Introduction
Within This Page
The innovative design of building enclosures relies less on successful past precedents than the application of building science. This is not because there is little to be learned from existing buildings, but is due to the changes in materials and methods that result from building technology innovation. Combined with growing expectations for high performance, building enclosure design is now required to satisfy a large number of performance parameters that were not given a great deal of consideration in the past. Building enclosures were always expected to be durable and provide a degree of environmental separation, but now they must address issues like energy efficiency, daylighting, indoor air quality, fire safety, thermal comfort, and carbon footprint. There is now a need to explicitly ensure these performance objectives are fully satisfied at the design stage.
Performance: the level of service provided by a building material, component or system, in relation to an intended, or expected, threshold or quality.
Performance-based design is not a new idea and in fields like structural engineering, limit states design has been deployed to reliably achieve appropriate levels of performance. There remain a number of challenges to overcome before a similar approach is available for building enclosure design. Until such time, the information that follows is intended to provide a practical framework for applying building science principles and strategies to the design of well performing building enclosures.
Before continuing with this Resource Page, it is highly recommended to review a summary of building science Vocabularyi in order to be consistent with the terminology used throughout the building science series of WBDG Resource Pages.
For those interested in knowledge enrichment, access Historical Development of the Building Enclosure to understand how ideas and technology have evolved.ii
Description
Principles of Enclosure Design
The requirements for wall performance were outlined some half a century ago (Hutcheon 1963)iii, and are applicable to all enclosure systems and components. The major considerations were identified as:
- Strength and rigidity
- Control of heat flow
- Control of air flow
- Control of water vapor flow
- Control of liquid water movement
- Stability and durability of materials
- Fire
- Aesthetic considerations
- Cost
Since Hutcheon's time, additional objectives have been adopted, such as consideration of the environmental impacts associated with building methods and materials, and the need to provide safe and secure buildings. The objectives or requirements for acceptable wall performance were implicit within traditional methods and materials of construction. With the advent of modern building science, these objectives became more explicit in response to technological innovation. Table 1 summarizes contemporary performance requirements and their corresponding assessment parameters.
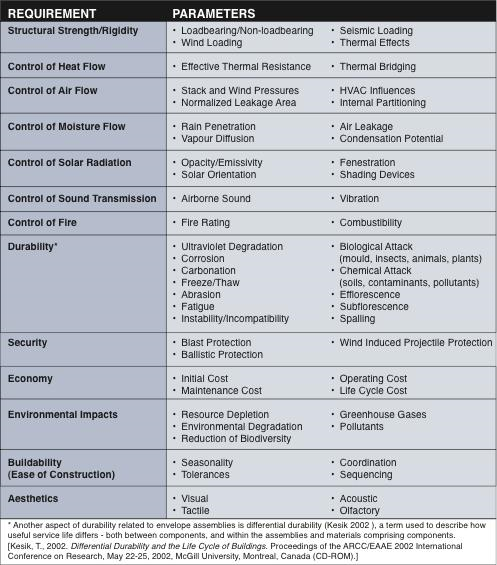
Table 1. Performance requirements for building enclosures and their corresponding assessment parameters.
Separator Versus Moderator
A critical principle in building science involves the difference between environmental separation versus moderation. For example, the control of fire and smoke movement is understood to be a strategy that attempts to completely separate smoke and fire from the indoor environment. The strategy employs a fire-rated assembly that fully controls the leakage of smoke by virtue of its airtight construction and in some cases, the control of air pressures between compartmentalized spaces.
Moderation involves a strategy where the severity of the difference between the indoor and outdoor environments (or two adjacent indoor environments) is moderated within a tolerable threshold. For example, the control of heat transfer does not seek to reduce the rate of heat transfer to zero, rather to a level that satisfies requirements for comfort, energy efficiency and the control of condensation/wetting. Table 2 summarizes key control strategies for the design of building enclosures, most of which involve a moderation strategy rather than a separator or 'perfect barrier' strategy.
