Introduction
Within This Page
What is Off-Site Construction?
Off-site construction involves the process of planning, designing, fabricating, transporting and assembling building elements for rapid site assembly to a greater degree of finish than in traditional piecemeal on-site construction.
Off-site building includes a range of materials, scales and systems, digital software, methods of manufacture and fabrication, and innovations in social and technological integration.
Off-site outputs include componentized, panelized, and modularized elements deployed in the service of structural, enclosure, service and interior partition systems.
An optimizing strategy of off-site is to integrate these systems and supply chain through research, design, testing, and prototyping.
Across the spectrum of off-site products, modular, is the most complete in factory finish, up to 95% in some cases, shipped and assembled as 3D volumetric units that are service or structural units to be joined on-site.
The modular industry consists of two distinct industry segments: re-locatable modular and permanent modular. Re-locatable modular, sometimes referred to as temporary modular, are structures which meet temporary space needs and can be leased in a short-term agreement or purchased outright. Job site trailers, temporary classrooms, communication pods, and show rooms are some examples. Although permanent modular construction (PMC) has been flourishing for a decade or more in Europe, it is an emerging market in North America. PMC is comparable to site built structures meeting the International Building Code (IBC), the difference being that it is simply manufactured in chunks within a factory. PMC is deployed for multistory multi-family structures, government buildings, health care facilities, schools, hotels, and any other building types found in traditional on-site construction. Whereas three to four years ago PMC only constituted 25% of the market share in the modular industry, today it represents over 50%.
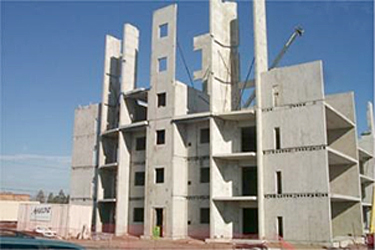
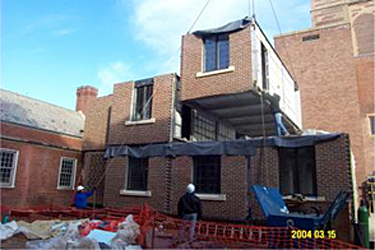
Precast concrete structure being assembled.
Steel modular and brick veneer at Yale University. Photo courtesy of Kieran Timberlake
The modular industry is host to both manufacturers, manufacturer direct, and dealers. Manufacturers produce modules to service general contractors or modular dealers. Manufacturer direct may manufacture for general contractors and dealers, but also contract directly with owners to provide modular solutions, acting as a general contractor. Both manufacturers and manufacturer direct organizations may be specifically focused on a particular building type, residential or commercial for example, or focus on re-locatable and/or permanent construction. Increasingly, however, manufacturers are becoming knowledgeable and skilled across the array of building types, markets, and industry segments.
Modular buildings, temporary and permanent, may be manufactured as structural units that make up the structure of the building once assembled on-site. Non-structural modular such as factory fitted bathroom or service pods can be placed within a larger modular superstructure or in traditional construction on-site.
Modules may be constructed from many different materials including: wood framing, cold-formed steel framing, hot rolled steel, concrete, or a combination of material assemblages. Not all manufacturers will manufacture in many materials; rather manufacturers tend to focus on a particular type of construction to maximize factory efficiencies. The choice of material by stakeholders is usually contingent upon project demands, site forces, and project cost. Further, projects may have a hybrid of material solutions such as traditional site built structure, bathroom modules, or structural modules and a portion of the building that is traditionally site built due to programmatic demands such as large openings, spans or other that are difficult to pre-assemble in the factory.
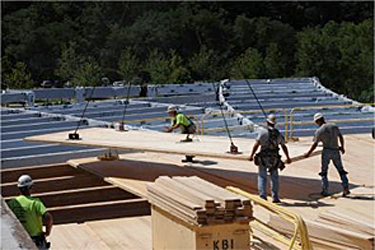
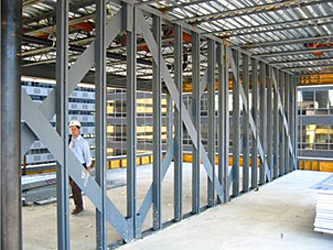
Cross-Laminated Timber roof panel being installed in Madison, Wisconsin. Photo courtesy of David Kretschmann, Forest Products Laboratory
Panelized shear wall system. Photo courtesy of AISC
Modular manufacturing uses an inside out approach to building. Modular frames are constructed as planes, fitted as boxes, and then finished from the inside out. For example, a dormitory unit may follow a sequence of frame, interior surface, electrical, plumbing, mechanical, insulation, exterior sheathing, and cladding. This differs from the traditional on-site assembly sequence of outside in, which restricts the multiple trades that work on top of one another during the build cycle. Factory production of modules avoids the difficulties of unpredictable weather, trades waiting on one another, and incessant delays associated with on-site construction.
