Introduction
Within This Page
Responsible management of waste is an essential aspect of sustainable building. In this context, managing waste means eliminating waste where possible; minimizing waste where feasible; and reusing materials which might otherwise become waste. Solid waste management practices have identified the reduction, recycling, and reuse of wastes as essential for sustainable management of resources.
Most construction and demolition waste currently generated in the U.S. is lawfully destined for disposal in landfills regulated under Code of Federal Regulations (CFR) 40, subtitles D and C. In some areas all or part of construction and demolition waste stream is unlawfully deposited on land, or in natural drainages including water, contrary to regulations to protect human health, commerce and the environment. Businesses and citizens of the U.S. legally dispose of millions of tons of building-related waste in solid waste landfills each year. Increasingly, significant volumes of construction related waste are removed from the waste stream through a process called diversion. Diverted materials are sorted for subsequent recycling, and in some cases reused. Volumes of building-related waste generated are significantly influenced by macroeconomic conditions affecting construction, societal consumption trends, and natural and anthropogenic hazards. In recent years, construction industry awareness of disposal and reuse issues has been recognized to reduce volumes of construction and demolition waste disposed in landfills.
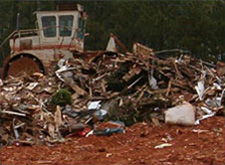
C&D landfill cell
Many opportunities exist for the beneficial reduction and recovery of materials that would otherwise be destined for disposal as waste. Construction industry professionals and building owners can educate and be educated about issues such as beneficial reuse, effective strategies for identification and separation of wastes, and economically viable means of promoting environmentally and socially appropriate means of reducing total waste disposed. Organizations and governments can assume stewardship responsibilities for the orderly, reasonable, and effective disposal of building-related waste, promotion of public and industry awareness of disposal issues, and providing stable business-friendly environments for collecting, processing, and repurposing of wastes. Businesses can create value through the return of wastes back to manufacturing processes, promoting and seeking out opportunities for incorporation of recycled materials into products, and prioritizing reduction of building-related wastes through efficient jobsite practices.
Description
Effective management of building-related waste requires coordinated action of governmental, business, and professional groups and their activities. Several non-governmental organizations and societies in the US promote coordinated action, and have identified best management practices in the interest of public health and welfare (see resources.) Absent coordinated regulations, realistic business opportunities, and the commitment of design and construction professionals and their clients for continual improvement of industry practices, consistent and stable markets for recovered materials cannot be achieved or sustained.
Management of building-related waste is expensive and often presents unintended consequences. However, common sense suggests that failure to reduce, reuse and recycle societal wastes is unsustainable. It stands to reason that efficient and effective elimination and minimization of waste, and reuse of materials are essential aspects of design and construction activity. Creativity, persistence, knowledge of available markets and businesses, and understanding of applicable regulations are important skills for design and construction professionals.
Eliminating Waste
Some waste generated in the process of construction can be eliminated. For example, durable modular metal form systems for use in concrete construction may be selected on the basis of being readily demountable and reusable on other projects, thus eliminating wood waste associated with formwork fabricated of plywood and dimensional lumber. Elimination of waste can be beneficial to reduce impacts on human health and the environment.
Minimizing Waste
Some building-related waste can be minimized. For example, construction products can be selected on the basis of its being designed and manufactured to be shipped with minimal packaging. Also consider that selection and use of recyclable materials and products offers potential to minimize waste.
Reusing Materials
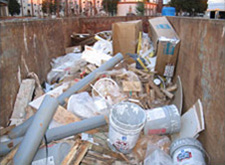
Commingled C&D waste in roll-off
Some materials can be reused. For example, doors and windows in good, resalable condition might substitute for new products, or be donated and or sold for use on another project—a form of beneficial reuse.
Materials and products which cannot efficiently and effectively be eliminated, minimized or reused ultimately are collected, and unless managed, will probably be disposed at the lowest cost. In many areas of the country, disposal fees at solid waste landfills are substantially higher than the cost of separation and recovery, including the disposal cost for residues.
A. Federal Regulations
In the United States, the Resource Conservation and Recovery Act (RCRA) defines the subset of solid waste known as hazardous waste. The term "hazardous" was intended to designate wastes that present a serious risk to human health and the environment when mismanaged. Several components encountered as part of construction and demolition materials operations are RCRA hazardous wastes and therefore processes must meet all of the regulatory management requirements for hazardous waste. Note that hazardous most hazardous components encountered with construction and demolition materials operations are identified by respective characteristics, rather than listing. For example, discarded paints and solvents would have ignitability characteristics; batteries would have corrosivity characteristics.
In Canada, the Canadian Environmental Protection Act, 1999 (CEPA 1999) is the primary element of the legislative framework for protecting the Canadian environment and human health. In Canada, each level of government has powers to protect the environment. Collection, diversion, and disposal operations are the responsibility of municipal governments, while the approval, licensing and monitoring of operations are the responsibility of the provinces and territories.
B. Management
Most construction and demolition debris is generated at the project level and therefore subject to laws and regulations by local, state, provincial, and federal laws. Construction and demolition debris is defined at the state level in the United States, and at the provincial level in Canada. Check local, state, and provincial regulations to verify correct interpretation of the law.