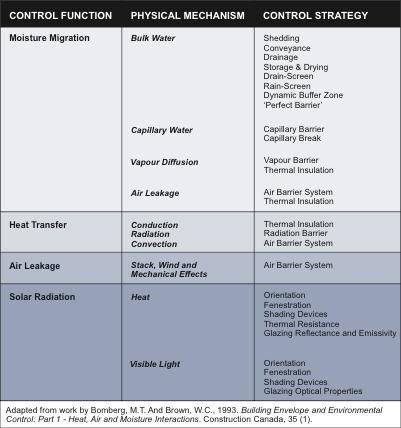
Table 2. Fundamental strategies for the control of heat, air, moisture and solar radiation in the design of building enclosures.
A review of the physical phenomena and corresponding control strategies indicates the control of moisture migration is by far the most important control function to be addressed by the designer. Moisture related problems in buildings are common and broadly vary in types and consequences. A brief listing of moisture related problems illustrates this point: frost heaving, adfreezing, water leakage, wood rot, mold growth, spalling, efflorescence, corrosion, and deterioration and staining of finishes. Consequences range from structural failure to cosmetic flaws, and in some cases the health of the occupants can be adversely affected as in the case of mold growth causing allergic and respiratory problems.
The list of the harmful effects of water in building materials and assemblies is indeed a long one. In many instances the water by itself is not harmful, and only when combined with other phenomena does it cause rapid deterioration. On the other hand, the other phenomena involved will not cause deterioration in the absence of water. It follows then that if water can be controlled a building can be made more durable and the maintenance and repair costs reduced. If this could be achieved only by the use of very expensive materials and construction it could be argued that it is better to let the building deteriorate and to replace the damaged portion from time to time. In fact, however, durable construction can be achieved with relatively inexpensive materials and designs, provided that the designer understands the behavior of water in its various forms and applies the necessary controls to prevent it from accumulating in harmful quantities.iv
Addressing the control of moisture in building enclosure design generally takes precedence over other control measures simply because so many of the requirements for the control of heat transfer, air leakage and solar radiation are satisfied when all forms of moisture management have been carefully considered.
A number of related pages are dedicated to explaining these various control strategies in depth:
For the purpose of applying building science effectively, it is important to appreciate the building enclosure is the primary environmental separator/moderator. It performs a passive role, unlike mechanical and electrical systems that actively supplement the amount of heat, air, moisture and daylight the enclosure is unable to provide. When all active systems fail, the building enclosure is the last line of defense between the indoors and the outdoors. High-performance building enclosures provide passive survivability during extreme weather phenomena and natural disasters, and safely shelter their inhabitants. The following section outlines a number of critical relationships and factors involved in the design of building enclosures.
Design, Materials, Workmanship
In order to appreciate the approaches involved in building enclosure system design strategies, it is important to understand several key relationships that impact performance.
Workmanship and materials are imperfect. If it is likely for a set of working drawings and specifications to contain errors and omissions, then it is almost a certainty that the translation of these instructions to contractors and their trades will be imperfect. Inaccuracy and inconsistency of workmanship and materials, in conjunction with variable weather conditions, result in buildings that only approximately fulfill their design intent.
Management approaches with respect to physical phenomena affecting the building enclosure system are shown through experience to be superior to barrier approaches. Not only do they provide redundancy of critical control functions, but they are more forgiving to construct, since tolerances are greater than those required by a barrier approach.
Enclosures must adequately control moisture migration, heat transfer, air leakage and solar radiation. Experience indicates that when the requirements for the control of moisture migration have been satisfied, the other control requirements are either simultaneously satisfied, or more easily satisfied than if moisture migration is not addressed at the outset.
In practical terms, these relationships guide designers to assume flawed construction that must be compensated with redundant control measures focused on moisture management. For experienced designers these assumptions are almost axiomatic.
Physical Phenomena
Environmental conditions, both internal and external, establish the physical phenomena that impact the performance of the building enclosure. In order to be durable and provide adequate moderation of the environment, the building enclosure must be designed to provide a threshold of control over, or resistance to, these phenomena.
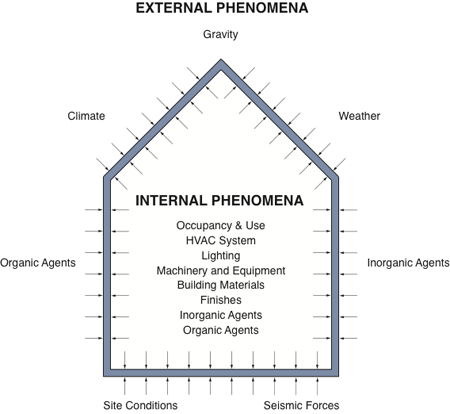
Figure 1. Imperfect building enclosures must manage all imposed internal and external environmental phenomena.
