Introduction
Within This Page
The management of moisture migration is by far the most important control function to be addressed by the building enclosure designer. Moisture related problems in buildings are common and broadly vary in types and consequences. A brief listing of moisture related problems illustrates this point: frost heaving, adfreezing, water leakage, wood rot, mold growth, spalling, efflorescence, corrosion, and degradation and staining of finishes. Consequences range from structural failure to cosmetic flaws, and in some cases the health of the occupants can be adversely affected, as in the case of mold growth, causing allergic and respiratory problems. This resource page explores moisture management in building enclosures and focuses on the concepts and terminology related to moisture management in building enclosures to provide a basis for better understanding of the various moisture management strategies that can be deployed in enclosure design. These strategies are based on what is commonly referred to as the 4 Ds:
- deflection of water to minimize wetting exposure;
- drainage to convey away water that penetrates the assembly;
- drying of any residual water by means of ventilation; and
- durability of materials to withstand exposure to periodic wetting and provide an acceptable service life.
"Except for structural errors, about 90 percent of all building construction problems are associated with water in some way." 1
The list of the harmful effects of water in building materials and assemblies is indeed a long one. In many instances the water by itself is not harmful, and only when combined with other phenomena does it cause rapid deterioration. On the other hand, the other phenomena involved will not cause deterioration in the absence of water. It follows then that if water can be controlled a building can be made more durable and the maintenance and repair costs reduced. If this could be achieved only by the use of very expensive materials and construction it could be argued that it is better to let the building deteriorate and to replace the damaged portion from time to time. In fact, however, durable construction can be achieved with relatively inexpensive materials and designs, provided that the designer understands the behavior of water in its various forms and applies the necessary controls to prevent it from accumulating in harmful quantities.2
Description
Physical States of Water
Water, or H2O, is found everywhere on our planet. For this reason, building designers must be able to apply moisture management strategies in building enclosures that correspond to the physical states of water. Like any pure substance, water may exist in three states: solid (ice), liquid (bulk or free water), and gas (vapor). In addition, various building materials may capture water molecules from the surrounding air and collect them on the surfaces of their inner pore structures in what is known as an adsorbed state. The predominant states of water that are of interest to building scientists and designers are bulk water and water vapor, although in cold climates ice may pose particular challenges.
Solid - Ice
Water freezes at 32°F (0°C) and goes from being a liquid to a solid. When water freezes, it increases in volume by about 9%. The ice then shrinks as the temperature decreases. The shrinkage is marginal, about 0.4% in volume going from 30&*deg;F (-1°C) to -50°F (-46°C). From a building performance perspective, ice is an important consideration in foundation design, where footings must be located below the depth of frost penetration to avoid heaving, and for freeze/thaw cycles in materials to ensure durability. Interestingly, if water in its bulk and vapor states is properly managed, most issues related to ice may be easily resolved.
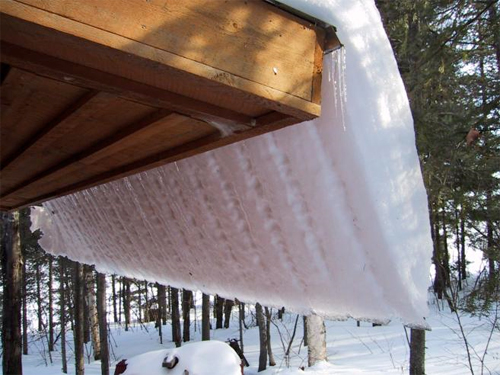
Figure 1. Ice buildup on roofs can cause damage to roofing and pose a hazard to pedestrians below. Enclosure design cannot control weather events like freezing rain, but the selection of appropriate building materials and details can minimize the potential for ice damage and risk of hazards. Often, observation of local practices will provide a good indication of suitable ice management strategies that are proven to be effective in a particular locale. Source: T. Kesik
Liquid - Water
Between 32°F (0°C), water's freezing point, and 212°F (100°C), its boiling point, water remains in a liquid state and to a lesser degree is suspended in the surrounding air as vapor (see next topic). Bulk water is experienced by buildings as precipitation (rainfall), snowmelt, flooding, groundwater, and the condensation of water vapor. Water as a liquid must be managed because many building materials are susceptible to various forms of damage by repeated or chronic wetting and little or no drying. Traditional building technology evolved in response to the management of bulk water with special attention to material selection and arrangement. Architectural features, such as sloped roofs and overhangs, were deliberate strategies aimed at managing liquid moisture. At the detail level, flashings and drip edges were employed to shed water away from the building enclosure. Most moisture management strategies begin by carefully considering appropriate control measures for the many sources of liquid water.