Local practices in the management and disposal of construction and demolition wastes often are shaped by the availability of suitable disposal sites, economic conditions, societal priorities, availability of markets for recycling and reuse, transportation options, and the capabilities of local workforces and construction businesses to adapt demolition processes for management of wastes.
Management of construction and demolition wastes is addressed at project, organization, and disposition levels.
Project Level—Enhancing project value and performance
The project level encompasses the work of a specific project or projects, and is administered by the project team, often led by the architect or engineer during the design phase. The project level requirements are often communicated through project specifications, and contract provisions. Green building certification programs, notably LEED, include protocols, measurement and verification targets, and documentation that may be helpful to ensure project goals are achieved.
Organization Level—Stewardship of corporate values and priorities
The organization level encompasses the management of wastes identified at the project level, and includes the business practices and priorities of building owners and general contractors. The organization level provisions are often communicated through corporate reports, policy statements, and work plans. Performance measured against corporate targets for diversion, reduction in greenhouse gas emissions, and sustainability metrics are increasingly being recognized in industry programs recognizing corporate green building practices. Organizations can work with vendors responsible at the disposition level to ensure that business practices and operation of segregation, sorting, transporting and final disposition of wastes meet or exceed corporate expectations.
Disposition Level—Management of diversion and disposal
The disposition level encompasses the segregation, sorting, handling, transporting and final disposition of wastes, and is administered by the businesses and agencies responsible for disposal under contract or agreement, under licenses, and in accordance with all laws and regulations. Communication is often provided in the form of written diversion reports tabulating the amounts of materials accepted, diverted, and disposed, and the locations of final disposition of the materials received. Service providers at the disposition level can work with building owners and general contractors for project-specific approaches to managing waste, including custom diversion plans tailored to the project opportunities.
C. Definitions
Alternative Daily Cover (ADC): Material having no value in reuse, although employed for beneficial use as a supplement to soil in the practice of applying earth cover over active portions of managed municipal solid waste landfills, thus covering the day's waste, and with the effect of reducing nuisance odor and exploitation by animals, birds and insects.
Beneficial Use: An assertion of right to enjoy the benefits of specific property. Industry best practices promote inspection and evaluation of materials and products proposed for reuse to be certain hazards are mitigated, for example: window assemblies which include caulking containing PCB compounds; friable asbestos containing products; light fixture ballasts; etc generally pose risks to human and environmental well-being.
Canadian Environmental Protection Act, 1999 (CEPA 1999): CEPA consolidated selected provisions and laws administered by Environment Canada, and provides a framework for the management and control of toxic substances at each stage of their life cycle from development and manufacturing/importation through transportation, distribution and use, storage and ultimate disposal as waste.
Commingle: A term referring to the practice of placing unrelated materials together in a single container, usually for benefits of convenience and speed, but presenting challenges for subsequent recovery and diversion.
Construction Waste: Waste generated by construction activities, such as scrap, damaged or spoiled materials, temporary and expendable construction materials, and aids that are not included in the finished project, packaging materials, and waste generated by the workforce.
Demolition Debris: Waste generated from the process of intentional dismantling all or portions of a building, and clearing of buildings and contents destroyed or damaged as a result of natural or anthropogenic hazards. Demolition debris often contains constituents regulated in the US as hazardous waste under RCRA Subtitle C, 40 CFR.
Disposal: Depositing waste in a solid waste disposal facility, usually a managed landfill, regulated in the US under RCRA Subtitle D, or in the case of hazardous waste, under Subtitle C, 40 CFR.
Diversion: The practice of diverting waste from disposal in a landfill, by means of eliminating or minimizing waste, or reuse of materials.
Diversion Report: A written assertion by a material recovery facility operator identifying constituent materials diverted from disposal, usually including summary tabulations of materials, weight in short-ton units (NIST), and percentages.
Industrial Waste Stabilizer (IWS): Material having no value in reuse, although employed for beneficial use in stabilization of industrial waste in landfills.
Landclearing Debris: Waste generated from the process of clearing land, including preparing building sites for construction, generally consisting of vegetation, soil, rocks, and constituent matter.
LEED: An internationally recognized green building certification system, providing third-party verification that a building or community was designed and built using strategies intended to improve performance in metrics such as energy savings, water efficiency, CO2 emissions reduction, improved indoor environmental quality, and stewardship of resources and sensitivity to their impacts.
Organics: Vegetation, soils, and constituent matter excluding rocks, and being both carbon- and nitrogen-rich, and completely biodegradable to carbon dioxide, water and biomass through the action of micro-organisms under normal environmental conditions.
Recycling: Introducing a material into some process for remanufacture into a new product, which may be the same or similar product or a completely different type of product.
Residue: Waste which is economically impractical to recover for reuse or to divert from disposal.
Resource Conservation and Recovery Act (RCRA): The principal Federal law in the United States, enacted in 1976 and amending the Solid Waste Disposal Act of 1965, with the intent of governing the disposal of solid waste and hazardous waste, and codified in Title 40 CFR. Construction and demolition debris are regulated under Subtitle D: Non-hazardous solid wastes. Hazardous wastes are regulated under Subtitle C, known as the 'cradle to grave' system with stringent bookkeeping and reporting requirements. RCRA authorizes states to carry out many of the federal regulations through their own state laws, with such laws subject to approval by the EPA.