Intensity, Duration, and Frequency
All physical phenomena share intensity, duration and frequency as defining characteristics. Events such as earthquakes, tornadoes, hurricanes, and to some extent floods, are typically high intensity phenomena of short duration and low frequency. In most climate zones, vapor diffusion, heat transfer, and air leakage are normally low intensity phenomena of relatively long duration and seasonal frequency. Both types of phenomena have accounted for considerable damage to buildings, however, the strategies for dealing with each varies not only in terms of the actual control measures, but mainly according to the associated risks and consequences of failure.
Risk and Consequences
Risk of failure involves the probability of a specified level of performance proving inadequate to resist an imposed physical phenomenon or phenomena. The likelihood of failure must be reconciled with the consequences of failure in terms of safety, health, functionality, economy, and aesthetics. Minimum levels of adequacy for health and safety in buildings have been established through codes and standards, and guide the designer in these vital aspects of building performance. However, the risks and consequences of failure for a building requirement such as structural integrity are much better understood than for moisture protection. For this reason, many building enclosure design strategies are based less on probability and analytical models, and more on precedent, heuristics, and common sense. This does not suggest that analysis is completely abandoned, but instead acknowledges that the results are often only accurate to within one order of magnitude. Numerical data must be interpreted qualitatively, requiring significant experience and judgment on the part of the designer.
Durability and Redundancy
Durability is a key consideration in effective enclosure design and this requires that a level of redundancy be provided in terms of critical control functions for moisture, heat, air leakage, and solar radiation. [Resilience is a concept related to durability that applies to the design, construction, and operation of buildings and infrastructure that are resistant to natural and man-made disasters.v]
Redundancy—An enclosure with more than one 'line of defense' against imposed phenomena may be redundant with respect to one or more critical control functions. The degree of redundancy may range from: (i) resistance to each imposed phenomenon is distributed across all materials in the assembly (fully redundant); to (ii) resistance to each imposed phenomenon correspondingly addressed by individual materials within the assembly (non-redundant, hence each material represents a 'perfect barrier'). To be cost-effective and practical, redundancy is not simply doubling up on every control layer, or only selecting materials that address all of the control functions simultaneously. Control layers may be selected so as to perform more than one control function, or to significantly contribute to enhancing the performance of one or more control layers.
Multi-Functionality—A material may be uni-functional, such as a structural element, or it may address more than one required control function resisting imposed physical phenomena. Multi-functionality may be described as either: (i) single material addresses all enclosure control functions; or (ii) material primarily addresses one control function (first line of defense) and contributes to another control function(s), (second line of defense). For example, exterior insulating sheathing can act as a thermal control layer while contributing to air leakage and rain penetration control. If it is a vapor resistant material, such as extruded polystyrene, the exterior insulating sheathing can also resist vapor diffusion.
Contribution—A material may improve or enhance the performance of another material or assembly of materials without displaying multi-functionality or explicitly adding to redundancy. For example, an air barrier membrane may reduce air movement through an air-permeable insulation material, improving its thermal effectiveness but not contributing to the nominal thermal resistance of the assembly.
High-performance building enclosures provide high levels of resistance to imposed phenomena by intelligently arranging materials that are multifunctional with respect to critical control functions and contribute to the enhanced performance of one or more materials comprising the assembly.
Continuity
The continuity of critical control functions is among the most significant considerations when detailing building enclosures. Air and water leaks along with thermal bridges not only compromise performance but often lead to severe degradation of the building enclosure. In extreme cases, problems such as mold arise from a failure to maintain continuity of critical control functions. There are four Resource Pages that address building enclosure transitions to maintain continuity: Integrating the Building Enclosure; Wall to Roof Transitions; Wall to Window Transitions; and Wall to Foundation Transitions. For the purposes of enclosure design principles and strategies, it is extremely important to observe the need to achieve continuity of critical control functions, especially at transitions between enclosure assemblies.
Buildability and Economy
Lines on working drawings are straight, and the dimensions are precise, but in the field the building artifact is always an approximation, sometimes too crude an approximation to perform adequately. How does this come about?
