Within This Page
Introduction
The home's enclosure separates the living environment from the outside environment in order to provide protection from the weather, intruders, pests, noise, and dirt, to control the entry of sunlight, and, most important, to maintain comfort. The enclosure of a home includes part or all of the structure that holds up and forms the roof and that resists lateral loads from wind or earthquakes. A durable and effective enclosure is a key element in a green home, because all that goes on within the home depends on its proper functioning.
Description
The enclosure is subdivided as follows:
- Foundations
- Walls and floors
- Wall cladding/exterior surfaces
- Water-resistive barriers
- Roofs
- Insulation and air barriers
- Windows
In a typical one-story home on a concrete slab, the enclosure includes the slab, the exterior walls, and the roof structure. If the wall structure is concrete or masonry, it is likely to be covered with stucco or brick on the exterior, with insulation and gypsum board on the inside.
If the wall structure is framed, the framing can be either wood or steel. Framed homes are most often insulated in the cavity between the 2 x 4 (or 2 x 6 where greater insulation is required) framing members. In steel-framed homes (and even in wood-framed homes), it is best practice to include an additional layer of continuous insulation either inside or, more commonly, outside the framing to provide a thermal break at the framing members. The outside surface will be cladding (brick, stone, wood, wood composites, fiber cement, etc.) along with an air barrier and water-resistant barrier such as asphalt paper, housewrap, fluid applied membranes, self-adhered membrane, closed-cell cellular plastic boards or other such materials. Wood-framed homes are typically sheathed with wood structural panels (OSB or plywood) to provide resistance to wind and seismic loads. In climates requiring heating, the inside surface is typically gypsum wallboard possibly with a vapor retarder installed directly to the studs (though an interior vapor retarder should be avoided in hot, humid climates).
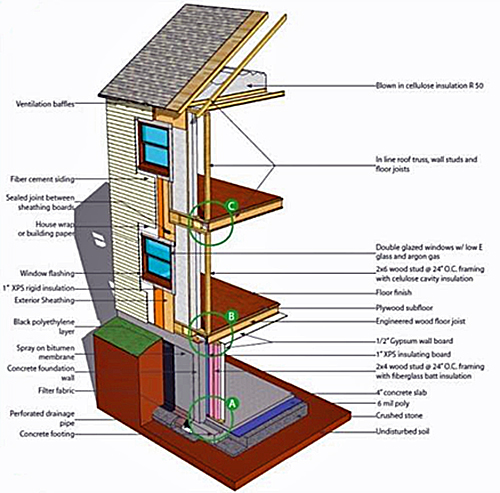
Figure 1: Components of a Building Enclosure
In a typical two-story home with a basement or crawlspace, the enclosure includes the foundation walls and the edges of the floor structures, in addition to the walls and roof. At the roof, the weather-protective roofing and the attic insulation that provides the thermal barrier are separate from each other. In some cases, the roof insulation occurs directly under the roof, creating a cathedral ceiling over usable space, or "cathedralized" when insulation is placed at roof level in a trussed roof.
Building Science in Transition
Building science is crucial in understanding how homes work. Long-held theories and ideas are being challenged, and accurate data is flowing in from well-instrumented test sites and from field monitoring of new and existing homes. Building scientists seldom disagree about the facts. Though controversy does arise over how much emphasis to give each of the many factors that influence the behavior of building elements.
Building science is now challenging some of the old methods for construction. In some jurisdictions, the building code requirements are outdated and go against building science principals. In those cases, the builder is caught between doing it right (from a building science viewpoint) and doing it according to code.
Foundations
Where the frostline is relatively deep, homes are typically built on crawlspaces or basements. If a basement is not needed or desired, either a slab or crawlspace is used. Crawlspaces must be designed to allow for visual inspection, so a leak (either from inside or from outside) can be readily detected. Crawlspaces may have other advantages in colder climates, including its ability to store and release solar-generated heat, and if properly insulated below, to form an ideal substrate for radiant heating.
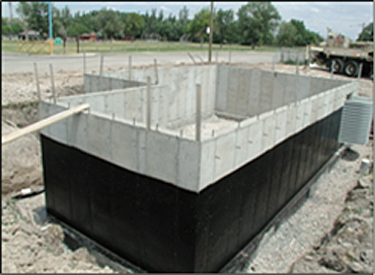
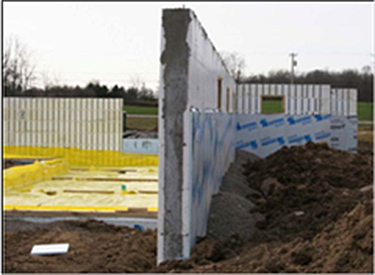
Figure 2: Foundation Preparation
Figure 3: Frost Protected Shallow Foundation
In cold climates where the frost goes deep into the ground, a builder can install a foundation by erecting the bearing walls on strip foundations independent of the slab, which can then be poured after the home is closed in. An alternative foundation for cold climates is a frost-protected shallow foundation (FPSF), where a skirting of insulation is placed around the outside of the foundation, trapping ground heat and making deep frost walls unnecessary.
