Introduction
Within This Page
Accounting for as much as 80 percent of a building's life-cycle costs, operation and maintenance expenses often reach three times a building's initial construction costs. But what if those costs could be alleviated - and performance optimized - by encouraging facility professionals to provide input during the design phase of the project? This resource page presents a methodology that links operations and maintenance goals to the design process, and how it can be applied to any organization.
Description
There are numerous costs associated with acquiring, operating, maintaining, and disposing of a building or building system. Building-related costs usually fall into the following categories:
- Initial Costs-Purchase, Acquisition, and Construction Costs
- Utility Costs - Water, Electric, Natural Gas, etc.
- Operation, Maintenance, and Repair Costs
- Demolition and Disposal Costs
- Replacement and Refurbishment Costs
- Residual Values-Resale or Salvage Values or Disposal Costs
- Finance Charges-Loan Interest Payments
- Environmental and/or Remediation Costs
Of these, Operation, Maintenance, and Repair Costs are greater than three times the cost of initial construction. Relatively speaking, studies show that these costs equate to sixty to eighty percent of a building's life-cycle costs. Having such a profound impact on a building's financial outlay, it is very important that operations and maintenance considerations be discussed at the beginning of any construction activity to optimize the life-cycle of a building. With that being said, maintainability is a subject that should be thoroughly explored, not only in the construction and operations phase of a project, but also in the feasibility, planning and design phases of such projects as well.
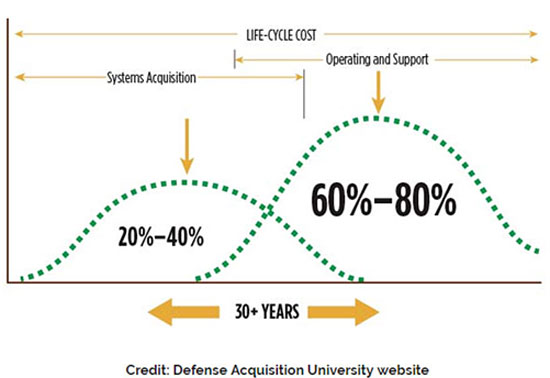
Studies show that operation and maintenance (O&M) costs are greater than three times the cost of initial construction and that O&M costs can equate to 60% to 80% of all life cycle costs.
Maintainability is considered, inherent to the building system design, ensuring the ease, accuracy, safety, and economy of maintenance tasks within that system. The purpose of maintainability is to improve effectiveness and efficiency of maintenance. One of the major products desired of such an activity is the optimization of building life—cycle costs. Design for Maintainability (DfM) is the first step of an effective maintenance program, linking maintenance goals to the design process.
Design for Maintainability emphasizes the importance of timely integration of design and construction knowledge with operations and maintenance (O&M) experiences into project designs at an early stage. Implementing DfM decreases the risk of equipment reliability and uptime being impacted and total life-cycle costs increasing significantly.
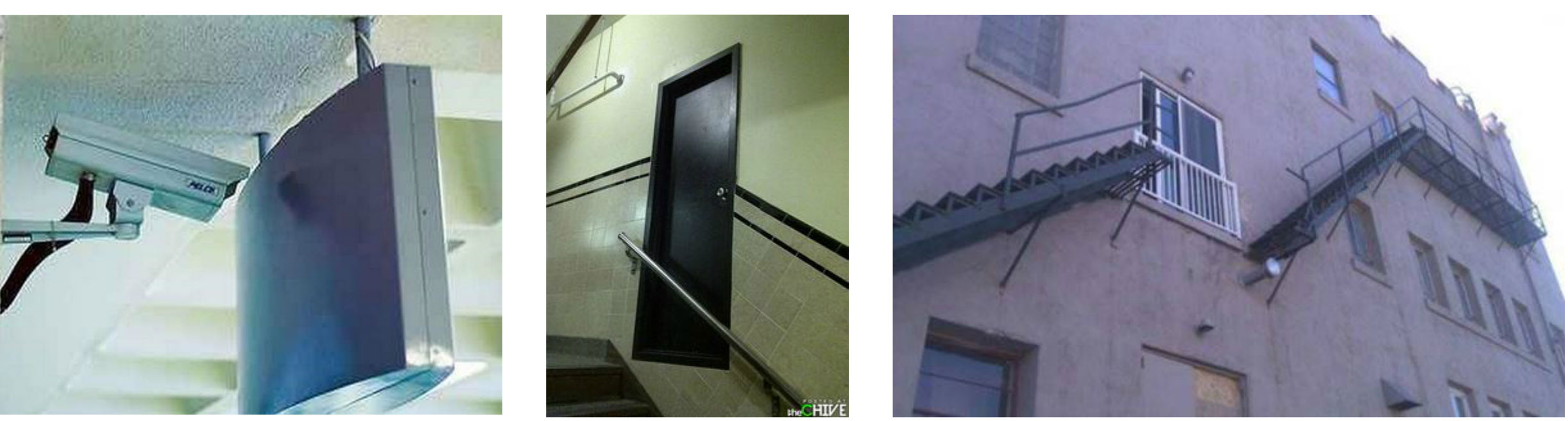
Unsuccessful examples of facility design installations.