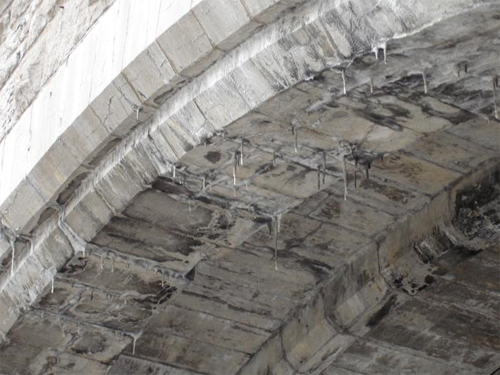
Figure 2. Water penetration into a stone archway causes water to leach through the material leading to mineral deposits and unsightly discoloration. Blemishing will eventually lead to deterioration as freeze/thaw cycling occurs. Source: T. Kesik
Gas - Water Vapor
The air contains suspended water molecules in the form of vapor, resulting from the evaporation or boiling of water, and the sublimation of ice. At a given temperature in the atmosphere, the air is capable of holding a given quantity of water vapor. Relative humidity (RH) is a measure of the amount of water vapor in an air-vapor mixture at a given temperature in the atmosphere, relative to its saturation point (100% RH). The vapor in the air exerts a vapor pressure and this is the driving force for the diffusion of water vapor through materials. Water vapor can also be transported by air leakage (i.e., the movement of a volume of air into or out of the building enclosure), a mechanism that is capable of transporting much more water than vapor diffusion.
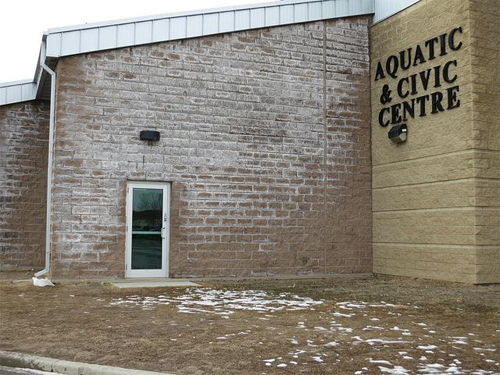
Figure 3. Efflorescence is caused by the migration of water vapor into mortar and masonry where it develops capillary water flow at high relative humidity. Salts in the mortar are dissolved and transported to the surface of the masonry, and the salt crystals remain after the water has evaporated. Besides being unsightly, efflorescence can lead to the deterioration of masonry finishes. Source: Martin Eisbrenner
Moisture Migration Phenomena
The relationships between the phases of water, sources, processes, storage, and sinks are depicted in Figure 4. Buildings are placed within this water environment and must effectively manage these interactions. Designers must devise moisture management strategies specific to each phenomenon and ideally conceive economical building enclosures that have sufficient redundancy to provide a factor of safety against moisture loads, similar to the approach taken for structures.
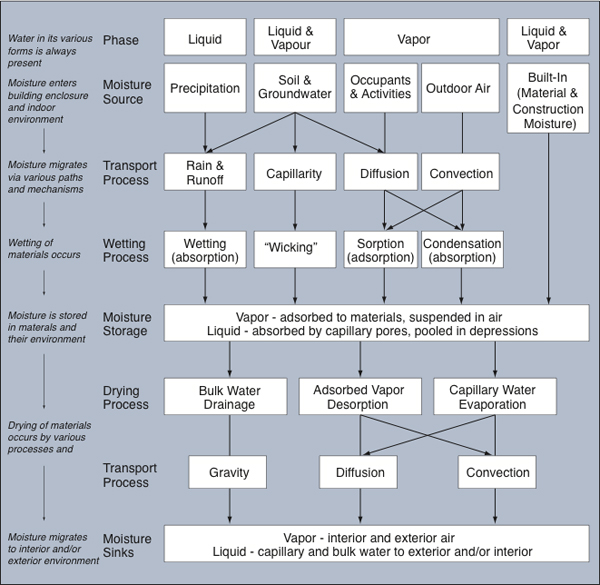
Figure 4. Moisture sources, processes, storage and sinks - the moisture management design challenge is to consider these explicitly and ensure all critical factors have been addressed. Source: Moisture in Buildings by John Straube. ASHRAE Journal, January 2002, pp. 15-19.