Contractors and their trades are highly constrained by time and budget on virtually all construction projects. They are generally not inclined to spend more effort on construction than it is economically worth. If the successful (usually lowest) bidder on a construction project discovers that an assembly or detail is too expensive to execute properly, then ad hoc modifications (a.k.a. cutting corners) may be implemented by workers intent on meeting productivity quotas.
In some cases, the skill levels of the trades may be too low for the work they have been awarded. In other cases, the knowledge and experience of those performing quality assurance and supervision are simply not up to par. When none of the above factors come into play, other problems such as substandard materials or bad weather affect the quality of the finished product. Unforeseen site conditions, usually involving soils and groundwater, may compound the situation further, along with human factors such as labor disputes (strikes).
For these reasons, practical considerations in design should not be underestimated. Forgiving building systems that accept the reality of imperfect materials, workmanship, site conditions, and human factors are truly elegant and sustainable design solutions. Details whose proper execution demands the most efficient and least expensive methods are the real masterpieces of building enclosure design. This approach is certainly preferable to being 50% over budget on a project with a leaky roof, especially from the perspective of the building owner.
The economy of a building enclosure, in particular its initial capital cost, is largely determined by buildability, which also impacts its life-cycle economy if assembly of the enclosure exceeds the capability of the work force. Bad details lead to bad workmanship and ultimately poor performance.
Building Enclosure System Integration
The architectural design of building enclosures, foundations, walls, roofs, windows, and doors demands functional integration and aesthetic orchestration. Assuming that each of these assemblies and components has been individually resolved, it must be recognized that a second order of design/assessment is subsequently required. This ensures that the major assemblies and components are compatible, both mechanically at their connections and intersections, and in terms of their collective contribution towards the management of critical control functions. This iterative process from architectural concept, through physics, materials, and components, and back to the building as a system is a cornerstone of modern building science and its contribution to architectural design practice. Keeping these principles and key relationships in mind, the next section examines the critical physical phenomena that need to be considered in the design of effective building enclosures.
Climate, Exposure, Occupancy, and Building Energy Profile
Designing an effective building enclosure must properly consider the following factors:
- Climatic zone where the building is located
- Annual exposure to precipitation
- Intended use or occupancy of the building (interior climate class), and
- Building energy profile (skin-load versus internal-load dominated).
Based on these factors, it is possible to design building enclosures that adequately address all of the imposed physical phenomena while delivery high performance.
Climate Zones (Hygrothermal Region)
ASHRAE has defined 8 basic climate zones, some with variations, as listed in Table 3.

Table 3. ASHRAE climate zone definitions used for the design of hygrothermal control functions in building enclosures.
Climate zones influence the selection and arrangement of hygrothermal control layers in a building enclosure. The appropriate levels of thermal resistance may also be derived from the zone thermal criteria. Figure 2 depicts the hygrothermal climate zones of North America.
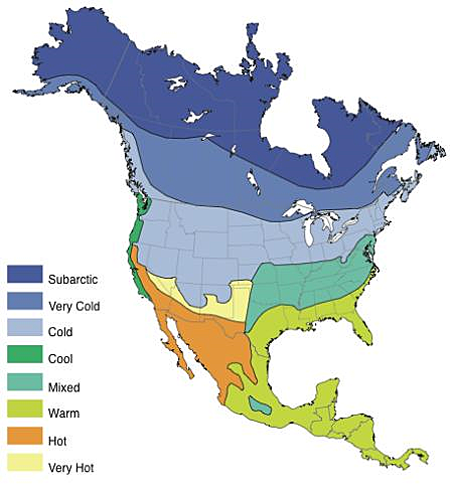
Figure 2. The selection and arrangement of heat and moisture (hygrothermal) control layers is based on climate zones. North America has all 8 climate zones and this broad range of climates explains why enclosures that are effective in one climate zone fail to perform properly in other climate zones.
Another way to understand climate zones is in terms of wetting and drying potential. All of the humid and marine climate zone variations in Table 3 have a high wetting potential and a low drying potential. This means that if the building enclosure experiences wetting due to moisture migration from either the exterior and/or interior, it will likely not dry out fully and be susceptible to mold and decay. Mixed, warm, hot, and very hot climate zones that are humid or marine will predominantly experience vapor migration across the building enclosure from the exterior toward the interior, while the cool, cold, very cold and subarctic zones will experience vapor flow from the interior to the exterior. The practical implications of these phenomena are presented in Understanding Air and Vapor Control Layers.