Two basic approaches are available to implement design for maintainability, the stand-alone process and the combined process. The stand-alone maintainability process is specifically focused on achieving project maintainability goals. Resources and procedures are dedicated solely to implementing appropriate levels of maintainability on the project. However, using the combined maintainability process, maintainability implementation is combined with other project improvement initiatives such as reliability improvement, constructability, value engineering, or process hazard analysis.
The following specifics are included in both of the two approaches to DfM:
- Standard Design Practice — Maintainability is accomplished through designed–in features such as equipment accessibility, standardization, modularization, ease of maintenance, etc.
- Contract Specifications — Effective specifications include maintainability objectives, thorough operation and maintenance documentation and training needs, and maintenance management system requirements.
- Cross–Functional Involvement — Input from maintenance personnel is incorporated into the maintainability planning and design of the project.
- Pilot Maintainability Program — Small–scale program identifies benefits and costs of maintainability that can be tested with minimal risk.
- Integration into Existing Programs — This approach identifies maintainability best practices that can be integrated into existing programs such as reliability analysis, process hazard analysis, and front–end planning with minimal cost and effort.
- Formal Maintainability Program — Developed, supported, and resources committed from the corporate level of the organization. Maintainability roles and responsibilities are clearly identified. A structured work process is provided to facilitate implementation of maintainability.
- Comprehensive Tracking — Methods exist to capture, document, archive, and share project maintainability lessons learned.
Attributes of a successful DfM program:
- Corporate Commitment — Demonstrated by setting aside resources to establish the maintainability program, development of a policy statement establishing the maintainability program, and designating a corporate–level champion to oversee the program.
- Program Supports — Demonstrated by having a dedicated corporate and project staff to implement the program and to develop written procedures, track progress, and develop and maintain a maintainability lessons learned database.
- Maintainability Planning — Demonstrated by work processes that review lessons learned, establish project maintainability objectives, and activity and resource planning to integrate maintainability into the project.
- Maintainability Implementation — Demonstrated by project cross functional teams including maintenance staff, project meetings dedicated to maintainability, and specific project design reviews for maintainability.
- Program Updating — Demonstrated by continuous program evaluation, updated maintainability lessons learned, and integration of innovative maintenance technologies into the project design.
There must be a commitment to implementing a robust Design for Maintainability program. This commitment is supported by developing management awareness of maintainability, performing a self-assessment and identifying barriers, recognizing the benefits, and developing an implementation plan. In establishing a Design for Maintainability program, several things are integral. Identifying a corporate maintainability champion, developing corporate procedures and staff, and developing a lessons learned database are key building blocks. In establishing DfM, most entities question whether or not this is possible. To answer this in the affirmative, consider the following:
- Who is responsible for maintainability at the project level?
- How will the project team be oriented to the DfM process?
- How will project maintainability reviews be conducted on an ongoing basis?
Implementing a Design for Maintainability program is supported by forming cross-functional teams, defining maintenance strategies project maintainability objectives, and integrating appropriate maintenance technology where applicable. It's also supported by conducting formal maintainability meetings, applying maintainability concepts in design and procurement, recognizing construction impact on maintainability, monitoring and evaluating program effectiveness, and conducting maintenance training and providing documentation. In the vein of continuous improvement, the Design for Maintainability program is a living organism. It must be subject to updates supported by evaluating the corporate program effectiveness, revising program organization and procedures, and updating the lessons learned database.
In summary, Design for Maintainability allows for the discussion and resolution of operations and maintenance considerations up front. It takes commitment and discipline to engage and implement such a methodology; however, the benefits to the overall life cycle of a building produce a good business case, and yield a high return on investment, not only in overall costs, but also improved morale through increased efficiency of labor. The impetus for such an initiative only proves to optimize operations and maintenance activity for the built environment.
Additional Resources
Publications
Construction Industry Institute
- CII 142-1 Design for Maintainability Research Summary
- CII 142-2 Implementation Resource: Design for Maintainability Guidebook
- CII 142-11 A Model Process for Maintainability Implenmentation
National Institute of Building Sciences Facility Maintenance and Operations Committee