Moisture and Material Interactions
From a building science perspective, moisture and material interactions are often governed by the nature of the materials. A practical classification is between hygroscopic (hydrophilic) and hydrophobic materials. Hygroscopic (hydrophilic) materials absorb water and most traditional building materials, such as wood, concrete, brick, and plaster are hygroscopic. Hydrophobic materials repel water and examples include glass, metals, and plastics. There are new materials exhibiting hybrid behavior, such as water resistive barriers that may resist bulk water but freely allow vapor diffusion.
Another significant factor influencing moisture and material interactions is capillarity. A capillary is a narrow, tube-like space or void in a material or assembly that can draw up water by a combination of surface tension and adhesive forces. As a result, a tool like a paint brush with hydrophobic bristles can draw up and retain paint by interstitial capillarity. Materials like wood or concrete used in a foundation assembly behave this way if built into wet soil. Capillarity in building materials explains the hysteresis in their moisture contents, and reinforces the need to prevent these materials from excessive wetting (see Figure 5).
For the building enclosure designer, the process begins with the selection of a suitable moisture management strategy for the enclosure assembly (i.e., wall, roof, etc.). Then, the water absorbing and repelling properties of constituent materials, and their capillarity, must be considered to determine if these are compatible. As a first step, the material should not be placed in an environment that will cause its degradation. If the designer cannot arrange materials to create a conducive environment, alternative materials must be employed, or a different moisture management strategy selected.
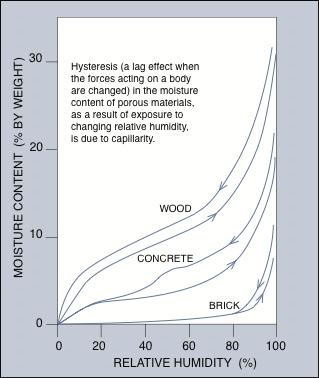
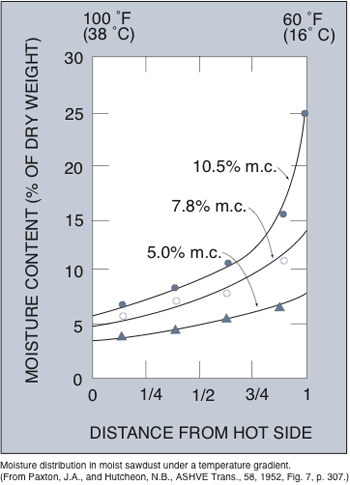
Figure 5. Common building materials having capillaries take much longer to dry out than to get wet. Source: Building Science for a Cold Climate by Neil Hutcheon and Gus Handegord. Institute for Research in Construction, 1983.
Figure 6. The concentration of moisture on the cold side of an assembly increases with the initial moisture content of the materials in the cavity. In practical terms, this means that only very low levels of moisture accumulation may be tolerated in most assemblies. Beyond this threshold, the moisture content on the cold side of moisture susceptible materials, such as wood-based sheathings, will begin to approach their fiber saturation point, often causing rot under chronic wetting. Low air and vapor permeable insulation materials, like medium density polyurethane spray foam, represent a popular moisture management strategy because they control heat, air, and moisture flows.
Moisture Flow and Temperature Gradients
The increasing emphasis on energy efficiency in building enclosures often results in wall and roof cavities that are highly insulated with air and vapor permeable insulation materials. This produces strong temperature gradients across the wall cavities, and experimental research as depicted in Figure 6 has shown that any moisture in the cavity will migrate toward the cold side of the assembly, driven largely by vapor pressure differences.
There are three primary means of addressing this phenomenon:
- avoid using air and vapor permeable insulation in cavities;
- use continuous insulation outboard of enclosure cavities insulated with air and vapor permeable insulation, to reduce the severity of the temperature gradient in the cavity; and
- leave cavities uninsulated and place continuous thermal insulation outboard of the cavity.
Continuous exterior insulation is always the most effective strategy, but cost, construction issues and/or existing conditions may require the first two strategies. Selecting a suitable strategy is largely determined by the climate zone, precipitation exposure and indoor environmental conditions for the particular building enclosure under consideration. (See Climate, Exposure, Occupancy, and Building Energy Profile for more information.)
Hygric Buffer
The concept of hygric buffer involves the capacity for safe storage of moisture in materials. Safe storage of moisture also depends on the duration of exposure to moisture (time of wetting) and the nature of the material, specifically its susceptibility to damage by moisture (e.g., concrete versus wood). As the sustainability imperative drives designers to use less materials with lower embodied energy, this generally translates into building enclosure assembles with significantly lower hygric buffer capacity than traditional methods and materials.