Precipitation Exposure
The annual quantity of precipitation is an indicator of the wetting potential of a particular geographic location, and also informs the selection of an appropriate cladding system that can adequately manage the amount of rainfall exposure.
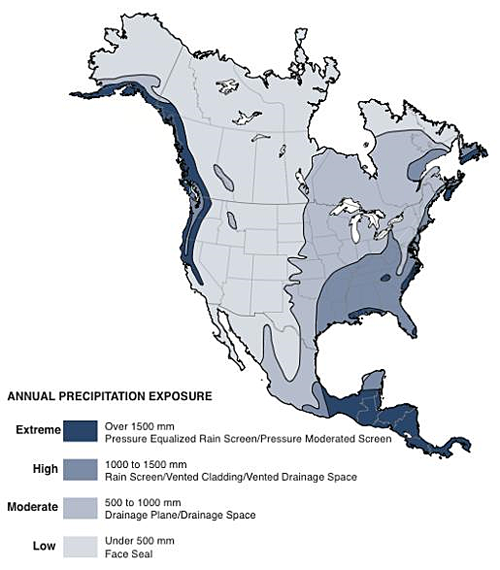
Figure 3. Annual precipitation exposure is a critical factor in the selection of a suitable cladding system that can provide adequate moisture protection.
Indoor Climate Class
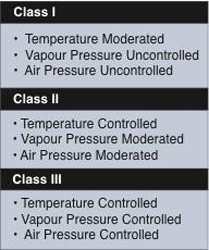
Table 4. Indoor climate classes based on a qualitative index advanced by Lstiburek 2002.vi
The building enclosure must also withstand environmental loads based on the interior building conditions. Table 4 outlines indoor climate classes based on temperature, vapor, and air pressure regimes. It should not be confused with ISO Standard 13788 characterization of indoor climate classes. Instead, it should be employed as a guide to the level of moderation or separation that must be achieved by the control layers. For example, a warehouse for storing non-perishable goods may be temperature moderated by a heating system set to prevent freezing but with no intentional means of controlling humidity or air leakage. As such, there will not be large gradients across the building enclosure and only minimal control layers will be required. On the other hand, in a facility where temperature, vapor, and air pressure must all be carefully controlled, such as a pharmaceutical laboratory, it will be essential to provide high quality control layers to provide adequate resistance across the full range of differential gradients that must be maintained within a relatively narrow tolerance.
It is important to note that the higher the climate class, the more environmental stress will be placed on the control layers. Not only do the materials comprising the control layers have to be properly specified, but their detailing to ensure continuity must also be carefully devised. In the past, building designers relied on the power of HVAC systems to manage indoor environmental conditions, but since the time of the first energy crisis in the early 1970s, there has been a steady move away from active systems of environmental control in favor of passive systems, primarily the building enclosure.
Building Energy Profile
From an energy efficiency and thermal comfort perspective, buildings are often classified according to the primary drivers for space conditioning loads. This translates into two major profiles of buildings: skin-load dominated; and internal load dominated. The design of the building enclosure must account for these characteristics to provide energy efficient operation and deliver thermal and visual comfort to the occupants.
Skin-Load Dominated Buildings
A skin-load dominated building has the largest proportion of space conditioning energy loads determined by the building enclosure. This type of building is characterized by a relatively low occupant density where internal heat generation is minimal (e.g., housing), and natural ventilation and daylighting may be easily accomplished. They are also located in a climate that is either cold or colder, or hot or hotter. Mild climates do not exert a significant temperature differential over a sufficient duration to render buildings skin-load dominated. This building type relies on high-performance windows set in a thermally efficient enclosure with minimal air leakage and thermal bridging. In general, skin-load dominated buildings benefit from passive solar heating strategies in cold climates and solar shading and natural ventilation strategies in hot climates. Typical skin-load dominated buildings include houses, apartment buildings, small commercial and institutional buildings.
