Introduction
Within This Page
Today's architects are faced with the urgent task of achieving energy-efficient and high-performance building enclosures. Structural Insulated Panels are an option for part of the enclosure assembly that can help achieve these goals. SIPs do an impressive job of slowing down the transfer of heat, air, and vapor through the assembly. They also dramatically reduce the drying potential of the enclosure, lessening its ability to recover from inadvertent water intrusion. Such an airtight assembly with great thermal resistance can result in a high-performance and durable enclosure if detailed and built correctly, or it can result in the rapid rot and decay of a building's primary structure if detailed or built incorrectly. Reference Building Science Corporation's Building Science Insight BSI-028: Energy Flow Across Enclosures.
History
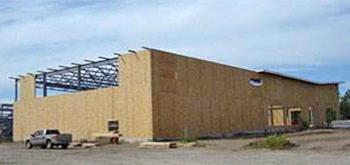
Figure 1: Example of SIPs used as infill with a structural steel frame, Silvis School, Illinois. Photo Credit: Steven Schaefer Associates, Inc. Consulting Structural Engineers
The Forest Products Laboratory in Madison, Wisconsin introduced the idea of what is now known as Structural Insulated Panels (SIPs) in 1935. The Laboratory's prototype panels consisted of framing members, plywood and hardboard sheathing, and insulation. These initial panels were used to build test homes that were disassembled and tested after thirty years to reveal that the panels retained their initial strength values. Frank Lloyd Wright used a form of structural insulated panels in the Usonian homes built in the 1930's and 1940's. In 1952, Alden B. Dow created the first foam core SIPs which were being mass-produced by the 1960's. (Morley)
Today, SIPs are prefabricated building components for use as walls, floors, roofs, and foundations. SIPs provide a continuous air and vapor barrier as well as increased R-value when compared to traditional construction. Construction costs associated with SIPs are comparable to more conventional building methods when savings associated with labor costs, material waste, and energy efficiency are considered. (Morley)
Description
Structural insulated panels are composed of an insulated foam core between two rigid board sheathing materials. The foam core is generally one of the following: expanded polystyrene (EPS), extruded polystyrene (XPS), and polyurethane foam (PUR). With EPS and XPS foam, the assembly is pressure laminated together. With PUR and PIR, the liquid foam is injected and cured under high pressure.
The most common sheathing boards are oriented strand boards (OSB). Other sheathing materials include: sheet metal, plywood, fiber-cement siding, magnesium-oxide board, fiberglass mat gypsum sheathing, and composite structural siding panels.
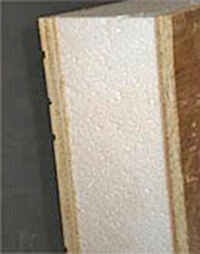
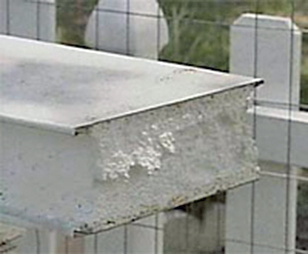
Figure 2: Typical SIP with OSB and EPS. Source: www. housing.com
Figure 3: Sheet Metal SIP. Source: www. steelsipconstruction.com
Each sheathing material and foam type has its benefits and drawbacks. The type of SIPs selected depends upon the building type and site conditions. The following tables outline the benefits and drawbacks of the most common sheathing and foam types.