Reuse: The subsequent use of a material, product, or component upon salvage.
Salvage: Recovery of components, products, or materials for the purpose of reusing them for the same or similar purposes as their original use.
Sortline (or Pickline): An item of industrial recycling equipment featuring a conveyor belt and several stations for workers to rapidly sort and segregate waste, usually part of a material recovery facility.
Source Separation: A term referring to the practice of administering and implementing a management strategy to identify and segregate unrelated waste at the first opportunity, thus simplifying subsequent processes for recovery of materials and diversion, but presenting challenges for management of space on the jobsite, training and supervision, and inefficiencies associated with hauling.
D. Construction and Demolition Wastes
Wastes encountered constitute all the materials and products incorporated into the built environment over a period of decades or in some areas over centuries. Include in that list earth, pavement, and organic plant materials. Assessment of wastes to be encountered on projects is an important first step in developing a construction and demolition waste management plan at the project level.
Industrial hygienists perform waste characterization studies and identify components which present known risks to human health and the environment. Specialty contractors provide comprehensive services for identification, verification, removal, handling and disposal of known and suspect hazardous and dangerous materials in accordance with applicable regulations.
Materials and products presenting known risk:
- Hazardous wastes (listed, characteristic and universal types identified by US EPA)
- Asbestos-containing materials (friable)
- Asbestos-containing materials (non-friable)
- Lead-containing materials
- Products containing polychlorinated biphenyls (PCBs)
- Solvents, chemicals, petroleum-derived products
- Dust
- Fluorescent and compact fluorescent lamps
- Electronics
- Medical waste
- Materials contaminated with waste
Materials and products typically benign:
- Woody and plant materials
- Concrete
- Gravel, aggregate, stone and rock
- Masonry and rubble
- Metals (ferrous and non-ferrous)
- Wood
- Plastic
- Glass
- Doors and windows
- Asphaltic roofing
- Gypsum board
- Carpet and pad
- Cardboard and paper
- Plumbing fixtures
- Lighting fixtures
E. Best Management Practices
How waste management, or diversion, is accomplished, and to what extent, depends on specific project requirements and conditions. Several issues contribute to an overall waste diversion strategy.
F. Process
Jobsite Sorting
Efficient identification and sorting of materials is an important factor in managing the economic viability of diverting construction debris from disposal. Jobsite protocols are identified in contracts and subcontracts, and implemented at the project level by superintendents and project managers. Superintendents and project managers utilize project specifications prepared by architects and engineers for information on diversion target rates, and general performance requirements. Building owners and contractors may have corporate guidelines and policies which improve upon project specific requirements. Materials may be sorted into a number of containers provided by service companies that specialize in management of specific types of waste at the jobsite. Generally the least number of containers is desirable both to keep container volumes high to reduce transportation trips and costs, and to keep the jobsite clear of obstructions.
Collection and Hauling
Containers containing construction and demolition waste are collected and transported to diversion facilities via truck. Light and medium duty trucks are most commonly used for this purpose in the US and Canada. Trucks and containers of various types are mated to allow for maneuverability and modular interoperability.
Tipping
Identification of loads on arrival at construction and demolition debris diversion facilities is an important step in ensuring materials are appropriately handled. Facility management plans typically describe materials that can be accepted. Loads which contain materials that are not accepted may be turned away, in which case the materials likely will be disposed in a sanitary landfill. The four hazardous waste characteristics are: corrosivity, ignitability, reactivity, and toxicity.
Picking
Materials are typically handled with equipment specifically designed to support heavy loads and resist abrasion. Materials are discharged from containers onto a tipping or receiving floor, usually beneath a roof cover or inside an industrial building. Once on the floor, a wheel loader operator will stockpile materials which will be picked through with a hydraulic excavator or a grapple. Materials such as steel reinforcing bar, carpeting, large pieces of wood, concrete and materials with dimensions greater than 3 feet are usually picked before the sorting process can begin in earnest.
Sorting
Sorting generally involves loading materials onto an inclined metal belt—a chainbelt—and passed across a manual sortline consisting of a flexible rubber belt and integral sort stations providing a place for several workers to stand, usually opposite from one another down the length of the belt. Materials are identified, grabbed, and deposited in vertical openings at each sort station. The effectiveness of the manual sort line is largely determined by the performance of the picking operation which precedes it; for example large materials on the belt can be difficult to manage and or obstruct recoverable materials passing by on the belt beneath.
Containerization and Transport
Picked and sorted materials are deposited by means of equipment and manual labor into industrial containers of various types. Combination compactor-balers are used in some applications to produce dense bales of materials which are then loaded into intermodal shipping containers for transport. Heavy interstate trucks are an important part of the transportation system. Containers of all types are destined for transport locally, regionally, nationally and internationally via road, rail, or barge via intermodal facilities such as railyards and ports. Once containerized, recyclable materials are commoditized and traded in the global marketplace.
Diversion or Disposal
Diverted materials are destined for incorporation in new products as recycled material, or are processed for reuse. Materials destined for disposal in landfills include refuse, materials contaminated with waste or which have been ruined, and materials for which markets do not exist.