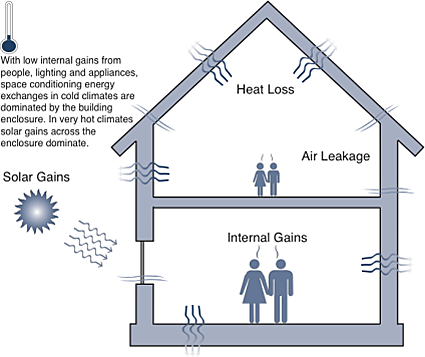
Figure 4. Skin-load dominated buildings benefit the most from high-performance building enclosures, and can take the best advantage of passive control strategies.
Internal-Load Dominated Buildings
Buildings that have high occupant densities and high internal gains from lighting and/or equipment are considered internal-load dominated buildings. Sometimes these are also referred to as a core-load dominated building. Regardless of climate type, the internal heat generation puts high demands on ventilation and cooling that are further driven by solar gains. For this building type, efficient means of rejecting excess heat generation translate into building enclosures that are typically less thermally efficient than effective at reducing solar gains by deploying shading devices and selecting appropriate optical properties of glazing. Different fenestration and shading strategies can also be deployed corresponding to the solar orientation of each face of the facade. Office towers and large retail facilities like shopping malls are notable examples of internal-load dominated buildings. Integration of the building enclosure with the HVAC systems is critical for achieving high performance in these types of buildings.

Figure 5. The energy performance of internal-load dominated buildings is strongly influenced by the window-to-wall ratio, effective U-value and solar heat gain coefficient of the glazing, and the airtightness of the building enclosure. Heat recovery for ventilation air and lighting system efficiency are the two most critical considerations for active building systems in these types of buildings.
There are also hybrid building types based on their changing occupancy. Schools are an example of buildings that are internal-load dominated when the classes are full during the day, and skin-load dominated on evenings and weekends when they are unoccupied.
It is important to appreciate that the hygrothermal design of a building enclosure to properly manage moisture, heat, and air flow is a function of the climate zone, precipitation exposure and indoor climate class. The building energy profile type is taken into consideration for the optimal levels of thermal insulation and selecting strategies for daylighting, passive solar heating, shading devices and passive cooling (natural ventilation).
Building Enclosure Design Strategies
Design strategies for building enclosures are a relatively recent opportunity for building designers. In the past, locally available materials and successful past precedents guided a highly traditional building industry where certain types of performance problems, (i.e., energy efficiency, thermal comfort, etc.), were considered acceptable. Today, a multitude of performance requirements must be satisfied amid a marketplace of innovative materials, components, and systems the designer is responsible to fully integrate, and the constructor must properly deliver. Picking a suitable generic building enclosure typology is an important first step.
Building Enclosure Typologies
The discussion that follows is focused on exterior walls recognizing that many of the considerations also apply to roofs and below-grade assemblies. It is interesting to note from Figure 6. that after thousands of years of building construction by humans, only a handful of building enclosure typologies have emerged. Most of these evolved by trial and error with some recent innovations arising from the application of building science principles, especially as it relates to rain penetration control.vii
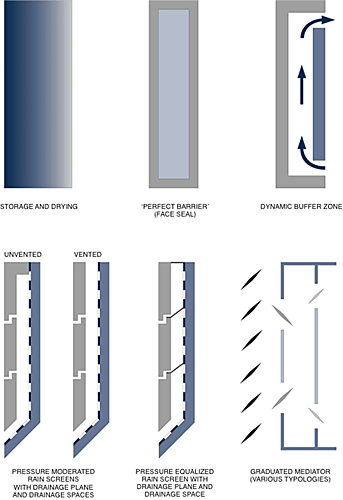
Figure 6. Schematic representations of basic building wall enclosure typologies.