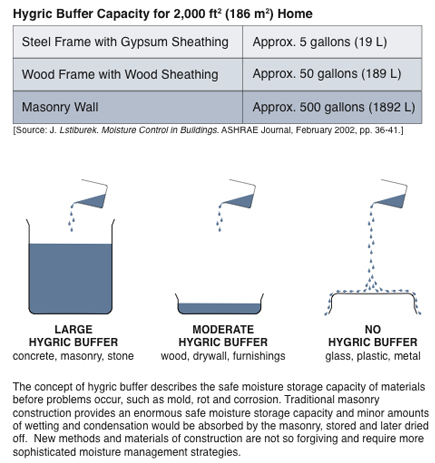
Figure 7. In practical terms, the hygric buffer capacity of building enclosure assemblies largely determines the level of redundancy that needs to be provided by critical control layers addressing moisture management functions.
Storage and Drying
Traditional materials and methods of construction often relied on storage and drying as moisture management strategies. While the durability provided by these strategies is unquestionable, the operating energy costs are no longer affordable. In contemporary building enclosure design, storage and drying concepts still apply to cladding materials, especially wood. However, instead of relying on heat loss through the enclosure for drying, effective drainage and adequate ventilation must be carefully considered.
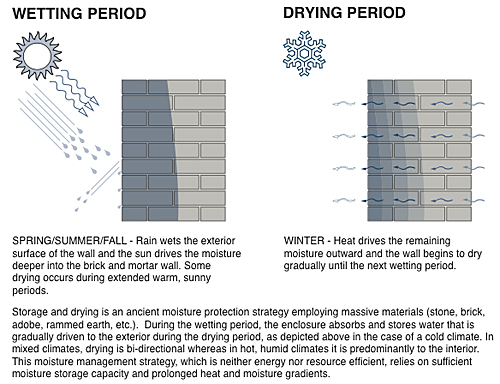
Figure 8. Improvements to the energy efficiency of building enclosures have reduced the driving force behind the seasonal drying of assembly materials. In the past, durability of cold climate enclosures was achieved by expending space heating energy at a time when fuel sources were very inexpensive. Current and forecast labor, material and energy costs require building enclosures to achieve higher performance with lesser expenditure.
Vapor Diffusion Versus Air Leakage
To appreciate the difference in the magnitude of diffusion versus air leakage as moisture transport mechanisms, consider a helium filled balloon, the kind found at parties and celebrations. When these are left to sit for several days they often no longer float because the helium has diffused through the balloon's membrane. By comparison, pricking the balloon will cause the leakage of the helium and in a matter of a few seconds it is no longer inflated. Building science research has indicated water transport by air leakage may be several orders of magnitude greater than by vapor diffusion. For example, under typical cold climate indoor/outdoor conditions, it is estimated that about 1/3 quart of water will migrate by diffusion over an entire heating season across a 4 x 8 foot sheet of gypsum board without a vapor retarder. A 1 square inch hole in the same sheet of gypsum board will result in about 30 quarts of water being transported by air leakage - a factor of roughly 100 to 1 for air leakage versus diffusion.3
The practical implications of the difference in magnitude between these two water vapor transport mechanisms are significant. While adequate vapor diffusion control may be easily provided by coatings such as paint over the interior surface of exterior wall enclosures, the control of air leakage requires careful attention to material selection, detailing, and sequence of installation.
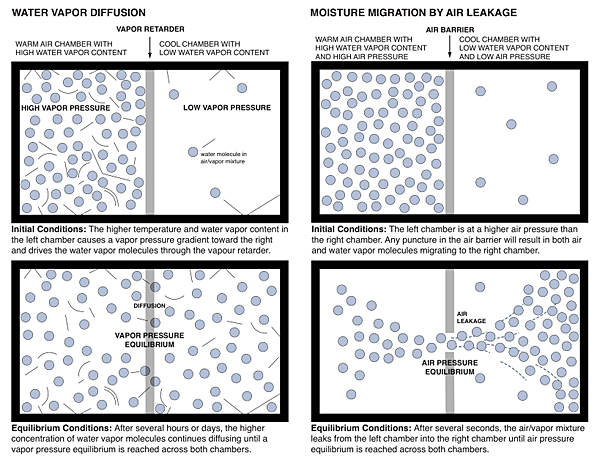
Figure 9. Vapor diffusion is a random and relatively slow moisture transport mechanism compared with air leakage, however, both need to be addressed when designing enclosures.