G. Prevalence of Common Materials
Constituent proportions of materials culled and sorted in the construction and demolition waste stream shows a high degree of correlation with local priorities and economic trends at a given time. For example, communities with a preponderance of 19th century buildings and undergoing gentrification tend to have a larger proportion of masonry waste as contrasted with a suburban neighborhood undergoing renovations and additions to lightly-built wood frame structures. Diversion performance over a two year period (2009-10) processing 20,000 tons of construction and demolition waste generated in an urban area in the US (2010) demonstrates the following proportions:
Ferrous and non-ferrous metal—9%: Ferrous and non-ferrous metals are among the most valuable materials in the construction and demolition waste stream. Ferrous metals are extracted from bits of concrete with hydraulic excavating equipment, and deposited into containers. Small bits of ferrous metal are collected with electromagnets positioned over the sortline belt, and grabbed manually. Non-ferrous metals, predominantly aluminum, are collected with a reverse magnet known as an Eddy current separator, and grabbed manually. Metals consistently demonstrate the highest diversion rate of all the recoverable materials.
Cardboard and Paper—3%: Cardboard and paper recovered from construction and demolition debris waste have value as recyclable materials, however are generally of a lower grade than cardboard collected at curbside, as a result of consequential exposure to water, and contamination with dusts. Cardboard and paper are usually baled for economical transport to paper and cardboard mills.
Plastic—1%: Post-consumer plastics 1 (PET) & 2 (HDPE) are valuable commodities. Plastics 3 through 7 are generally recyclable but have less value. Generally plastics are not recycled into material of the same type and grade (downcycled). PET is readily converted into a wide variety of products. HDPE is downcycled into plastic lumber, trash receptacles, etc. Plastic film is a nuisance material that impedes efficient picking and sorting of all other materials. When prices of the recycled commodities are low, plastic materials may be exported and or combusted for their energy-producing potential. Plastic may be granulated or chopped into flakes and placed in industrial tote bags for transport.
01: Polyethylene terephthalate (PET) 02: High-density polyethylene (HDPE) 03: Polyvinyl chloride (PVC) 04: Low-density polyethylene (PE-LD) 05: Polypropylene (PP) 06: Polystyrene (PS) 07: Other (O)
Wood—30%: Wood is a predominant material for waste streams in North America, and is highly useful in a wide variety of industrial processes including manufacturing of high recycled content products. Wood is a valuable commodity and merits diversion. Wood waste can also be processed to make feedstock for biomass and combined heat and power plants.
Concrete—5%: Concrete is crushed, and embedded metals removed for recycling. Rock and cement pieces are crushed, screened and separated to produce useful aggregates of various dimensions. It is advisable to characterize painted concrete and concrete which has been contaminated with wastes before recycling.
Industrial Waste Stabilizer (IWS)—25%: IWS is a form of diversion or disposal in some parts of North America whereby materials with no economic value between 0.75 to 8 inches dimension are disposed in industrial waste landfills, to promote physical stabilization of the landfill.
Gravel, aggregate and fines—20%: Gravel, small stones, concrete chips and similar materials can be diverted from disposal with trommel screens positioned before the inclined chain belt, or debris roll screens positioned at the end of the sortline belt.
Disposal as refuse—5%: Refuse passes off the end of the sortline belt. Generally the proportion of refuse should be less than 10%.
Window glass—0.15%: Window glass is a nuisance material with a nominal value as a recyclable commodity. Its relatively high weight per volume is a factor in restricting economical transport. Window glass usually ends up in a landfill unless a recycler is located in the vicinity of the diversion facility.
Carpeting—0.85%: Diversion of carpet from the landfill is very significant in reducing greenhouse gas emissions associated with manufacture of new carpet. Carpeting is a nuisance material in the picking and sorting process, complicating the efficient recovery of materials with higher values. Carpeting is generally picked from stockpiles on the receiving floor, and deposited in containers for transport to manufacturers who can make use of the fiber materials to make new products.
Drywall—3%: Drywall is 100% recyclable. Gypsum is a nuisance material in picking and sorting operations, producing dust which discomforts labor, and reduces the value of recyclable materials through contamination. Gypsum may be incorporated into new drywall, or used as a soil amendment.
Asphalt roofing—5%: Asphalt roofing shingles may be ground, sized and graded for remelting in asphalt paving applications, road base, new roofing, and fuel oil. Asphalt shingles consist of felt saturated with asphalt, and with mineral stabilizers and rock granules added. Asphalt constitutes 20 to 35% of the product weight. Contaminants including metal items and any wood waste must be removed.
Usually destined for other facilities: Appliances, equipment, tires, electronics, plumbing fixtures, asphalt, non-ferrous materials including copper, brass and stainless steel, landclearing debris. These materials may have value in secondary markets when one is available, or require special handling and management such as is the case with tires and appliances. Tires must be shredded in order to reduce the likelihood of being disposed of in unmanaged tire landfills. Appliances may contain refrigerants and other materials which pose environmental hazards.
Usually destined for reuse: Doors, windows, hardware: these materials often have value in a secondary market when one is available.
Nuisance materials: Sheet plastic, carpeting, drywall each require specific handling procedures to promote efficient handling of the rest of the waste stream. When commingled with other construction and demolition waste, these materials are generally picked with hydraulic excavating equipment or grapples—a costly and time-consuming process - before the bulk of waste is loaded onto a chainbelt and passed across a manual sort line.