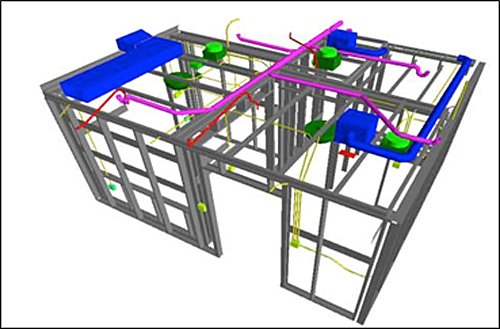
Building information model of an off-site constructed hotel room. Photo courtesy of Whiting Turner
The process of modular construction is quite different than on-site construction. This leaves many owners, architects, and builders confused and sometimes put off by the process. Dealers contract for delivery of re-locatable or permanent modular construction, acting as general contractor. With increasingly complex building projects, larger in size and requirement for MEP systems integration, dealers provide knowledgeable project delivery capacity between what is historically identically manufactured re-locatable mods in the temporary modular industry and sophisticated commercial construction solutions in the permanent modular construction industry. Together manufacturers and dealers are creating real value for project teams and building owners who are now embracing this form of construction and delivery.
Why Off-Site Construction?
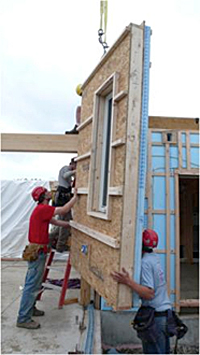
Prefabricated closed panel wall assembly for housing. Photo courtesy of Bensonwood Homes
Traditional contracts and on-site construction practices rigidly delineate responsibilities with much elaboration on the consequences of failure. This context reinforces risk-abating behavior, causing project teams to not engage in collaborative processes and present an adversarial construction culture, much to the disadvantage of all stakeholders. Owners are losing money on projects, architects and engineers are not seeing the quality of design increase, and contractors are bearing a great deal of financial burden and risk in the process. This fragmentation has been quantified in terms of waste and productivity.
Construction is essentially the design and assembly of objects fixed-in-place. Therefore, traditional buildings are site-produced goods, unique every time, and employ temporary teams—this triad might be called the peculiarities of construction, distinguishing it from other production industries. To make this process more productive we can remove the site, not make the building unique, and keep labor intact from project to project. Removing the site altogether is clearly not possible, but removing the site peculiarities to a degree vis-a-vis factory production certainly helps. Keeping teams in tact is an idea that has brought success to design-build entities and designers or builders who continually engage with the same engineers, contractors, and subcontractors. Modular production has the capacity to keep teams more intact by controlling the workflow. Finally, the uniqueness of the building design and production process is a variable that may in fact be controlled (or segments within the work flow at least), removing waste and adding value in the building process.
Further comparing construction to manufacturing, according to the U.S. Bureau of Labor Statistics, 57%, of activities in construction are wasteful and non-value adding. These are activities that are not compensated. Manufacturing is directly opposite with 62% of all activities being value adding. Replacing the wasteful elements of construction with manufacturing benefits through modular processes can remove waste and increase value for projects.
Increasing construction efficiency through modular requires examination of construction performance. Every project must consider a number of performance factors including:
- Cost: capital and operational investment
- Labor: skilled and unskilled human workforce
- Scope: extent or breadth of project program
- Quality: meeting or exceeding design and construction goals
- Risk: exposure to potential financial loss
Although not all of the factors will be equally valued in any given project, they generally have a contingent relationship to one another. For a given program, the design team usually establishes relationships, maybe even unknowingly, between quality, schedule, and budget where one change affects all the others. For example, an owner team may opt to select a lower quality material in favor of saving cost or allow the project to be completed on time. In this balance of factors, risk plays a critical component.