If a basement is present, heating equipment and piping or ductwork are invariably located there. Heat loss from basements therefore becomes an important part of the home's energy consumption. Achieving a high rating in most Home Energy Rating programs requires that the basement walls be air sealed and insulated. One technology that automatically insulates the basement wall very effectively is insulating concrete forms (ICF), where concrete is poured into modular forms made of foam insulation.
Walls and Floors
Along with dimension lumber, there are many new and innovative engineered wood products that are finding success in traditional lumber markets. Engineered wood products are made by gluing wood veneer or strands that are graded prior to manufacturing. This results in products which are virtually defect-free with improved structural performance. For example, plywood sheathing has been replaced by oriented strand board (OSB) sheathing in nearly every part of the country.
Another alternative is steel framing, which is light in weight, straight, and unaffected by moisture (though it has higher thermal conduction issues). A third is structural masonry, poured-in-place concrete, or precast concrete. Other alternatives to conventional wall construction include structural insulated panels (SIPs), where typically a layer of expanded polystyrene (EPS) foam is sandwiched between two layers of OSB, and insulating concrete forms (ICF), where concrete is poured into EPS foam forms that stay in place to create a tightly sealed, well-insulated wall.
Floors made with I-joists or metal-plate connected trusses have many advantages in addition to their green attributes. By allowing ductwork and piping to run through them, they encourage the practice of keeping ducts and pipes inside the conditioned enclosure. To truly be effective, the rim/band joist should be air sealed and insulated.
Framing Efficiency
Efficient framing techniques require fewer materials and generate less waste during construction. Rough framing accounts for about 15% to 20% of the total cost of typical home construction. Using proven techniques to reduce the amount of framing material can lower costs, better utilize resources, and save on labor.
Optimum Value Engineering (OVE)
OVE or advanced framing uses engineering principles to minimize material usage, while meeting model building code structural performance requirements. OVE techniques include the following:
- Increasing wall stud spacing to 24 inches on-center, rather than the standard 16 inches;
- Spacing floor joists and roof rafters at 24 inches instead of 16 inches;
- Using in-line framing when floor, wall, and roof framing members are in line with one another-sometimes called "in-line" or "stack" framing (in this manner, loads are transferred directly from one bearing member to the next, thus creating a direct load path and a more efficient structure) (see Figure 4);
- Designing homes on 2-foot modules (exterior dimension), thereby reducing waste and installation labor, since most panel products come in even-incremented dimensions such as 4 x 8;
- Using two-or three-stud corner framing instead of typical corner framing, which does not allow insulation to extend into the corner. With two-stud corners, drywall clips or scrap lumber are needed to provide a surface to attach the interior gypsum wall board (see Figure 5);
- Ladder blocking at exterior wall T-intersections;
- Properly sizing headers, such as using doubled 2 x 4s, 6s, and 8s over smaller door and window openings instead of doubled 2 x 10s. In certain instances, the window header can be relocated from the exterior wall to the floor system;
- Eliminating structural headers in nonloadbearing walls.
Substitute 2 x 6 for Conventional 2 x 4 Framing
While using roughly the same amount of board-feet of lumber as 2 x 4 lumber at 16" on center, 2 x 6 framing at 24" on center leaves a larger wall cavity for increased insulation levels. Once framing crews have gained experience, these techniques can save money by using fewer pieces and being faster to assemble.