1. Waste Management Planning
Waste management should be an integral part of a project's development. Each of the principal project participants—the Owner, their Architectural and Engineering (A/E) services (or Construction Management consultant), the Contractor, and Subcontractors—will engage in waste management to some degree throughout the project. Initially, the Owner and their A/E must establish waste reduction goals and define what levels of diversion are achievable and reasonable under the project's conditions and as required by:
- State and local regulations
- U.S. EPA
- State statutes or
- Green Building Rating program requirements.
2. Facility Design
The Contractor is responsible for the means, methods, techniques, sequences, and procedures of construction, which include waste disposal methods. However, the A/E's design team can contribute to waste reduction in several ways. These include:
Observe Value Engineering principals. Perform multiple functions with one material rather than requiring multiple materials to perform one function. Design to optimize systems' and components' use. Avoid extraneous materials that do not contribute to function.
Be efficient in area and volume. If less material is required by the design, less waste is generated at the jobsite.
Observe standard material and product dimensions. Locate features "on module" to the extent possible to reduce cutting and special fitting, which creates scrap.
Where possible, select construction systems that do not require temporary support, shoring, construction aids, or other materials that will be disposed of as debris during the project.
Where possible, select materials that do not rely on adhesives, which require containers and create residue and packaging waste. Furthermore, adhesives inhibit salvage and recycling at the end of the component's or building's life.
Where possible, reduce requirements for applied finishes, laminates, coatings, adhesives, and the associated scrap, packaging, and waste. Select materials with integral finishes.
Where possible, avoid materials which are sensitive to damage, contamination, environmental exposure, or spoilage on-site, which increase the potential for jobsite waste.
3. Construction Contract Requirements
The Owner and their A/E (or CM consultant) must determine how their waste management requirements will be represented in the contract documents and incorporated into the project. Several provisions are relevant to the project's overall waste reduction performance.
- There are essentially three ways to represent waste reduction requirements in the contract documents.
- Describe the waste reduction goals and rely on the Contractor's own initiative to achieve them. This may be effective if the Owner and Contractor share a good working relationship, and encouraging the Contractor is sufficient for them to "do the right thing."
- Specify definitive minimum waste and debris diversion criteria. This is commonly incorporated into the Demolition specification as a numerical criterion, such as "divert from landfill disposal a minimum of 75% of the non-hazardous construction waste generated at the jobsite."
- Develop incentives to reward the Contractor. This may be implemented as an award-type incentive based on the diversion rate, or by including Options in the Bid Schedule for each of several ranges of diversion rates. Note that simply requiring a specific LEED rating does not guarantee credit MR 2.1 or 2.2 (50%, and an additional 25% C&D waste diversion, respectively) will be attained. If the Owner, and their A/E or CM consultant desire to rely only on LEED as their requirement for environmental performance, they can still specify that MR-2.1 or MR-2.2 are mandatory for the project.
- Require the Contractor to submit a C&D Waste Management Plan. Typically, the Plan includes the following:
- Name of individual(s) responsible for waste prevention and management.
- Actions that will be taken to reduce solid waste generation.
- Description of the regular meetings to address waste management.
- Description of the specific approaches to be used in recycling/reuse.
- Waste characterization; estimated material types and quantities.
- Name of landfill and the estimated costs, assuming no salvage or recycling.
- Identification of local and regional reuse programs.
- List of specific waste materials to be salvaged and recycled.
- Estimated percentage of waste diverted by this Plan.
- Recycling facilities to be used.
- Identification of materials that cannot be recycled or reused.
- Description of the means by which any materials to be recycled or salvaged will be protected from contamination.
- Description of the means of collection and transportation of the recycled and salvaged materials.
- Anticipated net cost or savings. Some examples of C&D Waste Management Requirements and Plans are provided in Additional Resources, below.
Require the Contractor to document their actual waste diversion performance throughout the project. The Waste Management Plan, therefore, should also include progress reporting procedures to record actual diversion and cost corresponding to each diversion and cost estimate.
As the accepted Plan is a part of the contract document, it should be incorporated into the Contractor's Quality Control and Owner's Quality Assurance processes. Some public Owners go so far as to specify that progress payments will not be approved until updated actual diversion performance reports are submitted.
Vest title to debris and waste materials to the Contractor, and allow the Contractor to accrue the economic benefits. These include cost avoidance through reduced debris tipping expenses, revenues from salvaged and recycled materials, and cost avoidance by using materials taken from the jobsite back into the project.
4. Jobsite Waste Reduction
There are a variety of ways a Contractor can divert construction waste or demolition debris at the jobsite. The following general practices are common:
- Up to 10-12% of a project's construction waste stream can be cardboard alone. While protecting new materials is necessary, the Contractor can direct their subcontractors and suppliers to reduce extraneous packing and packing.
- Purchase materials in bulk where possible. Avoid individual packaging for volume purchases.
- Use returnable containers and packing materials
- Reuse non-returnable containers on the jobsite to the maximum extent possible. Develop one-hundred-and-one-uses for plastic barrels, buckets, and tubs.
- Give away non-returnable containers. Contact local and community organizations (schools, youth groups, community service groups, Habitat for Humanity, others similar).