Off-site and permanent modular in particular, is not a blanket solution to every building project. As such, the principles of cost, schedule, labor, scope, quality, and risk represent a sliding scale of opportunity and tradeoffs rather than definitive answers. When enacted intentionally and with pre-planning, modular construction can be a solution to help find balance between these sometime competing performance goals of construction. Off-site delivery and early planning are co-lateral concepts. Engaging the off-site fabrication industry early in the design process to help solve this equation is fundamental to successful utilization of the off-site design and construction process.
Much research has been performed and is ongoing regarding the benefits of off-site construction. Documented benefits of off-site construction versus traditional on-site construction include:
- shorter construction schedules
- greater degree of predictability in cost
- reduced material waste
- reduced carbon emissions due to transportation to and from site associated with on-site construction
- reduced site disturbance, and finally
- an increase of safety and security of laborers and trade equipment.
Labor productivity has shown an increase of 30% on off-site projects when compared with on-site projects. Ultimately, risk is reduced with off-site construction. (McGraw Hill 2009; FMI 2013; Mortenson Construction 2014; Quale et al 2012)
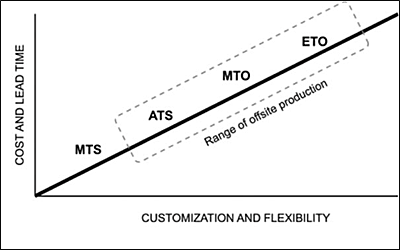
Range of off-site production in the construction sector. Graph courtesy of R.E. Smith
Numerous projects have demonstrated that schedule savings are the most easily documented and noticeable savings that occurs as a result of modular construction. Savings from 15%–50% by virtue of modular construction is not uncommonly reported. This is due to concurrent site and factory work, as well as factory production being faster than on-site framing, removing weather delays and subcontractor sequence delays associated with on-site construction.
Clearly, material waste is reduced because fall off is recaptured in the manufacturing stream. However, the greatest environmental benefit demonstrated by off-site construction documented in a recent publication in the Journal of Industrial Ecology is attributed to the reduction in transportation energy and carbon as a result of workers commuting to a factory instead of the job site and supply yards throughout the day. (Quale et al 2012) Modular and panelized construction projects are regularly meeting LEED standards today.
There are also notable disadvantages to off-site construction that should be pointed out:
- Structural bulkiness: floor to floor heights and wall thicknesses affected
- Transportation restrictions limit module and panel size
- Spans and configurations of design are somewhat restricted
- Lack of transparency in overhead, profit margin, transport, setting (cranes), and associated increase in designer fees if new to the process.
- Flexibility and changeability of structure through future renovations becomes more difficult
How Does the Off-Site Process Work?
The off-site industry has grown from primarily a re-locatable modular manufacturing sector to a building delivery sector. This presents difficulty for both manufacturers of panels and units and the traditional building industry that do not understand off-site, its delivery process, and how to engage effectively in that process. Because of this history as a re-locatable modular industry, these manufacturers are accustomed to delivering buildings on turn-key contracts in direct negotiation with owners. This may in fact be desirable for owners on certain kinds of projects that need a one-stop shop approach.
However, on more complex projects, the off-site industry is less experienced. Manufacturers engaging in the design and delivery process for the duration of an extended building project involving numerous project stakeholders including designers, general contractor, and many trades and contracts including design/build, design-bid-build, CM, and other forms of mainstream construction agreement, are facing relatively new territory.
An ideological and structural shift in the construction industry is occurring with the abandonment of traditional design-bid-build contracts toward design-build and integrated project delivery that rely on performance contracting and shared risk and reward. Off-site construction is a synonymous concept with integrated delivery. Research shows that projects that decide to utilize off-site after the design development phase have demonstrated a negative impact on both schedule and budget as a result of employing modular too late in the process of building delivery.
Ideally, stakeholders on off-site projects would ask the following questions across typical project phases as outlined in Prefab Architecture (Smith, 2011).
- Predesign: Does off-site aid in meeting the cost, time, labor, site and programmatic goals for the project?
- Design: Is the project designed in integration with stakeholders for off-site manufacture, transport, assembly and disassembly if required?