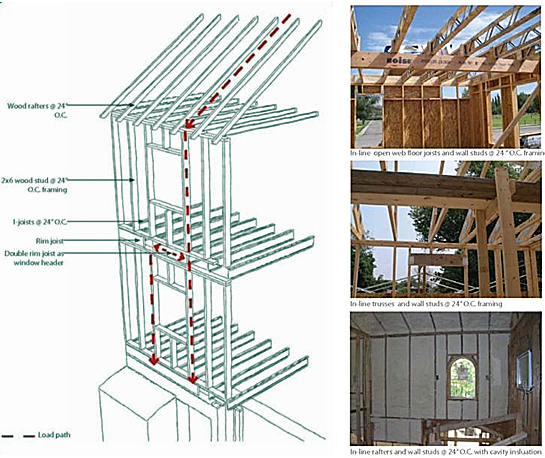
Figure 4: Schematic and Field Examples of In-Line Framing
Typical corner framing versus OVE three-stud corner framing
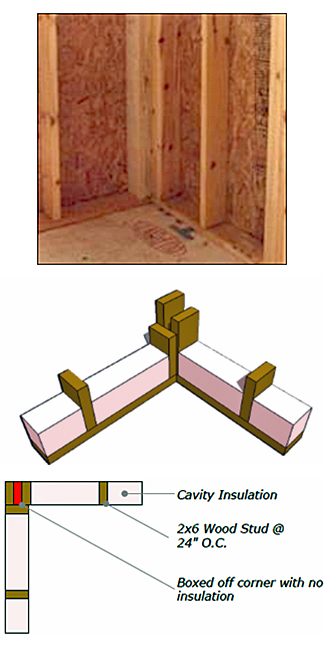
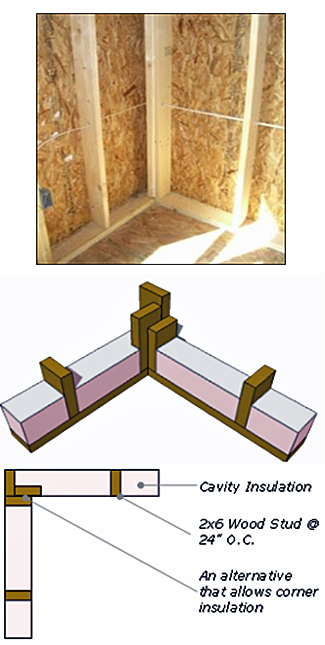
Figure 5: Corner Framing Examples
Wall Cladding/Exterior Surfaces
Wall cladding (siding, stucco, brick, etc.) needs to be combined with a water-resistive barrier to properly manage any liquid water and keep it from entering the building enclosure. Liquid water can move down (gravity) or even up (capillary action) and will enter into any crevice or hole in the cladding. Cladding systems are designed to shed most of the liquid water (bulk water) from the surface, but some liquid water will penetrate past the cladding material. A water-resistive barrier impervious to water in all ways must be installed under the cladding material. This water-resistive barrier needs to be flashed to expel the water back to the exterior. Doors and windows need special attention when flashing to ensure that all of the water is directed back to the exterior. The window itself can also leak water but by installing a "sill pan" under the window, this water can be directed to the exterior. In areas where there is a lot of rain or simply for a better performing water management system, the rainscreen principle can be used. In constructing a rainscreen wall, install the water-resistive barrier as normal, but then space the cladding system away from the surface of the wall approximately 3/8 to ½ of an inch. This can be achieved by using wood battons or other materials that are treated to resist decay. By having the cladding system spaced away from the water-resistive barrier, any liquid water that penetrates past the cladding will run down the back of the cladding system-only a very small amount will actually find its way to the surface of the water resistive barrier.
OVE ladder blocking at exterior wall T-intersection
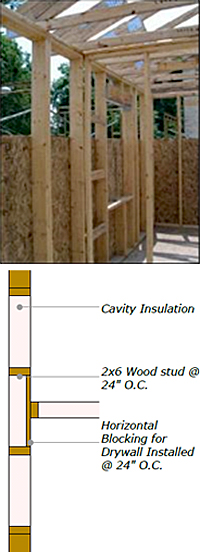
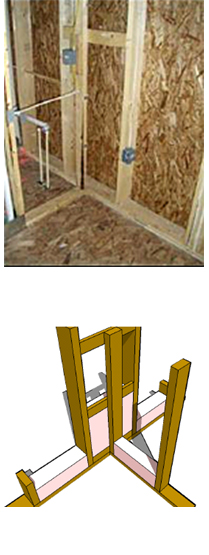
Figure 6: Ladder Blocking Example
Roofs
Whether a roof is framed or is trussed, and whether roofing is asphalt, metal, or tile, there are principles that should be followed to minimize the chances of failure leading to water intrusion. Rainwater collects in valleys, and these concentrations increase the chances for water to run up under the roofing at those locations. If valleys exist in the roof, make sure water can flow unimpeded for several feet on either side of the valley. Do not place a dormer or chimney in or near the valley, and do not place dormers close together. When there is an obstruction such as a chimney, or where a "blind" valley occurs between two parallel roofs, there needs to be a substantial cricket that directs water around the obstruction or out of the blind valley. Where an eave ends against a wall, kick-out flashing is needed to prevent water that runs down the joint between wall and roof from penetrating and running behind the siding below.
Some roof leaks are not roof leaks at all. In cold climates, warm moist air can seep out of the conditioned space into the attic and condensate as liquid or even form on the underside of the roof sheeting. In warmer weather, the frost will melt and leak into the home. The living space should be carefully air sealed from the attic or cathedral ceiling to prevent warm, humid interior air from condensing on the roof structure in cold weather. Ensure that any bathroom exhaust ventilation is ducted all the way to the exterior of the home and not simply to the attic, as this can result in wetting of the roof structure as the warm moist air will condensate as the air cools.
Where ducts are located in unconditioned attics, duct losses or gains due to not having enough insulation on the ducts or no insulation at all, and losses due to ducts leaking the conditioned air that they carry, can add significantly to energy bills. Some homes are air sealing the duct system and burying them in the insulation or moving the insulation to the underside of the roof sheeting to create a conditioned space in the attic where the ducts can be run. It is always good practice to seal all ducts whether they are in a conditioned space or not.
Trusses are widely used in home building. They have the green advantage of using small-dimension and short lengths of lumber.
