generation of useful mechanical and thermal energy in a single, integrated system. CHP can be configured as a topping or bottoming cycle. In a typical topping cycle system, fuel is combusted in a prime mover, such as reciprocating engines, combustion or gas turbines, steam turbines, microturbines, or fuel cells, which drives the overall system to generate electricity. In a bottoming cycle system, also referred to as "waste heat to power," fuel is combusted to provide thermal input to a furnace or other industrial process and heat rejected from the process is then used for electricity production.
CHP involves the recovery of otherwise-wasted thermal energy to produce useful thermal energy or electricity. This can significantly increase industrial efficiency and decrease unnecessary fuel consumption. CHP already has a large presence in the U.S., with 4,300 installations in all 50 states and 130 GW of remaining technical potential for electricity generation . Additionally, CHP is recognized for its potential to significantly reduce carbon emissions and to reliably generate power, even during emergency situations. Although CHP represents a significant up-front investment, it can pay for itself within a few years.
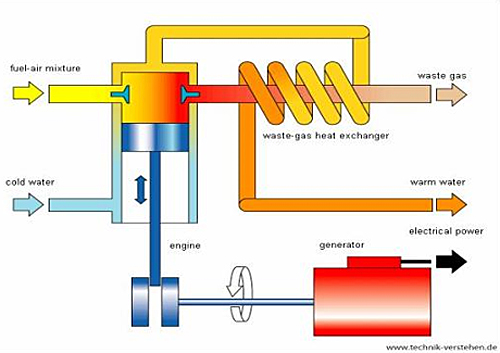
Source: Responsible Business- European e-Learning Module
Description
A. Types of CHP Prime Movers:
CHP SYSTEM | ADVANTAGES | DISADVANTAGES | AVAILABLE SIZES |
---|---|---|---|
Gas Turbine | High reliability. Low emissions. High-grade heat available. No cooling required. | Require high-pressure gas or in-house gas compressor. Poor efficiency at low loading. Output falls as ambient temperature rises. | 500 kW to 300 MW |
Microturbine | Small number of moving parts. Compact size and lightweight. Low emissions. No cooling required. | High costs. Relatively low mechanical efficiency. Limited to lower temperature cogeneration applications. | 30 kW to 250 kW with multiple unit packages up to 1,000 kW |
Spark ignition (SI) reciprocating engine | High power efficiency with part-load operational flexibility. Fast start-up. Relatively low investment cost. Has good load following capability. Can be overhauled on site with normal operators. Operate on low-pressure gas. | High maintenance costs. Limited to lower temperature cogeneration applications. Relatively high air emissions. Must be cooled even if recovered heat is not used. High levels of low frequency noise. | 1 kW to 10 MW in DG applications |
Compression ignition (CI) reciprocating engine (dual fuel pilot ignition) | High speed (1,200 RPM) ≤4MW | ||
<80 MW for Low speed (60-275 RPM) | |||
Steam Turbine | High overall efficiency—steam to power. Can be mated to boilers firing a variety of gaseous, liquid or solid fuels. Ability to meet more than one site heat grade requirement. Long working life and high reliability. Power to heat ratio can be varied. | Slow start up. Very low power to heat ratio. Requires a boiler or other steam source. | 50 kW to several hundred MWs |
Fuel Cells | Low emissions and low noise. High efficiency over load range. Modular design. | High costs. Fuels require processing unless pure hydrogen is used. Sensitive to fuel impurities. Low power density. | 5 kW to 2 MW |
Source: EPA Combined Heat and Power Partnership
B. Features of CHP Technology
Installed Cost
The installed cost for most CHP technologies consists of the total equipment cost plus installation labor and materials, engineering, project management, and financial carrying costs during construction.
Operation and Maintenance (O&M) Cost
Non-fuel operation and maintenance (O&M) costs typically include routine inspections, scheduled overhauls, preventive maintenance, and operating labor. O&M costs are comparable for gas turbines, gas engines, steam turbines, and microturbines, and only a fraction higher for fuel cells.