Use scrap in lieu of cutting full new materials. Direct subcontractors and trades to collect and keep scrap at cutting and fabricating locations. Collect paints and liquids from almost-empty containers; avoid disposing of useable materials simply because there is not enough in one container to finish a job.
For materials that are heated, mixed, exposed to environmental conditions, or otherwise subject to spoilage, limit preparation of these materials to quantities which can be installed within their expiration times. Working in smaller batches will reduce the necessity to throw out expired or spoiled materials. Ensure volatile materials, and materials that degrade when exposed to heat, cold, or moisture are protected from spoilage and are not wasted.
Recycle damaged components, products, and materials, or disassemble them into their constituent materials for recycling.
Establish a return or buy-back arrangement with suppliers. Alternatively, unused, or used but serviceable materials and products can be sold to architectural salvage or used materials retail outlets. Donations to a non-profit outlet, such as a Habitat for Humanity (HfH) ReStore, are usually tax-deductible.
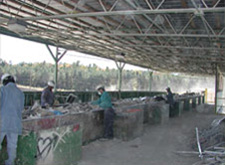
C&D recycling pick line
The Contractor may contract with a C&D recycling firm who accepts commingled debris. At the recycling site, concrete and masonry rubble are separated out of the debris for crushing into aggregate products. The remaining debris is typically crushed or shredded, then conveyed along a pick line for sorting and recycling. Recycling commingled debris and waste off-site requires virtually no adjustment in practice on the Contractor's part. C&D waste recyclers generally describe their fees as "competitive" with landfill disposal, which means a modest savings over prevailing landfill tipping fees. This method typically achieves a very high diversion rate. However, clean wood is frequently sold for boiler fuel, and some agencies do not allow incineration to be counted as diversion.
The Contractor may contract with individual recycling firms who deal in specific materials, in addition to a general waste hauler. This requires the Contractor, subcontractors and tradespersons to segregate waste, deposit it in the appropriate receptacles, and guard against contamination by other materials. The key to effective jobsite segregation is to place receptacles in the path of least resistance to the workforce, training the workforce to observe segregation practices, and policing the jobsite to prevent contamination. The construction process lends itself to on-site segregation. As trades enter and leave the jobsite, each generates a relatively homogeneous waste stream, given the specific tasks and the materials with which they work. As the recyclable materials are segregated, the recycling firms generally offer a higher price for the material (if the contractor hauls), or a lower hauling rate (if the recycler hauls). Alternatively, the Contractor can contract with a waste hauler who provides receptacles for recyclable materials and debris, and hauls all materials as a one-stop service. While some contend site separation increases the cost of construction, efficient materials movement and site layout should minimize any increased effort.
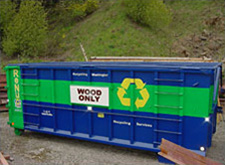
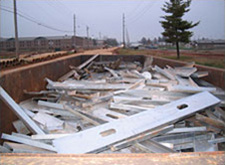
"Wood only" receptacle
"Metals only" receptacle with steel deck trimmings
- The waste diversion potential in a demolition scenario is considerable. The building's construction type and project schedule are the two primary factors in determining what and how salvage, reuse, and/or recycling can be accomplished. Consider the following:
- Develop the project schedule to accommodate salvage, reuse, or recycling. The quality and quantity of materials salvaged is a direct function to the time available for salvage.
- Prior to demolition, salvage as much useable material and components as the schedule will allow. Windows and doors, wood flooring, cabinetry, architectural millwork, electrical fixtures, plumbing fixtures, mechanical equipment anything that can be detached and removed can be usually be salvaged and reused. When developing the C&D Waste Management Plan, identify the most accessible and valuable materials, thereby optimizing the application of resources to this task.
- Concrete and masonry materials can be recycled to produce aggregate. This may be accomplished on-site with mobile equipment, or rubble can be hauled to a permanent recycling facility. Preferences vary among demolition contractors and recyclers about whether the building should be gutted prior to demolition, leaving only concrete and reinforcing to be crushed, or demolished intact, and the debris sorted as part of the concrete crushing process. Consider how the recycled concrete aggregate (RCA) will be used, what RCA products are most useable, and how the rubble should be processed to produce these products. If aggregate materials are required for the project, on-site recycling can provide these materials at a reduced net cost. The Construction Materials Recycling Association (CMRA) can provide information on methods and service providers.
- Landscape materials and wood that is not painted with lead-based paint, treated with an arsenic-based preservative, or otherwise contaminated with a hazardous or toxic material can be shredded into mulch, composted, or chipped for boiler fuel. This can be accomplished on-site or off-site. If mulch or compost is required for the project, shredding on-site can provide these materials at a reduced net cost.
- Structural steel and metals are almost universally recycled. This should be standard practice with any demolition contractor.
- Old growth timber is a valuable material and will usually justify the time required for a more delicate removal process. Timbers are generally sold through timber brokers to be cleaned and resold for timber framing, or as feedstock for high quality architectural millwork.
- Some species of dimensional lumber can also be quite valuable. Wood framed buildings can be partially or totally deconstructed. While this is often a more labor intensive approach, cost avoidance and the value of the materials can offset initial cost. The Building Materials Reuse Association (BMRA) can provide information on deconstruction contractors and used building materials retail businesses.