Light-colored asphalt shingles or shiny, light-colored painted metal or glazed tile roofing can help reduce attic temperatures.
Insulation and Air Sealing
There are many types of insulation available to the builder. Some building systems, such as structural insulated panels (SIPs), insulating concrete forms (ICFs), and shallow frost-protected foundations (SFPF) include insulation as an integral part of the system. In the open cavities of framed walls, there are many choices.
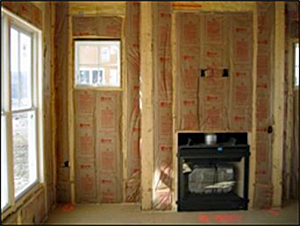
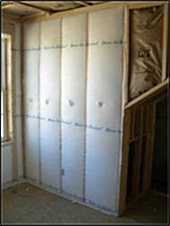
Figure 7: Examples of Fiberglass Insulation
Fiberglass Insulation
Fiberglass is manufactured by melting silica (largely sand) with other materials and spinning fine glass strands to the desired consistency. Fiberglass insulation has natural fire resistance and generally has 20-25% recycled content, including both post-industrial glass cullet and postconsumer recycled bottles. Some products contain as much as 40% recycled content. These levels meet the EPA Buying Guidelines in terms of recycled content. Fiberglass insulation is used in walls, ceilings, and cavities in the form of batts, blankets, and loose fill. Many manufacturers have certified their products to the GREENGUARD specification, and fiber glass products are available with or without formaldehyde binders. The Consumer Products Safety Commission has concluded that the amount of formaldehyde present in fiber glass is not a concern.
Cellulose Loose-Fill Insulation
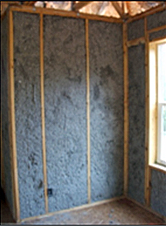
Figure 8: Cellulose Loose Fill Insulation
Cellulose insulation is made from recycled paper (primarily recovered newsprint and cardboard), that is milled to a state resembling the original paper pulp. The recycled material content of cellulose insulation is typically approximately 85%. Most of the recovered content is postconsumer. Fire retardants are added to produce performance characteristics required by ASTM standards and federal and state regulations. Like all loose-fill insulation, cellulose is labeled with both "settled thickness" and "installed thickness" columns on coverage charts. To ensure thermal performance, it is essential to follow the manufacturer's guidance for installed thickness, so that proper R-value is achieved. Loose-fill insulation can be easier to fit around pipes and other obstructions in a wall assembly. Cellulose is sometimes applied as wallspray. Care should be taken to allow for appropriate drying time based on both temperature and humidity levels prior to installation of gypsum wallboard. If not allowed to dry thoroughly before enclosing, products with added moisture may damage or support mold growth on other building materials with which they come into contact. Dry cellulose insulation can be pneumatically installed behind webbing, netting, reinforced polyethylene or gypsum board.
Mineral Wool Insulation
Mineral wool is similar to fiberglass in many respects. Mineral wool is manufactured from basalt or other minerals often in combination with slag, a byproduct from several industrial processes. When installing insulation to a high-temperature surface, mineral wool is ideal. It is also used as passive fire protection. Mineral wool comes in board, blanket and loose-fill forms. Many types of mineral wool insulation have recycled content as high as 70%. Slag wool insulation contains as much as 90% recycled blast furnace slag, some of which is reclaimed from landfills for use in insulation.
Spray Polyurethane Foam
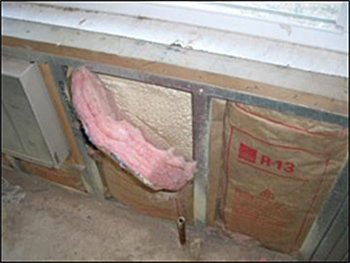
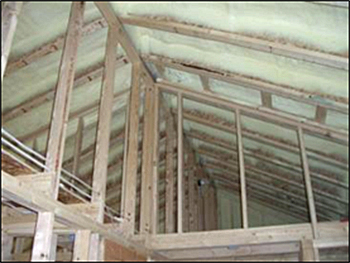
Figure 9: Examples of Spray Polyurethane Foam Insulation
Closed cell foam insulation has excellent air-sealing qualities, moisture resistance, and insulating properties. Spray polyurethane foam insulation is typically either medium-density closed cell or low-density open cell polyurethane for thermal insulation applications and high-density for roofing applications. Foam can be sprayed directly into cavities, either filling them or creating an air-sealing liner over which batts can be placed (typically referred to as "flash and batt"). However, care must be taken to prevent condensation within the wall. Foams have the advantage that they can be sprayed into overhead cavities, creating an air-sealed cocoon around the living space, and can be used to create unvented attic and cathedral ceiling spaces (according to the 2009 IRC), or to insulate roof lines that cannot be properly vented. Foams can also be sprayed directly on concrete or masonry.
Rigid Foam Board Insulation
There are three primary types of rigid foam boards used for building insulation; the use and properties are different enough to consider them separately. All products are typically available in 2'x8' or 4'x8' sheets with thicknesses of 0.5–4".