Start-Up Time
Start-up times represent how long it takes CHP units to get online and be able to provide electricity and thermal output. Start-up times for the five CHP technologies described above can vary significantly depending on the technology and fuel used.
Availability
Availability indicates the amount of time a unit can be used for electricity and/or steam production. Availability generally depends on the operational conditions of the unit.
Thermal Output
The ability to produce useful thermal energy from exhaust gases is the primary advantage of CHP technologies. This value is equivalent to the gross useful thermal output of the CHP system minus the thermal input.
FEATURE OF CHP TECHNOLOGY | TYPE OF CHP PRIME MOVER | ||||
---|---|---|---|---|---|
Gas Turbine | Microturbine | Reciprocating Engine | Steam Turbine | Fuel Cell | |
Installed Cost ($/kW) | Ranges from 1,200 to 3,300 | Ranges from 2,500 to 4,300 | Ranges from 1,500 to 2,900 | Ranges from 670 to 1,100 | Ranges from 5,000 to 6,500 |
Non-fuel O&M Cost ($/kWh) | Ranges from 0.009 to 0.013 | Ranges from 0.009 to .013 | Ranges from 0.009 to 0.025 | Ranges from 0.006 to 0.01 | Ranges from 0.032 to 0.038 |
Start-Up Time | 10 min–1 hr | 60 sec | 10 sec | 1 hr–1 day | 3 hrs–2 days |
Availability | 93–96% | 98–99% | 96–98% | Near 100% | >95% |
Uses for thermal Output | Heat, hot water, low-pressure and high-pressure steam | Hot water, chiller, heating | Space heating, hot water, cooling, low-pressure steam. | Process steam, district heating, hot water, chilled water | Hot water, low-pressure and high-pressure steam |
Source: EPA Combined Heat and Power Partnership
C. Economics of CHP
CHP systems are major investments. For instance, a 1 MW reciprocating engine system for a hospital might have a capital cost of around $1.6 million. The cost of a CHP system depends on the complexity of its secondary features, such as heat recovery and emissions monitoring systems. Generally, costs for CHP per kilowatt of capacity decrease as size increases. Given the efficiency gains from CHP, however, some analysts estimate that it can be implemented at a negative cost because cost savings from reduced fuel expenditures will outweigh capital and other project costs over the life of the system.
Despite its high initial costs, CHP is cost-effective and offers a variety of long-term economic benefits:
Offset capital costs: CHP can be installed in place of boilers or chillers in new construction projects, or when major heating, ventilation, and air conditioning (HVAC) equipment needs to be replaced or updated. Additionally, CHP avoids the need to build costly, hazardous high-voltage lines. Based on projections that the U.S. will need to install 137,000 MW of new electric transmission and generation capacity, relying on distributed generation rather than central plants would save $136 billion of capital investment and reduce the cost of new power by about three cents per kW .
Reduced energy costs: The high efficiency of CHP technology results in energy savings compared to conventional, separately purchased power, and on-site thermal energy systems. CHP users are insulated from volatile electricity prices. Moreover, by doubling the useful energy products derived from their fuel, CHP hosts can slash their fuel costs. For instance, the BMW plant in Spartanburg, SC reduced its annual energy costs by $5-7 million after installing two CHP gas turbines in 2009 .Hedge against volatile energy prices: CHP can provide a hedge against unstable energy prices by allowing the end user to supply its own power during times when prices for electricity are very high. In addition, a CHP system can accept a variety of inputs including natural gas, biogas, coal, biomass, and build in fuel-switching capabilities to shield against high fuel prices.
More flexible funding: CHP plants can be activated faster and in more flexible increments than traditional electricity generating units (EGUs). They have a direct linkage between the generation and the consumption to meet the power supply needs that accompany economic growth.
D. Benefits of CHP
CHP offers a variety of commercial and societal benefits; including improved environmental quality, grid reliability, and energy efficiency.