- Develop: Is the design of the project developed so that work is structured for what is done on-site and what is manufactured in the factory?
- Detail: Is detailing developed in collaboration with the design team, general contractor, fabricator and installer?
- Order: Are design changes reduced and are orders placed in a short time frame to reduce cost?
- Fabricate: Is fabrication performed with prototypes and lead times reduced in coordination with the project team?
- Deliver: Are site deliveries made just-in-time, loaded and delivered to minimize handling?
- Assemble: Are assembly operations designed collaboratively as continuous follows to ensure safety, quality, time and cost parameters are met?
Some differences that should be considered with off-site delivery versus traditional on-site include:
Most states require a third party agency and/or have a state program that regulates the design, approval and inspection of the building at the manufacturing plant and an on-site inspector for siteworks. The extent or impact of these programs varies from state to state as well as the associated cost of such.
Transportation regulations are also handled state-by-state. Therefore, shipping from a state in which a module is manufactured to another state where the site is located will require differing codes, permitting, lead cars, and various associated fees. Each project should carefully ensure this is well considered. A general rule of thumb is 500 miles maximum for shipping from a manufacturer to a job site. On average, modular manufacturers, for example, are approved to build in 20 states.
Special engineering may be required to ensure modules are structurally robust enough for dynamic load associated with transport. Often, manufacturers or dealers will have their own engineers in-house, in addition to the engineer of record in permanent modular projects that are servicing a traditional design and build team contracted with the owner.
Pick points where the panel or module will be lifted from the truck trailer by a crane and set on-site is to be designed as part of the element structure. Wooden modules may use a wraparound belt strap. The most common crane used for setting elements is a truck mounted hydraulic crane, crawler crane and, in special circumstances, a tower crane. A determination on who will set the elements should be determined early during contract negotiations.
Critical Path Method is the most common method of construction scheduling where trades are stacked sequentially on-site. In off-site construction, concurrent scheduling overrides CPM, requiring a construction professional approach construction scheduling, cost, labor and supply chain management in a radically different way, to the advantage of the overall schedule of the project.
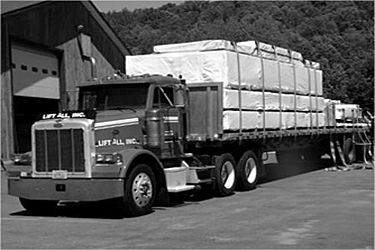
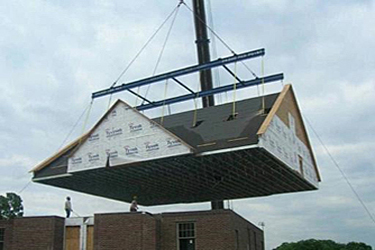
Flat pack delivery. Photo courtesy of Euclid Timber
Roof assembly being delivered and installed on-site. Photo courtesy of Whiting Turner
When Should Off-Site Construction be Used?
The intention here is not to say that off-site generally and any one off-site system is an appropriate solution to every building problem. Off-site has performed better on some building types, with certain building teams and in certain locations. These guidelines are not meant to be definitive but suggestive of consideration that should be taken when deciding if off-site is appropriate.
Projects that are restricted by schedule such as schools and dormitories that must open for new school year or semester, embassies that must be built for operations in a foreign country quickly, or retail units that must open doors to gain an increased return on revenue. It is hard to think of any building type today that does not demand a shorter construction schedule.
Repetitious projects such as identical classroom units, dormitory units, office units, laboratories, high-tech facilities, communication structures, and bathroom pods. Projects that employ unique forms, unique sustainability requirements, or a higher degree of control in the end product also stand to benefit from off-site construction. The factory provides space for prototyping, quality control and ability to integrate complex systems. As such, off-site is restricted to box forms, and unique projects may in fact demand geometric forms that off-site construction cannot provide.
The delivery method selected by the owner can have a large impact in determining if off-site is used or not. Although off-site can be used in any contract form, design-bid-build contracts without consideration to means and methods by the contractor during the design process or construction manager contracts that make decisions concerning construction method without input from owners can work against off-site delivery. This can be mitigated by selecting design-build or integrated contracts that allow for early fabrication decision making by owners, designers and builders partnership with dealers and/or off-site product manufacturers direct through design assist during the planning and schematic phases of development.