- If none of the alternative salvage, reuse, or recycling options are possible, mixed demolition debris can be hauled to a C&D debris recycling facility, as described above.
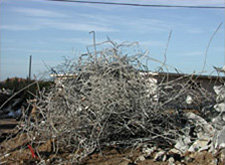
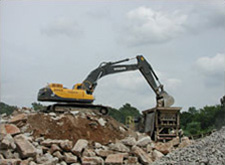
Segregated piles
Concrete recycling
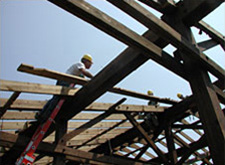
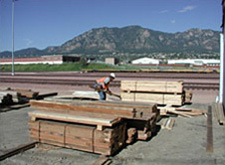
Wood building deconstruction
Salvaged lumber at the jobsite
Application
Waste reduction practices are applicable to virtually any construction and demolition project scenario. The goal is to divert materials from landfill disposal to the greatest extent practical under the circumstances.
There are two opinions about whether this is a realistic expectation under real world project conditions. One is that waste reduction costs money, and the other is that waste reduction saves money. As with any construction project, planning and project management will ultimately dictate whether waste reduction is accomplished within the established cost, schedule, and quality parameters.
The greatest uncertainty is usually the availability of salvage and recycling services and outlets, and any costs associated with handling these materials. Resources are available to help Owners, A/E and CM professionals, and Contractors familiarize themselves with the salvage, reuse, and recycling industries and infrastructure. Examples are provided in Additional Resources, below.
The following sources provide case studies, or collections of case studies, on C&D waste diversion.
- Air Force Center for Engineering and the Environment, C&D Waste Management Guide (See Appendix D for 19 case studies)
- BuildingGreen, website features articles and case studies on C&D waste management
- California Department of Resources Recycling and Recovery (CalRecycle)—Case Studies Related to C&D Diversion Ordinances
- Powell Center for Center Construction and Environment, University of Florida
- Vermont Waste Management and Prevention Division
Emerging Issues
In an era of increasing energy prices, construction and demolition waste will be more widely recognized as a recoverable resource. Technology and attendant regulations may promote improvements in the diversion of wastes from the landfill and increasingly toward energy generation and recycling of materials.
Organic materials such as wood and plant wastes will increasingly be recognized as important components of biofuel feedstock in the generation of so-called green power.
Building product manufacturers will continue to look for and find opportunities to reclaim their used products, and to increase and promote their use of recycled materials into new and improved products.
Industrial recycling equipment manufacturers are investing in development of improved machinery which has potential to revolutionize the efficient sorting and diversion of waste. Industrial shredders reduce physical volume and produce particles of consistent dimension, allowing efficient mechanical separation. Industrial air separation technology allows efficient segregation of materials with differing mass characteristics, thus separating small pieces of wood and plastic from metal and aggregate.
International trade and shipping will continue to present opportunities and risks for the responsible diversion, recycling, and disposal of waste.
Public attention to issues of indiscriminate dumping of wastes will continue to pressure governments to ensure compliance with environmental regulations.
Solid waste landfills in the US sited in arid regions will continue to receive significant volumes of waste generated in urban areas. Landfills located in wet regions, near waterways, and in other environmentally sensitive areas will continue to trend toward closure. Post-closure expenses for management of landfills will continue to increase, with environmental monitoring and greenhouse gas management being significant priorities. Costs for disposal in many areas may continue to increase faster than the cost of energy, creating a de facto demand for increased diversion, recycling, and reuse.
Relevant Codes and Standards
- Executive Order 13693, "Planning for Federal Sustainability in the Next Decade"
- UFC 1-200-02 High Performance and Sustainable Building Requirements
Additional Resources
The following references are intended to provide further information about the C&D Waste Management subject. This list is only a sampling of available information.
WBDG
Design Objectives
Sustainable—Optimize Building Space and Material Use
Project Management
Project Planning, Delivery and Controls
Tools
Construction Waste Management Database, Building for Environmental and Economic Sustainability (BEES)
Federal Regulations
- Canadian Environmental Protection Act, 1999 (CEPA 1999), Environment and Climate Change Canada
Unified Facilities Guide Specifications (UFGS)
- UFGS 01 57 19 Temporary Environmental Controls
- UFGS 01 74 19 Construction Waste Management and Disposal
- UFGS 02 41 00 [Demolition] [and] [Deconstruction]
Army Corps of Engineers Engineering and Construction Bulletin (ECB)
Army Public Works Technical Bulletins (PWTB)
- PWTB 200-1-17 Recycling Interior Finish Materials - Carpet and Ceiling Tiles
- PWTB 200-1-23 Guidance for the Reduction of Demolition Waste Through Reuse and Recycling
- PWTB 200-1-24 Quantifying Waste Generated From Building Remodeling
- PWTB 200-1-26 Market Valuation of Demolition Salvage Materials
- PWTB 200-1-27 Reuse of Concrete Materials From Building Demolition
- PWTB 200-1-40 Characterizing Demolition Debris for Diversion Opportunities: WWII-Era and Korean War-Era Buildings
- PWTB 200-1-44 Recycling Exterior Building Finish Materials
- PWTB 200-1-45 Deconstruction of WWII-Era Wood Framed Buildings
- PWTB 200-1-48 Opportunities for Reducing Construction and Demolition Waste from Residential Communities Initiative (RCI) Programs
- PWTB 200-1-73 Reuse of Materials from Modular Relocatable Facilities
- PWTB 420-49-30 Alternatives to Demolition for Facility Reduction
Construction and Demolition Waste Management Information
- Characterization of Building-Related Construction and Demolition Debris in the United States, U.S. Environmental Protection Agency, Municipal and Industrial Solid Waste Division. Office of Solid Waste, Report No. EPA 530-R-98-010
- Construction and Demolition Recycling, King County Washington, Solid Waste Division
- Construction & Demolition Recycling Magazine
- Cradle to Cradle: Re-making the Way We Make Things by William McDonough & Michael Braungart. New York, NY: North Point Press, 2002.