Storage and Drying
Traditional masonry buildings relied on the storage and drying strategy for the management of moisture on a seasonal basis. The monolithic masonry façade was not only part of a load-bearing system, but also a hygric buffer with a capacity to store large quantities of water during wet periods, which are then released during dry periods. As long as the hygric buffer capacity was sufficient to store moisture accumulations, and the flow of moisture was not impeded at either the interior or exterior of the wall, this enclosure system would render good service. Some drawbacks of this strategy are the large quantities of materials and labor needed to erect the enclosure, the poor thermal efficiency due to a lack of insulation, and the absence of an air barrier system. Durability and moisture management are achieved at the expense of energy and thermal comfort. It is important to note that by abandoning this approach in favor of high performance, critical considerations have increased while margins of error have decreased.viii
Perfect Barrier
Modern building science experience has demonstrated that perfect barrier or "face seal" strategies for building enclosures do not have a high likelihood of acceptable performance, except for highly arid climate zones. The imperfect nature of materials and workmanship results in a high probability the perfect barrier will have discontinuities, either at the time of construction / assembly and/or after exposure to the elements. Maintaining a perfect barrier is a costly and perpetual proposition. Perfect barrier or face seal systems do not have any redundancy of critical control functions, have no provisions for draining unintentional water penetration, and should therefore be avoided in high-performance building design. Perfect barriers or face seal systems rely on tightly sealed joints using caulking and/or gaskets to resist water and air leakage. This approach has been applied to components such as windows and doors that are manufactured under controlled conditions in factories. The joint between the component (window) and the opening in the enclosure is also highly dependent on workmanship and material durability.
Dynamic Buffer Zone
The dynamic buffer zone is a strategy employed in the preservation of historic buildings where the exterior facade cannot be altered, but typically cooling is being provided through a modernized HVAC system. This is exclusively an enclosure retrofit strategy intended to create a buffer zone inboard of the existing facade, which continues to reside in its original hygrothermal environment.
Graduated Mediators
The most notable contemporary example of a graduated mediator is the double-skin facade (DSF), but there are many historical precedents where a system of overhangs, screens, and louvers manipulated insulation, shading, and natural ventilation to enhance environmental control. This strategy is usually associated with mild climates where the potential passive contribution of the enclosure is significant. In more extreme climates, a single enclosure assembly is generally preferred as this enables multiple lines of defense (in effect a compressed graduated mediator) to be incorporated cost-effectively into a more conventional building enclosure.
Pressure Moderated Drainscreens
This term refers to a family of enclosure typologies that deploy a cladding that has a vertical airspace behind it that is drained to the exterior. A drainage plane, usually in the form of a sheathing paper, prevents bulk water from penetrating past the air space. Pressure moderated drainscreens, also known as cavity walls in masonry construction, may be vented or unvented, with the latter approach being recommended for water absorptive cladding materials such as wood and brick. The fundamental principle behind this strategy is to make it much easier for the water to get out than to get in the assembly. Moisture management for this type of enclosure relies on the 3-Ds: deflection, drainage, and drying. This strategy can be deployed in a wide variety of enclosure types including, wood/metal/vinyl siding, brick/masonry, precast concrete, and EIFSix. Typically, this enclosure strategy is suitable for low and mid-rise buildings. For high-rise buildings, a pressure-equalized rain screen strategy is recommended.
Pressure-Equalized Rain Screens
Pressure equalized rain screens are an invention of modern building science. Drained cavities that proved effective in low-rise buildings evidenced air and water leakage on high-rise buildings due to extreme wind speeds. The concept behind pressure equalized rain screens is to create air pressure chambers behind the cladding by compartmentalizing the air space with baffles. Wind pressures would be neutralized in these pressure equalization compartments, thus eliminating a driving force for rain penetration. Considerable research has shown this approach to be effective even when it is not perfectly achieved in practice.x
Pressure equalized rain screen principles can be applied to a wide variety of cladding system including curtain walls. Best practices for the design and detailing of pressure-equalized rain screens have been developed to assist designers.ix
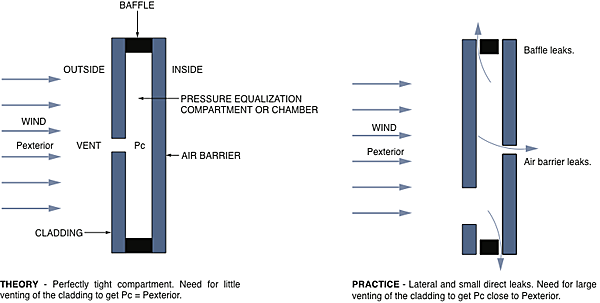
Figure 7. Pressure equalized rain screens are idealized drainscreens that manage air pressure differences through compartmentalization of the air space behind the cladding. In reality, the pressure equalization is not perfectly achieved, but rain penetration can still be adequately controlled with this strategy as long as a continuous, structural air barrier is provided.
