Introduction
Within This Page
Architecture has always been the marriage of aesthetics, function, economics, and building science. Every successful project ever constructed has balanced these often conflicting requirements.
Nonresidential projects are a financial exercise from beginning to end—projected revenue streams must cover construction and operating expenses, limiting the initial and life-cycle costs a project can bear. Function and aesthetics create building value-in-use. And if design is not supported with adequate building science, unexpected cost overruns and/or premature building failure are likely outcomes.
These interdependent considerations make architecture a uniquely challenging profession. The demands of sustainable construction add a further dimension of complexity.
Sustainability Drives Change in Design and Construction Practices
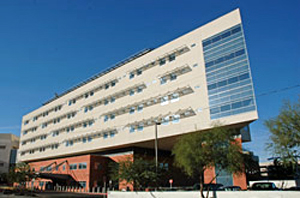
Sustainability add a new dimension to architecture and construction.
With the advent of LEED 2009 and state building codes steadily evolving toward more stringent requirements for energy-efficient building performance, significant changes in building envelope design are happening at a rapid rate. Continuous exterior insulation is required in many cases to meet building enclosure thermal performance requirements. Air barriers have become a code-mandated part of building enclosure design. In addition, the need to deliver real energy benefits once buildings are in operation is driving new building compliance and commissioning practices.
This raises the bar for everyone in the construction industry, not just architects.
To reliably reduce long-term building energy consumption, construction practices are changing. Lowest initial-cost bid processes now must anticipate the requirements of ever-tightening regulations and associated building performance verification procedures.
One tool that can be used is integrated project delivery. Early design phase collaboration among larger, more diverse design teams helps architects deliver projects that are both sustainable and cost-effective.
Architects will need all the collaboration they can get. Trying to attain sustainability objectives through product selection is not likely to answer the complex tradeoffs inherent in architecture. Taking a holistic viewpoint enables designers to create systems-based strategies, where key components of the building are evaluated on their contributions to multiple design objectives. That way, aesthetic, functional, economic, building science and sustainability goals can be effectively reconciled to meet the emerging demands of 21st century architecture.
EIFS and the Initial-cost Paradigm
Exterior Insulation and Finish Systems (EIFS) are cladding assemblies that can be configured in many ways to meet a range of end-use needs. Most of the EIFS used in the United States have been configured to meet demand for outstanding visual appeal at low initial cost. This has influenced general perceptions of the properties that EIFS are able to provide.
EIFS have performed very well in cost sensitive environments, as demonstrated by the large number of outstanding projects completed with EIFS claddings. Many of these buildings have performed well for 30 years or longer.
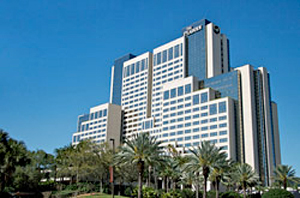
First opened in 1986, the EIFS-clad Peabody hotel in Orlando, FL retains its distinctive appearance.
With the advent of more rigorous building codes, EIFS can be configured to provide higher performance. Provision can be made for water drainage; insulation values can be substantially increased; an air barrier can be added; and impact resistance dramatically improved, all for very little extra cost. Compare these High-Performance EIFS with traditional materials like brick, stone and metal composite, and EIFS can substantially reduce initial cost in addition to providing outstanding performance and aesthetics.
Controlling initial cost in addition to life-cycle cost is an important aspect of sustainable construction, because the pillars of architecture (aesthetics, function, economics, building science and now sustainability) will never change. This is particularly true for designers who intend to pursue certification under the more challenging LEED 2009 standard.
Description
EIFS Design for Sustainability
The U.S. Green Building Council's (USGBC) Leadership in Energy and Environmental Design (LEED) rating system provides a comprehensive approach to sustainability. It sets performance objectives for design professionals, and provides them with latitude to attain environmental goals in creative ways that take the needs of various stakeholders into account. As a result, materials per se provide very limited LEED credit contributions. Performance counts—and designers that leverage the benefits of the materials they choose and maximize all dimensions of performance will be the most successful.