- North Carolina Department of Environmental Quality
- "A Report on the Feasibility of Deconstruction: An Investigation of Deconstruction Activity in Four Cities" by U.S. Department of Housing and Urban Development
- Seattle Public Utilities: Construction and Demolition Waste Management
- Sustainable Managment of Construction and Demolition (C&D) Materials, U.S. EPA
- WasteCap—Construction & Demolition Waste Diversion
Environmental Life Cycle Information
- The American Institute of Architects The Environmental Resource Guide
- Impact Estimator for Buildings, Athena Sustainable Materials Institute
- International Council for Research and Innovation in Building and Construction
- Building for Environmental and Economic Sustainability (BEES), National Institute of Standards and Technology (NIST)
- Waste Reduction Model (WARM), U.S. EPA
Hazards
- U.S. EPA
Selected C&D Waste Management Guides
- C&D Guide Air Force Center for Engineering and the Environment
- CalRecycle Construction and Demolition Debris Recycling—Specifications
- A Guide to Deconstruction Deconstruction Institute
- 2007 King County/Seattle Contractors Guide King County, Washington
- King County Washington Design Specifications & Waste Management Plans
- Recycling Construction and Demolition Wastes: A Guide for Architects and Contractors, Massachusetts Department of Environmental Protection / Boston Society of Architects
- Minimizing Construction & Demolition Waste , State of Hawaii
- WasteSpec - Model Specifications for Construction Waste Reduction, Reuse, and Recycling , Triangle J Council of Governments, North Carolina
Building Materials Exchanges
- Build Reuse
- Directory of Wood Framed Building Deconstruction and Reused Building Materials Companies , U.S. Department of Agriculture, Forest Products Laboratory
- Georgia Industrial Materials Exchange
- North Carolina Recycling Markets Directory
- Recycler's World
- Southern Waste Exchange Information (SWIX) WasteXchange
Selected State, County, and Local Agencies
- California Department of Resources Recycling and Recovery (CalRecycle)
- City of New York Construction & Demolition Waste Manual
- Construction Industry Compliance Assistance Center—C&D Debris State Resources
- King County, Washington Construction & Demolition Recycling
- North Carolina Department of Natural Resources, Division of Pollution Prevention & Environmental Assistance
- StopWaste—Construction and Demolition Debris Alameda County, California
Recycling and Waste Management Councils
- Association of State and Territorial Solid Waste Management Officials See resource links to solid waste management websites for each of the 50 states and other federal resources
- Carpet America Recovery Effort
- Environmental Sustainability Resource Center
- National Recycling Coalition, Inc.
- Northeast Recycling Council
Associations
- American Industrial Hygiene Association
- ACGIH—American Council of Governmental Industrial Hygenists
- Build Reuse
- Construction & Demolition Recycling Association
- National Demolition Association
- Solid Waste Association of North America
Training and Certification Programs
- National Demolition Association Education & Events
- SWANA Certification: Managing Construction & Demolition Materials
Organizations
- Build Reuse
- Carpet America Recovery Effort
- Construction & Demolition Recycling Association
- Deconstruction & Reuse Network
- greenGoat
- Habitat for Humanity ReStore network
- The Loading Dock
- Reuse Development Organization
Tools
- WasteCap TRACE online C&D project documentation system, WasteCap Resource Solutions
Miscellaneous References
- Application of Updated Construction and Demolition Waste Reduction Policy to Army Projects , ERDC/CERL SR-15-1, December 2015.
- Concepts for Reuse and Recycling of Construction and Demolition Waste , ERDC/CERL TR-97/58, June 1999.
- Investigation of Mechanical Processes for Removing Lead Based Paint from Wood Siding , ERDC/CERL TR-06-30, September 2006.
- LBP Concerns in Producing Recycled Concrete Aggregate from Former Fort Ord Family Housing , ERDC/CERL TR-07-2, January 2007.
- On the Road to Reuse: Residential Demolition Bid Specification Development Tool, Report by EPA Region 5
- Regulatory and Policy Issues for Reuse and Remanufacture of Wood Materials Coated With Lead-Based Paint , Technical Report by USDA Forest Products Laboratory
- System Chemistry To Control Potential Environmental and Safety Hazards of Recycled Concrete Aggregate with Lead-Based Paint , ERDC/CERL TR-10-1, January 2010.