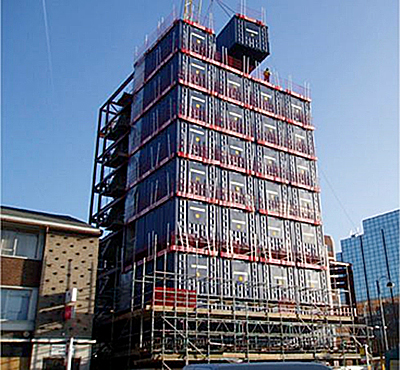
Travelodge construction using off-site container modules. Photo Courtesy of Travelodge
There are a few characteristics of team members that are determinants of off-site employment. These include:
Experience of the team using modular construction in previous projects aids in using off-site again. Design team members and contractors that have off-site experience have fostered confidence and skills to deliver again. These skills are different than on-site construction, as we have discussed, where the act of coordinating shipping, setting and stitching demands an integrated process.
Repetition of the team working together on multiple projects builds trust between stakeholders. This is especially true for project stakeholders working with a specific dealer and manufacturer for a sequence of projects that allow a continuous workflow and repeated process of decision-making, roles and responsibility.
An owner that wants to maintain control and predictability of project costs, schedule, and quality may choose off-site over traditional on-site delivery. In addition, an owner that has capital to invest in off-site at the beginning of a project has a higher chance of realizing its successful employment as early project payouts and draws may be necessary per the contract agreement with the manufacturer.
There are a few project location determinants for off-site:
Sites that are accessible, land that is affordable, and construction seasons that are year round are less likely to benefit from off-site factory production. However, remote sites and highly dense urban sites, where on-site construction would be difficult to access, sites with a short build season, or sites with expensive land that require any means possible to reduce overall construction budgets benefit from off-site the most.
In addition, locations where the access to a wide range of affordable materials, lower levels of manufacturing of components that use stick elements or planar elements, and access to affordable labor are less likely to deploy off-site construction.
Finally, not all building code jurisdictions are as open to off-site construction. This may require building teams to take extra care and precaution to prepare alternate means for permitting and inspection. These may be met with longer review and reporting cycles than would normally be experienced in traditional on-site construction. The best bet is to check with your local building department to determine the process for requirements of off-site regulatory review.
Conclusion
Off-site construction can service a variety of building and construction types such as education, housing, health care, office, government, dormitory, retail, and hospitality. Off-site is a building process of delivery as much as it is an amalgamation of building products. When understood and deployed by stakeholders intentionally, with early project planning, it is a well-suited solution to control project schedules and budgets while increasing quality and reducing environmental impact. Off-site construction is especially effective when employed to shorten building cycles, on repetitious or unique projects, and with teams that are prepared to embrace the challenges and opportunities associated with its delivery.
Additional Resources
Organizations
- American Institute of Steel Construction
- BuildOffsite
- Centre for Offsite Construction + Innovative Structures
- Integrated Technology in Architecture Center
- Modular Building Institute
- Precast/Prestressed Concrete Institute
- Structural Building Components Association
- Structural Insulated Panel Association
- WoodWorks™
Publications
- Better Building through Off-site Construction Mortenson Construction, 2014.
- Construction Matters by Quale, J., M.J. Eckelman, K.W. Williams, G. Sloditskie, and J.B. Zimmerman. Journal of Industrial Ecology, 2012.
- MBI White Paper: Modular Building and the USGBC's LEED Version 3.0 2009 Building Rating System
- Modular Design Guide by Lawson, M, Ogden, R, & Goodier, C. CRC Press, 2014.
- Off-Site Studies: Permanent Modular Construction, Process, Practice, Performance, 2015.
- OFFSITE: Theory and Practice of Architectural Production, Abstract Book, Association of Collegiate Schools of Architecture 2012 Fall Conference Proceedings by Smith, R.E., Quale, J. & Ng, R., ACSA Press, 2012.
- Prefab Architecture: a guide to modular design and construction by Smith, R.E. John Wiley & Sons, Inc., 2011.
- Prefabrication and Modularization in Construction 2013 Results . FMI, 2013.
- Prefabrication and Modularization: Increasing Productivity in the Construction Industry. SmartMarket Report. McGraw Hill, 2009.
- WRAP Report Current Practices and Future Potential in Modern Methods of Construction