That is why a detailed understanding of the properties of High-Performance EIFS, and the ways that EIFS-related design decisions contribute to overall project objectives, is so important.
EIFS Design for LEED-rated Buildings
LEED has seven sections—Sustainable Sites (SS), Water Efficiency (WE), Energy & Atmosphere (EA), Materials & Resources (MR), Indoor Environmental Quality (EQ), Innovation & Design (ID) and and Regional Priority (RP).
The Material and Resources section deals with materials directly, but in the case of EIFS it is of secondary importance. That is because the greatest contributions EIFS can provide come from the combination of thermal performance, exterior appearance, weight reduction, and cost-effectiveness unique to these products. EIFS contribute toward multiple design objectives, helping architects create buildings that satisfy their many constituencies, including those related to LEED.
LEED-NC Energy and Atmosphere (EA) Prerequisite 2
This is where EIFS can make their most significant contributions to designs targeting LEED 2009 ratings. All new LEED-rated buildings must demonstrate an improvement in energy performance at least 10% beyond the requirements of ASHRAE 90.1. Further improvement qualifies for up to 19 points under Energy and Atmosphere (EA) Credit 1.
When designing for energy efficiency, the building envelope is the place to start. Creating a tight, highly insulating building envelope is the most cost-effective way to minimize energy consumption. Reduction in base heating/cooling demand may allow HVAC systems to be downsized, reducing initial cost and improving energy efficiency. For designers contemplating the use of alternate energy strategies such as building-integrated photovoltaics, an efficient building envelope is needed to ensure that these expensive resources are effectively utilized.
To maximize the benefits of High-Performance EIFS, it is important to understand how LEED evaluates the energy efficiency of a structure that has yet to be constructed. LEED provides both prescriptive compliance and thermal modeling options.
Prescriptive compliance paths developed by ASHRAE and the New Buildings Institute each provide a set of design requirements. All requirements must be fulfilled to meet EA Prerequisite 2 and attain a specific number of EA Credit 1 points. Thermal modeling is an alternate approach that uses computer software to simulate building energy performance. Projects that target more than 3 EA Credit 1 points must use thermal modeling.
LEED EA Prerequisite 2: Prescriptive Compliance Options
ASHRAE has developed a series of Advanced Energy Design Guides focused on Small Offices, Small Retail Buildings, Small Healthcare, Warehouses and K-12 Schools. These Guides contain prescriptive compliance paths that can be used to meet EA Prerequisite 2 and provide 1 point under EA Credit 1.
The New Building Institute's Advanced Buildings Core Performance Guide provides prescriptive options for larger buildings (up to 100,000 ft², excluding health care facilities, warehouses and laboratories). Meeting Core Performance Guide requirements can provide 1-3 points under EA Credit 1.
Three aspects of the ASHRAE and Core Performance Guide prescriptive compliance paths are relevant to EIFS. First, all Guides require use of an air barrier. Second, the Guides require minimum levels of insulation for exterior walls specific to each climate zone and wall type. While the Guides describe specific combinations of cavity insulation and continuous exterior insulation, they also define maximum wall assembly U-factors that can be used to qualify alternate insulation designs. Third, in many cases the insulation requirements of these Guides can only be met by using continuous insulation, typically placed on the exterior of wall sheathing. Continuous insulation is needed to prevent thermal bridging, which can reduce effective R-values by up to 65% in light-gauge steel-frame assemblies.
The five ASHRAE Guides, The Core Performance Guide and the ASHRAE 90.1 standard all contain slightly different insulation requirements. These levels are steadily increasing as the Guides are revised to provide building performance consistent with the more stringent requirements of LEED 2009 and society's demand for energy efficiency.