Drainscreens, Rain Screens and Enclosure Fundamentals
There remains a great deal of confusion about drained enclosure assemblies, due in part by the nomenclature that has been used: cavity wall, rain screen, drainscreen, pressure-equalized, pressure-modulated, pressure-moderated, and rear ventilated are just some of the terms that may be found in publications. It is helpful to shed light on this fuzzy situation.
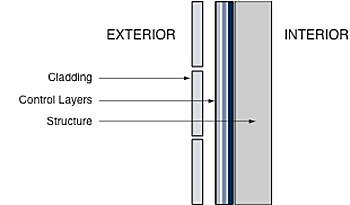
Figure 8. Enclosure assemblies that conform to building science principles of performance consist of three primary elements from inside out: the structure; control layers (heat, air, moisture, solar); and the cladding.
If it is generally acknowledged that the mass wall and the perfect barrier approach do not constitute feasible alternatives for high-performance buildings, then the only enclosures worth considering provide drainage and some degree of air pressure moderation. While the graduated mediator may be engineered to deliver a high level of control it is not off-the-shelf technology readily available in most building markets. The pressure moderated drainscreen, in a variety of forms and proprietary systems, is suitable for low to mid-rise buildings, and the pressure equalized rain screen is well suited to high-rise buildings. Regardless of the approach selected, building scientist Joseph Lstiburek has demonstrated it must conform to the schematic arrangement of enclosure elements depicted in Figure 8.xii
Important Note: The ordering of cladding, control layers, and structure do not change regardless of climate type. Cladding and control layers always reside outboard of the structure, which is held at a relatively constant temperature to minimize thermal stresses, and thereby maintain dimensional stability.
Lstiburek has demonstrated this arrangement is equally applicable to roofs and floor slabs, suggesting there are not nearly as many feasible enclosure typologies as might be portrayed by the wide variety of building materials, components, and assemblies available in the construction marketplace. The corollary to this observation is that only a subset of available building enclosure technologies is suitable to a particular combination of climate, exposure, indoor climate class, and building energy profile. Contrary to popular misconceptions, there are only a handful of successful building enclosure design strategies with proven past performance available to designers. xiii It is therefore advisable to ensure the proposed design solution conforms with a feasible generic building enclosure strategy that observes these fundamental building science principles.
Additional Resources
Publications
- Building Envelope by Canada Mortgage and Housing Corporation.
- Building Science for a Cold Climate by N.B. Hutcheon and G.P. Handegord. Institute for Research in Construction, 1983.
- Building Science for Building Enclosures by John Straube and Eric Burnett. Building Science Press, December 2005.
- Designing the Exterior Wall: An Architectural Guide to the Vertical Envelope by Linda Brock. John Wiley and Sons Inc., 2005.
- Evolution of Wall Design for Controlling Rain Penetration by G.A. Chown, W.C. Brown, and G.F. Poirier. Construction Technology Update No. 9, December 1997.
References
i. BSI-024: Vocabulary by Lstiburek, Joseph. Building Science Insight #024, September 9, 2009.
ii. BSD-007: Historical Development of the Building Enclosure by Straube, John. Building Science Digest #007, October 24, 2006.
iii. CBD-48: Requirements for Exterior Walls by Hutcheon, N.B. Canadian Building Digest #48, December 1963.
iv. Water and Building Materials by Latta, J.K. Canadian Building Digest #30, National Research Council Canada, June 1962.
v. Secure / Safe. WBDG Secure / Safe Committee.
vi. Moisture Control For Buildings by Lstiburek, Joseph, 2002. ASHRAE Journal, February 2002, pp. 36-41.
vii. Rain Penetration and Its Control by Garden, G.K. CBD-40. April 1963.
viii. BSI-039: Five Things by Lstiburek, Joseph. Building Science Insight #039, April 20, 2010.
ix. BSI-038: Mind the Gap, Eh! By Lstiburek, Joseph. Building Science Insight #38, February 22, 2010.
x. Facts and Fictions of Rain-Screen Walls by Rousseau, M.Z. Construction Practice: Selected Applications in Construction Technology, NRCC 35475, 1993.
xi. The Rain Screen Wall System by Canada Mortgage and Housing Corporation, Ottawa.
xii. BSI-001: The Perfect Wall by Lstiburek, Joseph. Building Insight #001, May 20, 2008.
xiii. BSD-018: The Building Enclosure by Straube, John. Building Science Digest #018, August 1, 2006.