Sustainability
CHP can substantially reduce emissions of carbon dioxide and air pollutants like nitrogen oxide, sulphur dioxide and volatile organic particles. By using the fuel's energy twice, CHP yields one-half to one-third of the emissions of the separate generation of heat and power. According to the U.S. Department of Energy, meeting the Agency's goal to double U.S. installed capacity to 40 GW by 2020 would reduce annual greenhouse gas emissions by at least 150 million metric tons of carbon. CHP also avoids emissions associated with conventional power plants, which are responsible for two-thirds of the nation's annual sulfur dioxide emissions, one-quarter of the nitrogen oxide emissions, one-third of the mercury emissions, and one-third of the carbon dioxide emissions. These emissions contribute to serious environmental problems, including global climate change, acid rain, haze, acidification of waterways, and eutrophication of critical estuaries.
Reliability
CHP systems are relatively small and widely distributed. Because they are located at the point of use, they are not vulnerable to a disruption of the transmission system and can provide emergency power in the case of an outage due to extreme weather events. CHP systems are independently fueled and operated. While such systems can be centrally dispatched, they can also be operated effectively in the event of a disruption to central systems if specially configured for "islanding."
Also, distributed energy resources like CHP reduce electricity infrastructure vulnerability. These features make CHP installations less vulnerable than central power plants to disruption. CHP also generally uses secure natural gas or other domestic fuels, reducing vulnerability to a volatile fuel market. CHP can increase the reliability of a building's power supply - a substantial advantage in today's changing electricity market and high-tech society. A highly reliable power supply is vital to some companies' computing, manufacturing, and research functions and essential for critical infrastructure like hospitals and wastewater treatment plants.
Efficiency
Combined heat and power is an efficient and clean approach to generating power and thermal energy from a single fuel source. The average efficiency of fossil-fueled power plants in the United States is 33 percent, and has remained virtually unchanged for four decades. This means that two-thirds of the energy entering the system is lost as waste heat. However, CHP systems typically achieve total system efficiencies of 60 to 80 percent. Because CHP is more efficient, less fuel is required to produce a given energy output than with the separate production of heat and power.
As an efficiency technology, CHP helps makes businesses more competitive by lowering their energy costs, reducing demand on the electricity delivery system, and reducing strain on the electric grid. Such on-site generation avoids the transmission and distribution losses associated with electricity purchased via the grid from central stations and defers or eliminates the need for new investment. CHP's inherent higher efficiency and elimination of transmission and distribution losses from the central station generator, results in reduced primary energy use and lower GHG emissions. CHP can provide overall energy and CO2 savings on par with comparably sized solar PVs, wind, and natural gas combined cycle (NGCC), and at a capital cost that is lower than solar and wind and on par with NGCC.
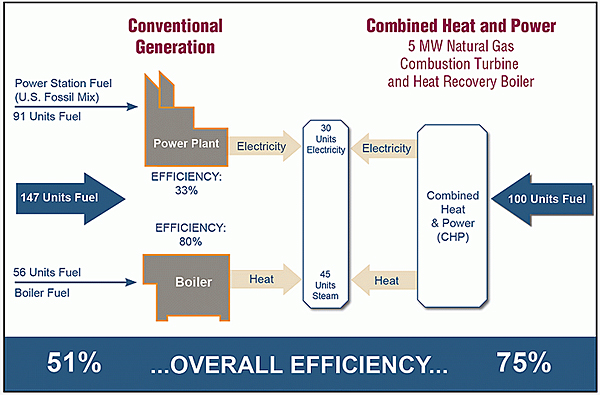
Source: EPA Combined Heat and Power Partnership
Applications
Commercial/Institutional Buildings
Commercial buildings used over 16 quadrillion BTUs of energy in 2000—equivalent to the annual gasoline consumption in the U.S. There is great potential for CHP in large commercial office buildings, supermarkets, hotels, restaurants, and large retail markets. Mixed-use developments are an emerging market for CHP, especially due to the clean, reliable on-site power they provide. Recent ICF projections predict equal technical potential of 65 GW in the industrial and commercial/institutional sectors.
Hospitals
Hospitals are excellent candidates for CHP because they have high electrical and thermal energy needs and because reliability is critical. A 2 MW gas turbine CHP system can provide annual O&M savings of more than $400,000. Also, CHP enhances the quality of power by assuring smooth operation of clinical devices.