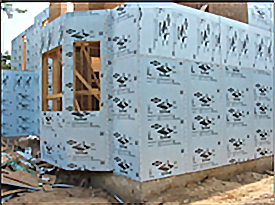
Figure 10: Example of Rigid Foam Board Insulation
Expanded Polystyrene (EPS) is a white foam board sometimes called "bead board" because of its composition; it appears to be made up of many small, compacted beads. Of the three rigid foam products, EPS has the lowest thermal resistance (R-value) and the highest moisture vapor permeability. EPS is generally provided without a facing, though polymer or foil facings are sometimes available. As with most foams, EPS cannot be left exposed indoors and must be covered with a thermal barrier.
While chemically similar to EPS, the extrusion of extruded polystyrene (XPS) results in higher thermal resistance and lower moisture vapor permeability. While EPS is nearly always white, XPS is nearly always colored; blue, pink, and green XPS boards are available from different manufacturers. XPS is commonly used on foundation walls, over exterior sheathing (as additional insulation to the cavity insulation or as the only insulation), and in some ICF systems. As with EPS, typically XPS cannot be left exposed indoors and must be covered with a thermal barrier.
Unlike EPS and XPS, polyisocyanurate (polyiso) foam boards are almost always faced on both sides with polymer and/or foil. This facing makes polyiso boards almost impervious to moisture vapor diffusion—a consideration when deciding on an insulation strategy.
Exposed or Unexposed?
When installing insulation materials in occupied or unoccupied spaces, be aware of the building code requirements for flame spread and smoke-developed indices. These code requirements will dictate whether materials such as vapor retarders and insulation can be left exposed or must be covered by a fire-resistive barrier, or an "ignition" barrier in the case of an unvented attic where access is required for service if HVAC equipment is located within this space. Often this information is provided in the ICC Evaluation Service (ICC-ES) report for the insulation material being specified.
Vapor Retarders
Humidity in the air can move through ordinary building materials by a process called vapor diffusion. In the past 50 years, a strong emphasis on vapor diffusion as a source of moisture problems in walls, attics, and cathedral ceilings has led to the almost universal requirement for a strongly effective vapor retarder. Recently, however, this emphasis has been re-examined in light of condensation problems in air-conditioned homes in hot and humid climates, where an interior vapor retarder contributes to the moisture problems rather than solving them.
In cold climates, it is generally safe to wrap the inside of a home that is not air-conditioned with most types of "vapor retarders." The preferred strategy for an air-conditioned home in a cold climate is to caulk every leakage path and use a moderately effective vapor retarder, such as the kraft paper facing on batt insulation or a vapor retarder paint (primer).
In hot and humid climates, it is essential to avoid any sort of vapor retarder on the inside surface (including vinyl wallpaper) to reduce condensation potential so that when the wall or ceiling gets wet, it can dry out to the air-conditioned interior.
Air and water leakage, not diffusion, are the primary causes of moisture damage in walls and attics. Once air leakage is controlled by air sealing and water leakage is controlled by proper water management techniques, the vapor retarder can be chosen to suit a specific climate. Look for climate-specific improvements in the vapor retarder requirements of the national model codes, starting with the 2009 International Residential Code (IRC).
Moisture Control Techniques
Careful attention to water movement (foundation drainage systems, house perimeter grading, and flashing details) and vapor movement (air sealing details and vapor barrier systems) can go a long way toward controlling moisture and possible mold problems in homes. The following is a list of general techniques to help control moisture:
4" (or more) crushed stone and 6+ mil polyethylene vapor barrier below the slab will provide a capillary break to prevent moisture from wicking up through the slab.
Install a capillary moisture break between the top of the footing and the foundation wall (or under a footing that is integral with the slab).
Learn where seasonal high ground water occurs, and do not build basement slabs, floor slabs, or crawlspace floors less than 1 foot above high groundwater or a sump pump may need to be installed. This system should include back-up power and a solid sealed lid.
Around the foundation wall exterior, install crushed stone and a 4" (or larger) perforated drainage pipe with a filter fabric next to the footer to divert water away from the foundation during rain events. In poorly draining soils, a sheet drainage material (e.g. black polyethylene) can be used over the exterior insulation to enhance the movement of water to the foundation drain and reduce hydrostatic pressure against the outside of the wall.
Footing drains should drain to daylight, a drywell, or a sump pump.
Exterior surface of foundations should be water-proof (commonly urethanes, modified asphalts, clay based, or rubber based) and not simply damp-proof (generally asphalt or tar based compounds).
Soils with significant clay or organic matter will retain water for extended periods. If these conditions are present, additional drainage measures may be necessary.
Moisture laden air leakage into the basement can result in condensation issues, so it is recommended that the rim/band joist and sill plate are air sealed with a closed cell spray foam application of at least 2".
Regardless of how well a basement is constructed; a dehumidifier may be needed to maintain a dry basement (especially in the first two years after construction).