Condensing Surface of Interest
Moisture penetration and/or accumulation within enclosure assemblies is practically unavoidable and must therefore be managed within the moisture exposure and safe storage thresholds of the constituent materials. Assuming that defects (water leaks) may be reasonably eliminated or suitable repaired, the seasonal migration of moisture by diffusion and/or air leakage becomes the most significant concern. The migration of moisture across insulated building enclosure assemblies is of great interest to building science because it predicts the long-term durability of the enclosure and its susceptibility to problems such as staining or mold growth. Typically, if there is potential for a performance problem, moisture migration due to diffusion and/or air leakage will accumulate at some point in the enclosure assembly. This location is termed the condensing surface of interest. Figure 10 depicts two condensing surfaces of interest in an insulated, wood-frame wall assembly corresponding to two different seasonal conditions.
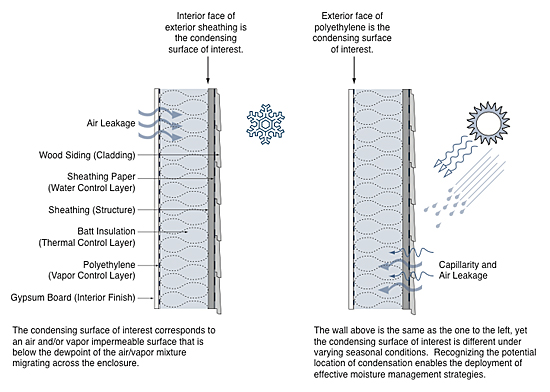
Figure 10. The condensing surface of interest in an enclosure assembly often changes on a seasonal basis. In climate zones where only one form of space conditioning is dominant (i.e., heating or cooling) there may only be a single condensing surface of interest. Hygrothermal analysis is capable of identifying critical surfaces to inform the appropriate selection and arrangement of materials.
Identification of the condensing surface of interest is usually straightforward. It occurs on the upstream face of a surface or plane of low air and/or vapor permeability that is at or below the dew point temperature of the migrating air/vapor mixture. Once the condensing surface of interest is located, suitable measures can be taken to manage the potential for moisture accumulation and related problems.
Wetting and Drying Potential
Most materials can withstand some degree of wetting provided they are subsequently allowed to dry. Some materials can endure numerous wetting/drying cycles with no significant deterioration. But there are also materials that are highly sensitive to the magnitude and duration of wetting.
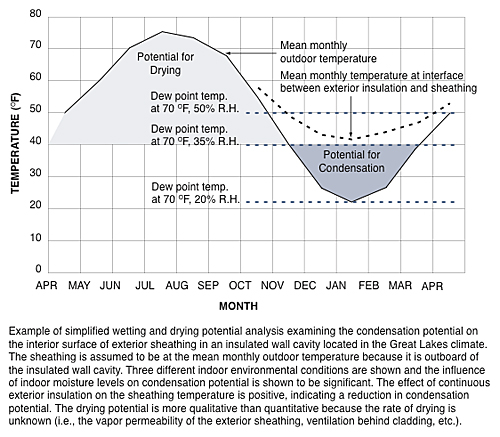
Figure 11. Wetting and drying potential is the primary phenomenon underlying the limit states design of moisture management in building enclosures. Research into limit states (beyond safe storage capacity) of building enclosure assemblies and materials has not yet established reliable thresholds to guide designers. In the future, design standards for moisture management may become as systematic and rigorous as those governing structural engineering.
Moisture Balance
Managing the moisture balance in building enclosures is a major challenge of modern building science. Different materials can cope with various amounts of moisture and duration of exposure to wetting. In assemblies, the upper moisture exposure threshold is determined by the least moisture tolerant material. In formulating suitable moisture management strategies, the essential conditions for moisture problems must be kept in mind.
For a moisture-related problem to occur, at least five conditions must be satisfied:
- a moisture source must be available;
- there must be a route or means for this moisture to travel;
- there must be some driving force to cause moisture movement;
- the material(s) involved must be susceptible to moisture damage; and
- the moisture content must exceed the material's safe moisture content for a sufficient length of time.