Cavity insulation combined with continuous exterior insulation introduces a number of new factors to wall design. Location of the dew point within the wall changes with insulation placement and amount. Excessive amounts of cavity insulation can move the dew point inside the wall cavity, creating potential for condensation and associated moisture-related issues. Use of continuous exterior insulation can make brick, stucco, and other wall claddings thicker, changing building aesthetics and requiring careful evaluation of techniques used to fasten the claddings to the building structure. Fire propagation properties may also be affected.
While continuous exterior insulation places new demands on traditional claddings, it is a tested, proven, inherent part of High Performance EIFS.
Recently, the Department of Energy's Oak Ridge National Laboratory completed a 30-month evaluation of the hygrothermal performance of EIFS, stucco, and brick walls. The wall system found to have the best overall performance—an EIFS with 4" of EPS insulation and an air barrier—meets or exceeds all ASHRAE and Core Performance Guide insulation and air barrier requirements in the continental U.S. and much of Alaska.
In addition to reliably providing continuous exterior insulation, High Performance EIFS can be designed to incorporate a fluid-applied air barrier material. Many EIF systems offer fluid-applied air barrier systems that are approved for use behind all claddings, allowing designers to create a seamless air barrier for all walls on multi-clad buildings.
LEED EA Prerequisite 2: Thermal Modeling Option
Thermal modeling must be used for buildings larger than 100,000 square feet, for certain types of buildings, and whenever more than 3 points under EA Credit 1 is needed.
Thermal modeling software predicts the energy consumption of specific building designs. This software takes the benefits of air barriers into account, as well as the negative effects of thermal bridging.
While thermal models do not explicitly require building envelope performance like the Prescriptive Guides, the economics of the building envelope do not change. A tight, well-insulated building envelope is key to cost-effective reduction in energy consumption. EIFS provide excellent insulation value and air barrier performance. Designers that use thermal modeling get the same cost and performance benefits from High-Performance EIFS as those that use Prescriptive Compliance options.
LEED Credits Synergistic with EA Prerequisite 2 - MR Credit 1.1 Building Reuse
USGBC defines synergy as an activity that makes a positive contribution to more than one LEED category. Recladding an existing building with EIFS facilitates reuse of the building, and also improves the insulation value of the building envelope. So EIFS can contribute to MR Credit 1.1 and EA Credit 1.
EIFS are an effective way to upgrade the appearance and curb appeal of an existing building while dramatically improving its energy performance.
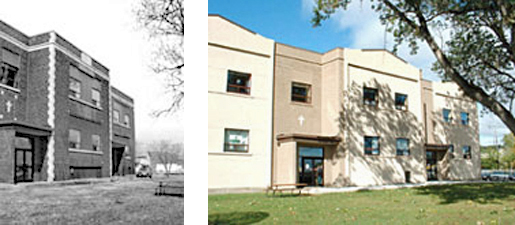
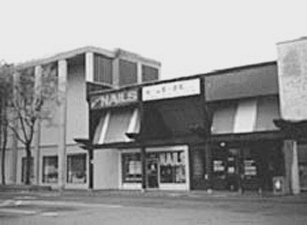
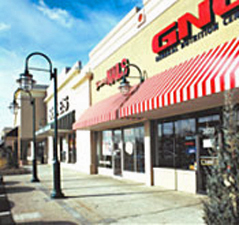
Recladding with EIFS refreshes curb appeal and adds insulation value.
LEED Credits Synergistic with EA Prerequisite 2 - EQ Credit 7.1 Thermal Comfort: Design
EIFS help attain this point as part of an overall plan to meet ASHRAE 55 requirements. The intention of ASHRAE 55 Section 6 is for the building envelope and HVAC system work together effectively, everywhere in the building. A building design that carefully integrates building envelope and HVAC systems design, as outlined in the EA Prerequisite 2 Section, clearly addresses this requirement of the ASHRAE 55 standard.