Use "rainscreens" with cladding in all cases.
Direct any downspout discharge well away from the foundation. Rain gutters should run at least 3' from the house perimeter (refer to the 2012 International Residential Code Section R801.3). Regularly clean gutters to allow roof run-off to be directed away from foundation.
Slope grade away from foundation a minimum of 6 inches in the first 10 feet. Backfill may settle over the first couple years. Regrade exterior landscaping as required to maintain drainage away from foundation.
Use kickout flashing where an eave runs into a sidewall.
Avoid valleys and keep chimneys, dormers, and skylights away from valleys.
Use crickets where water might not flow easily off the roof.
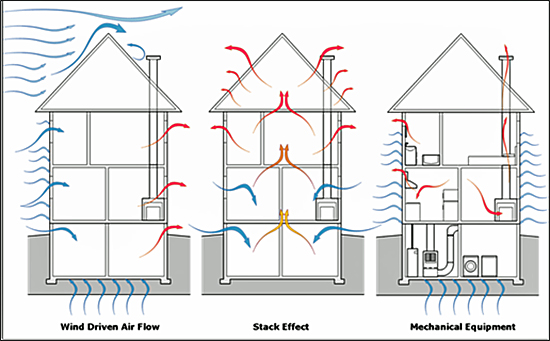
Figure 11: Air-Flow in Buildings Copyright Steven Winter Associates, Inc. 2011
Air Leakage Driving Forces
Requirements for air leakage to occur are:
- Holes, cracks, gaps, seams, and penetrations. The larger the hole, the greater the air leakage. Large holes have higher priority for air sealing efforts.
- Driving force. A pressure difference that allows air to flow through a hole. Holes that experience stronger and more continuous driving forces have higher priority.
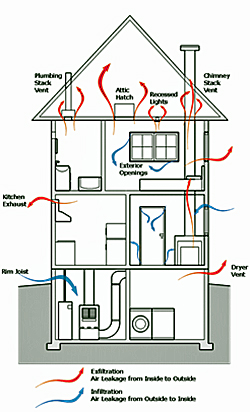
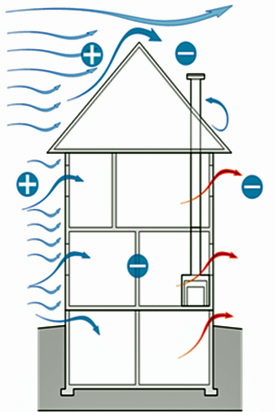
Figure 12: Infiltration and Exfiltration Copyright Steven Winter Associates, Inc. 2011
Figure 13: Wind Pressure in Buildings Copyright Steven Winter Associates, Inc. 2011
The common driving forces are:
- Wind. Caused by weather conditions.
- Stack effect. Upward air pressure due to the buoyancy of air.
- Mechanical blower. Induced pressure imbalances caused by operation of fans and blowers.
Wind is usually considered to be the primary driving force for air leakage, but, in most locations, wind is intermittent and relatively minor. When wind blows against a building, it creates a high pressure zone on the windward side. Outdoor air from the windward side infiltrates into the building, while air exits (exfiltrates) on the leeward side. Wind creates areas of differential pressure, which cause both infiltration and exfiltration. The degree to which wind contributes to air leakage depends on its velocity and duration.
The temperature difference between inside and outside causes warm air inside the home to rise, creating a driving force known as the stack effect. In the winter, cold air is drawn in at the bottom of the structure to replace the warm air that escapes near the top. In homes with large holes in the attic and crawlspace or basement (or even chimneys), the stack effect can be a major contributor to air leakage, moisture and air quality problems. In the summer, the opposite can occur.
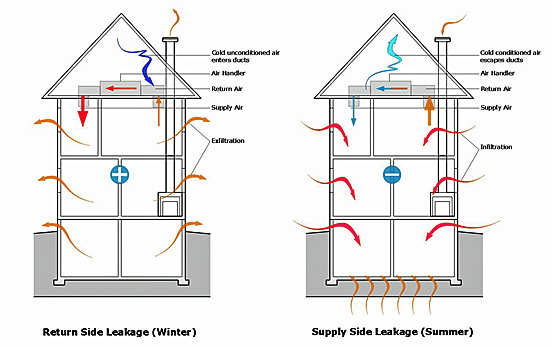
Figure 14: Seasonal Leakage Copyright Steven Winter Associates, Inc. 2011
Poorly designed and installed forced-air systems can create strong pressure imbalances inside the home whenever the heating and cooling system operates. In addition, unsealed ductwork located in attics and crawlspaces can draw pollutants and excess moisture into the home. Correcting duct leakage problems is critical when constructing an energy-efficient home.
Air Leakage Control
This is a brief overview of the many air leakage issues that arise when constructing an energy-efficient house. Sealing the house carefully to reduce air leakage is even more important than adding insulation. Consider the following:
Ensure that a complete air barrier system has been installed on all six sides of the home and that it is continuous and air-tight.