District Energy
District energy systems may be installed at large, multi-building sites such as universities, hospitals, airports, and government complexes. District energy systems are a growing market for CHP because they significantly expand the thermal load potentially served by the system. District energy also has a major added benefit of reducing the requirement for size and capital investment in production equipment due to the diversity of consumer loads, enabling more cost-effective CHP.
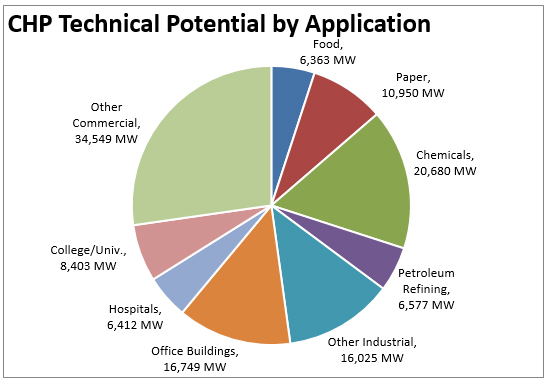
Source: ICF International Internal Estimates, July 2014.
Emerging Issues
Unclear Utility Value Propositions
Since CHP does not depend on central power, it reduces revenue for many investor-owned utilities where business models link sales to cost recovery and revenues. Utility tariff structures and standby rates directly affect onsite CHP generation. Similarly, interconnection processes can delay projects and require costly studies or onerous technical specifications to develop and install a system.
Market and Non-Market Uncertainties
Because CHP equipment requires substantial upfront costs and has a long life (exceeding 20 years), potential hosts must make a long-term financial commitment. Energy efficiency is maximized when a system is sized to match a facility's thermal load. This often results in more power than the host site needs. In some jurisdictions, this excess power production can be sold to the grid, but raises questions about long-term electricity pricing.
Local Permitting and Siting Issues
CHP installations must comply with many local zoning, environmental, health, and safety requirements. This requires interaction with a number of local agencies, including fire districts, water districts, and planning commissions, which are largely unfamiliar with CHP. While CHP systems reduce regional emissions because the facility now produces electricity, on-site emissions will increase, which may prevent hosts from pursuing projects.
Relevant Codes, Standards, and Guidelines
- 26 U.S. Code § 48 (a) (3) (A)
- Distributed Energy Interconnection Procedures Best Practices for Consideration
- Executive Order 13624, "Accelerating Investment in Industrial Energy Efficiency"
- Methodology for Modeling Combined Heat and Power for EAp2/c1 in LEED 2009
- Modified Accelerated Cost Recovery System (MACRS)
Additional Resources
State and Federal Agencies
- California Energy Commission
- DOE Office of Energy Efficiency and Renewable Energy, CHP Basics
- EPA Combined Heat and Power Partnership
- HUD Office of Environment and Energy
- New York State Energy Research and Development Authority (NYSERDA) Combined Heat and Power Systems
Associations and Organizations
- The Combined Heat and Power Alliance
- American Council for an Energy-Efficient Economy
- Center for Climate and Energy Solutions
- Combined Heat and Power Alliance
- Heat is Power Association
- International District Energy Association
- International Energy Agency Technology Collaboration Programme on District Heating and Cooling including Combined Heat and Power
- Pew Charitable Trusts
- State and Local Energy Efficiency Action Network
- World Alliance for Decentralized Energy
Reports
- "Challenges Facing Combined Heat and Power Today: A State-By-State Assessment"
- "CHP: A Clean Energy Solution"
- "Combined Heat and Power: Effective Energy Solutions for a Sustainable Future"
- "Guide to Using Combined Heat and Power for Enhancing Resiliency and Reliability in Buildings"
- The Market and Technical Potential for Combined Heat and Power in the Commercial/Institutional Sector
- "The Opportunity for CHP in the United States
- "Portfolio Standards and the Promotion of Combined Heat and Power"
- "Promoting Combined Heat and Power (CHP) for Multifamily Properties"
- "Standby Rates for Consumer-Sited Resources: Issues, Considerations, and the Elements of Model Tariffs"