LEED Innovation and Design - ID Credit 1
The Innovation and Design credit makes provisions for innovations that benefit the environment. A major benefit of EIFS is their light weight. Not only does light weight translate directly to a lower resource demand and carbon footprint, it also dramatically reduces the embodied energy of a wall system. Lightweight EIFS reduce loading on the building frame and foundation, allowing other components of a building to be made lighter, further lowering their environmental burden.
Comparisons between EIFS, stucco, and brick walls made by RS Means1 have shown that on a metal framed wall, EIFS contribute 2 lbs/ ft², compared with stucco at 14 lbs/ ft² and brick at 42 lbs/ft². Replacing a 100,000 ft² brick wall with EIFS reduces weight by over 4 million lbs—a savings of over 95%!
This is true eco-efficiency — reducing environmental burden and the cost of construction.
Other Contributions to LEED Ratings
EIFS produce very little waste, most of which is recyclable or reusable. In this way, they contribute to Materials and Resources (MR) Credit 2 Construction Waste Management.
MR Credit 4 Recycled Content and Credit 5 Regional Materials are based on the weight percent of recycled and regional materials multiplied by the cost of the material. This final cost attributed to recycled and regional materials is divided by the total material cost of the building to create a final percentage. Buildings with greater than 10% recycled or regional material content are eligible for LEED points.
The relatively low cost of EIFS as a percentage of total building material costs limits the contributions that can be made to these credits. EIFS can contribute to these credits, but not as significantly as they contribute to other aspects of LEED.
LEED, EIFS, and Specification of Installation Quality
Every building is a one-of-a kind project, driven by schedules and economics. Quality control is an important part of the execution of every construction project.
LEED 2009 makes important contributions to quality control. Energy and Atmosphere Prerequisite 1 requires basic commissioning of building energy systems. While commissioning the building envelope is not required under EAp 1, it is recommended. Since a commissioning agent is required in any case, commissioning the building envelope simply requires broadening the scope of an existing commissioning agent.
Energy and Atmosphere Credit 3 provides 2 points for Enhanced Commissioning. The USGBC claims that costs involved in Enhanced Commissioning are often recouped in improved design and construction coordination, fewer change orders, and reduced operating costs. Enhanced Commissioning provides the opportunity to integrate effective quality control with attainment of a target LEED rating.
Conclusions
Architects have always been expected to balance the needs of a wide set of stakeholders to create designs that are functionally, aesthetically and economically effective. Sustainability adds a new dimension of challenge.
Those architects who are able to bring a systems perspective to these often-conflicting demands will have a competitive advantage over designers who select materials in isolation.
High-Performance EIFS can be used to advance multiple design objectives. They can create spectacular exterior appearances in a cost-effective manner. In addition, they can make significant contributions toward attainment of LEED Energy and Atmosphere Prerequisite 2 through specification of an air barrier and thermally efficient exterior insulation. Locating building insulation outside of the building sheathing helps move the dew point outside of the wall cavity, which is a necessary design practice in all climate zones.
Lightweight EIFS reduce overall material consumption in a given building design, with clear environmental benefits in terms of resource conservation and embodied energy reduction.
The significantly greater eco-efficiency of EIFS over alternate wall cladding materials suggests that these innovative cladding materials will be used more extensively as demand for cost-effective, sustainable building design continues to rise.
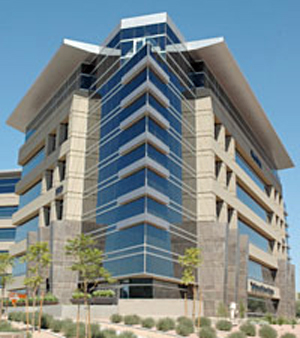
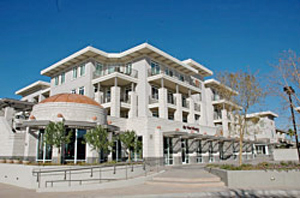
Lightweight, highly insulating EIFS can be used to create a wide range of textures and appearances.
Footnotes
1 [RS Means evaluation of brick, stucco and EIFS wall cladding systems prepared for BASF Construction Chemicals, LLC.]