Make sure all wall cavities are well sealed to minimize air leakage prior to installing cavity insulation.
When using sealants to create the air barrier system, be certain to use sealants that are adequately flexible and can bridge the gap. Larger openings should be sealed with rigid air impermeable materials, using caulk or foam around the perimeter.
Ensure the most common sources (floor-wall junctions [sillplates], wall outlets, windows and window openings, HVAC ducts, fireplaces, recessed lighting fixtures, and exterior venting devices for bathrooms, kitchens and laundry rooms) are airtight. Careful sealing of these areas will reduce air leakage and control moisture.
Most of the largest leaks in homes occur where framing (such as floor joists or wall studs) span from an area inside conditioned space to an unconditioned or vented space, such as the attic, garage, or roof. Appropriate blocking is needed in these instances.
Installing house wrap as an air barrier material over the exterior sheathing can reduce air leakage and moisture penetration. Tape all seams and seal and/or tape penetrations such as windows, doors, and vents.
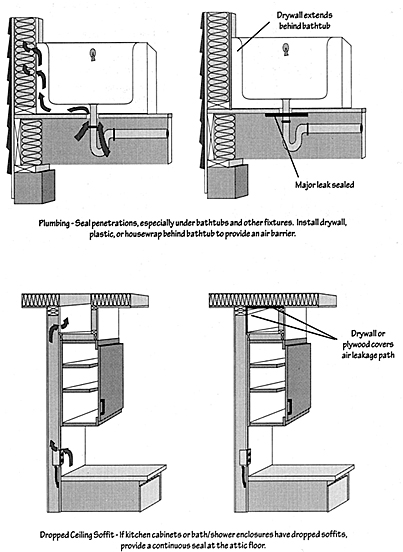
Figure 15: Sealing Bypasses
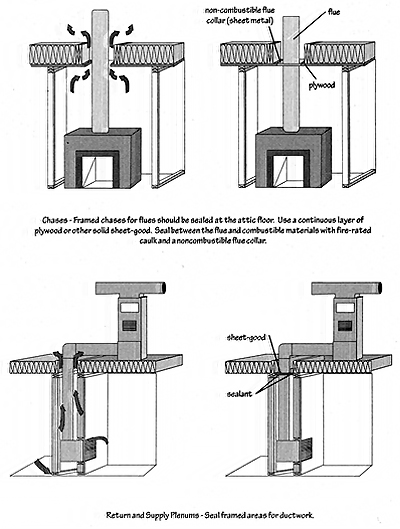
Figure 16: Sealing Bypasses for Flues and Ducts
Windows
Windows play an important role in creating an energy-efficient enclosure. How they are installed and flashed is crucial to maintaining the moisture integrity of the exterior walls.
Flashing around windows should carefully overlap the upper layer over the lower one in all cases. Do not rely upon window flanges set in sealant to keep water out, and use sill pans whenever possible.
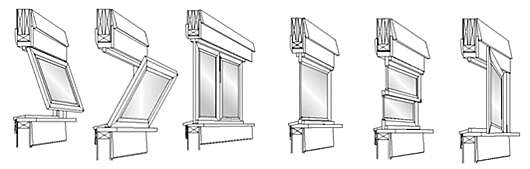
Figure 17: Examples of Window Types
Window Upgrades for Existing Buildings
There are many high-performance fenestration products on the market, yet no one product is the best choice for all climate conditions. For example, low-e coatings are what are being marketed for energy-efficient windows. Low-e coatings provide a lower solar heat gain coefficient, so they restrict the amount of solar heat gain that enters the living space. In cooling-dominated climates, low-e coatings are desirable because they will help lower the cooling demand of the building. In heating-dominated climates, select gas-filled windows with low-e coatings to reduce heat loss. Depending on what surface of the window panes the low-e coating is located on, it can actually assist in keeping heat in the space during the winter, rather than restricting it from entering.
The Efficient Windows Collaborative provides a tool to help consumers choose the best replacement windows depending on their climate or to meet their unique tastes and preferences. This window selection tool is available here.
Make sure to properly air seal between the rough opening of the window and the window frame when installing replacement windows. Using low-expansion sealant is recommended. This air sealing, along with the enhanced windows, will often address common homeowner comfort complaints of drafty windows and window condensation.
High-Performance Windows and Utility Bills
High-performance windows, doors, and skylights can reduce energy bills while helping protect the environment. Achieving a full return on investment on a given retrofit tends to be realized incrementally over time.
Window Films, Energy Efficiency, and Comfort
One alternative to retrofitting windows is using window films. Such film is a self-adhesive transparent material that is applied directly to glass and the glazing systems of existing buildings. This application typically reduces the SHGC without changing the window or building structure. However, it may not significantly impact the window's U-factor. In some cases, window films can reflect approximately 75 to 80 percent of solar heat, which leads to savings on energy costs. Window films can also reduce heat loss from a building by reflecting the heat back into the building. In addition to contributing to energy efficiency, window films also improve occupant comfort. Finally, window films can help reduce the fading and color changes in fabrics, artwork, and furniture due to ultraviolet light.