To avoid a moisture problem one could, in theory, choose to eliminate any one of the conditions listed above. In reality, it is practically impossible to remove all moisture sources, to build walls with no imperfections, or to remove all forces driving moisture movement. It is also not economical to use only those materials that are not susceptible to moisture damage. Therefore, in practice, it is common to address two or more of these prerequisites so as to reduce the probability of exceeding the safe moisture content and the amount of time the moisture content is exceeded.4
Moisture balance is not a uniform or homogeneous phenomenon in real buildings. Often there is a weak link in the chain, figuratively speaking, and some part of an enclosure assembly with critical exposure and/or at a complex transition will have its safe moisture storage capacity exceeded for a sufficient period of time to cause deterioration, and in extreme cases, failure to adequately provide critical control functions. In this sense, moisture balance is influenced both by the selection and arrangement of materials, and the detailing of the enclosure assemblies and their transitions.
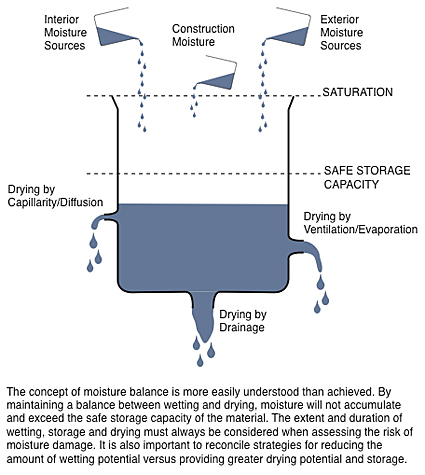
Figure 12. Calculating the moisture balance for materials comprising an enclosure assembly (wall, roof, etc.) is not a precise science because materials and workmanship are imperfect, and exposure to weather is difficult to predict. In the absence of a limit-states design approach to moisture management engineering, providing multiple lines of defense, while ensuring it is easier for water to drain out of the assembly than to penetrate it, represent prudent design practice.
Moisture Management Synopsis
The fundamental premises underlying moisture management in building enclosures assume that materials and workmanship are imperfect, construction moisture is unavoidable and the most practical strategy involves redundancy of critical control measures. The intelligent arrangement of multi-functional materials that manage moisture in its various states while also contributing to the control of heat flow and air leakage is a proven means of providing redundancy cost-effectively. It is also important for designers to recognize that imperfections, deterioration, and aging in building enclosures will inevitably lead to moisture penetration, and these inevitable events must be managed through the selection, arrangement and detailing of enclosure assemblies and their transitions.
Additional Resources
Publications
- Appraisal and Repair of Claddings and Fixings, (Appraisal and Repair of Building Structures Series) by Wilson, M. and P. Harrison. American Society of Civil Engineers, February 1993.
- Case Studies of Moisture Problems in Buildings by Proskiw, G. Thermal Performance of the Exterior Envelopes of Whole Buildings X International Conference, Clearwater Beach, Florida, December 2-7, 2007.
- The Difference Between a Vapor Barrier and an Air Barrier by Quirouette, R.L. Building Practice Note No. 54, Division of Building Research, National Research Council Canada, July 1985.
- Investigating and Diagnosing Moisture Problems by Lstiburek, Joseph. Building Science Digest #108, Building Science Corporation, October 27, 2006.
- Moisture and Materials by Straube, John. Building Science Digest #138, Building Science Corporation, October 24, 2006.
- Moisture Control for Buildings by Lstiburek, Joseph. ASHRAE Journal, February 2002, pp. 36-41.
- Moisture Control in Buildings: The Key Factor in Mold Prevention, ASTM MNL18-2nd, October 2009.
- Moisture in Buildings by Straube, John. ASHRAE Journal, January 2002, pp. 15-19.
- Appendix C of the Building Air Quality Guide: Moisture, Mold and Mildew., EPA.
- Performance and Durability of the Window-Wall Interface, STP 1484, ASTM International, 2006.
- The Technology of Building Defects by Hinks, John and Geoff Cook. E&FN Spon, 1997.
- Up Against the Wall: An Examination of Building Envelope Interface, STP 1509, ASTM International, 2010.
Footnotes
1 [ASTM E 241-77, Recommended Practices for Increasing Durability of Building Constructions Against Water-Induced Damage. Philadephia, PA: American Society for Testing and Materials, 1977.]
3 [Lstiburek, J. Insulations, Sheathings and Vapor Retarders . Research Report - 0412, Building Science Corporation, November 2004.]
4 [Straube, John and Eric Burnett. Building Science for Building Enclosures. Building Science Press, Westford, MA, 2005.]