Recent High-Performance Developments for Windows
Many windows of yesteryear have nothing more than air between their panes. The most energy-efficient windows, however, have inert gas such as argon or krypton between their panes. It is important to note that while these gases are harmless, they are effective for minimizing heat transfer. They accomplish this by slowing the exchange of energy between molecules. Air as a gas is fairly reactive and exchanges energy naturally with itself and its surroundings, but inert gases resist such changes.
Key Considerations Regarding High-Performance Windows
When considering what kind of high-performance windows to install as part of a retrofit project, there are many factors to consider, including the life-cycle cost of the windows and the operator type. High-performance windows can even lower the cost of a new home due to the ability to install a smaller, less expensive heating and cooling system. With respect to window performance, there are two main things to consider. The first is the type of glass in the window.
Single Pane Windows
As the name implies, this kind of window is comprised of just one sheet of glass. The U-factor for a good quality single-pane window is 1.0, which means they do not provide good protection against heat gain during summer or heat loss during the winter. Because of their poor energy efficiency, single pane windows are not readily available in today's marketplace.
Multiple Pane Windows
There are double, triple, and quadruple pane windows. Each sheet of glass is separated by a gap. This gap is filled either with air or an insulating inert gas, such as argon or krypton.
Every time a sheet of glass is added to a window, the U-factor improves. This means a quadruple pane window will have better insulating properties than a double or triple pane window. This, of course, equates to greater energy savings.
The second thing to consider when choosing the right kind of high performance windows for a retrofit project is the material used to construct the window frames.
Vinyl
This is a popular option because vinyl is resistant to corrosion, swelling, and peeling. Its good insulation properties help reduce energy bills. Vinyl frames also require less maintenance and offer competitive prices. Moreover, vinyl is moldable into a variety of shapes, scratch resistant, and fits well with most structural designs.
Aluminum
Aluminum is approximately three times stronger than vinyl, and it is about twenty times stronger than wood. Aluminum tends to be more affordable than vinyl, and it can easily be repainted. Additionally, aluminum is second only to vinyl in durability, and it maintains its properties under all weather conditions.
One important thing to consider about aluminum, however, is that it has poor insulating value and therefore requires the application of additional materials to improve thermal resistance and to reduce condensation. Aluminum that is exposed to the elements may also become oxidized.
Wood
Many people consider wood to be the most elegant and aesthetically appealing option among window frames. Wood offers nearly endless design options and maintains its properties under widely varying temperatures. Wood frames provide excellent insulation value, so they contribute to energy savings.
Nevertheless, wood may be more expensive than vinyl and aluminum. Wood also requires regular maintenance such as painting or staining, and protection from moisture to prevent cracking and splitting. Wood is also considerably weaker than vinyl and aluminum.
Fiberglass
Fiberglass window frames are stronger than wood and vinyl and have a lower chance of warping. One unique point about fiberglass frames is that they contribute to sustainability because they are made with approximately 60 percent glass, and glass can be recycled. It is important to note that not all fiberglass windows are necessarily made with recycled glass, but they can potentially be made with recycled glass.
The Building Enclosure—Rules of Thumb
- Consider using advanced framing to reduce framing costs, add strength to a home's enclosure, and reduce material consumption.
- Pay careful attention to water movement.
- Install a "sill pan" under all windows.
- Use the "Gap Sealing Checklist" for homes. (See page 90 of the Beyond Green™ Guidelines for High-Performance Homes, 6th Edition)
- Install an air barrier system.
- Stay abreast of rapidly changing building science and codes regarding crawlspace and roof ventilation and vapor retarders.
- Consider advanced foundation systems such as FPSFs and ICFs.
Conclusion
Many people choose new windows based on appearance, style, convenience, and price. While these may be important factors, overall performance should actually be the most important. High-performance windows typically cost more initially, but they provide greater comfort, increase home value, and save money over the long term. High-performance windows also contribute to energy cost savings because they enable consumers to install smaller, less expensive heating and cooling systems that can be adjusted periodically throughout the day. Consumers should expect to realize the return on investment of a window retrofit project over time—15 to 20 years—rather than expecting their utility bills to decrease dramatically in the short term.
Additional Resources
Web Resources
- Building America Solution Center Resources
- Cellulose Insulation Manufacturers Association
- EPS Industry Alliance—Insulated Concrete Forms
- Greenguard Environmental Institute
- Insulation Institute (NAIMA)
- NAHB HomeInnovation Research Labs™
- National Fenestration Ratings Council, web site provides a standard industry rating for use by manufacturers. Helpful window selection information is also available.
- Portland Cement Association information on concrete and sustainability and concrete homes
- U.S. Department of Energy: Efficient Windows Collaborative
- U.S. Department of Energy: Office of Energy-Efficiency and Renewable Energy