Table 1: Sheathing Type Chart
Sheathing Type | Benefits | Drawbacks |
---|---|---|
Oriented Strand Board (OSB) | Load bearing; readily available; tested; large panel size up to 8' x 24' | Subject to mold and a reduction in structural capacity if exposed to moisture; not fire resistant; must be treated for termites; difficult substrate for most common joint tapes |
Sheet Metal | Reistant to mold; can be load-bearing; very light; unlimited lengths when made from coil stock | Must be galvanized or stainless steel; not load bearing |
Plywood | Lateral strength | Availability; price; limited panel size; subject to mold and reduced structural capacity if exposed to moisture for a prolonged period of time; not fire resistant; must be treated for termites |
Fiber Cement Siding | Resistant to mold, termites, and fire | Availability; weight; testing; limited panel size |
Magnesium Board | Resistant to mold, termites, and fire | Availability; testing; limited panel size |
Fiberglass Mat Gypsum Sheathing | Resistant to termites and fire | Not structural; limited panel size |
Composite Structural Siding Panels | Resistant to mold and termites; pre-primed materials available | Not fire resistant |
Table 2: Core Type Chart
Foam Core | Benefits | Drawbacks |
---|---|---|
Expanded Polystyrene (EPS) | Least expensive; thickness options are only limited by the foam manufacturer; availability; fastest to modify in field; most benign blowing agent | Produced with HBCD* |
Extruded Polystyrene (XPS) | Strength; water resistant | Availability; produced with HBCD* |
Polyurethane Foam (PUR) | Highest R-value/inch; strength, water resistant | Most expensive; harder to modify thickness limitations; creep; availability; produced with chlorinated phosphate flame retardants** |
*HBCD: hexabromocyclododecane - a brominated fire retardant classified by the European Union (REACH program) as persistant, bioaccumulative, and toxic (PBT). **Not as hazardous as most brominated flame retardants, but health and environmental concerns still exist. Source: BuildingGreen Insulation Report
Table 3: Foam Technical Data
Foam Type* | EPS Foam | XPS Foam | PUR Foam |
---|---|---|---|
Density in Panel (lb/ft3) | 0.90 | 1.5 | 2.3 – 2.5 |
Compressive Strength @ 10% deformation (psi) | 10 | 20 | 35 |
R-value/in @ 75° F | 3.6 | 5.0 | 6.54 |
Permeance per inch | 5 | 1.1 | 2.00 |
Common Fire Retardant | HBCD | HBCD | TCPP |
Common Fire Rating Class | 1 | 1 | 1 |
Common Blowing Agent | Pentane | HFC—134a | HFC—245fa |
* Most SIP manufacturers use a 0.95 minimum density.
Fundamentals
Structural Design and Construction
SIPs behave similarly to a wide flange steel column in that the foam core acts as the web and the sheathing responds as the flanges. Under axial loads, the sheathing responds similarly to a slender column, and the foam core acts as continuous bracing preventing the panels from buckling. Just as wide flange sections increase in strength with increased depth, thicker cores result in stronger panels in compression and bending. (Morley)
SIPs are designed to resist not only axial loads, but also shear loads and out of plane flexural loads. The panels' ability to resist bi-axial bending and lateral shear allow them to be used as roofs and floors. SIPs panels are acceptable to use as shear walls in all seismic design categories. A structural engineer should determine if a secondary structural system is required based on the design loads.
To date, the tallest structure constructed exclusively of SIPs is four stories. Taller structures are possible; however, design limitations are due to the fact that SIPs are bearing walls and therefore open spaces at lower floors are more difficult to achieve. Often large SIPs structures rely on a secondary framing system of steel or timber to satisfy requirements for unobstructed spaces. Unique screw connections are available to attach SIPs to wood, light gage steel, and structural steel up to 1/4 inch thick.
It is imperative for foundations for SIPs panels to be level. There is little tolerance for differential settlement. If there is substructure shift, it will compromise the sealant of the panels' joints which may cause moisture infiltration. Allowable deflection tolerances set by the manufacture of the panels and sealants should be consulted when designing the foundation. Minor imperfections may be accommodated with careful, skilled installation.
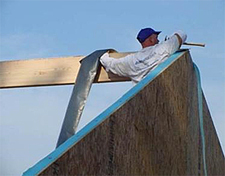
Figure 4: SIP ridge and gable end tape/gasket seal. Photo Credit: SIPschool
Joint design is imperative for structural and long-term durable performance. One particular weakness of SIPs panels is air penetration from the interior at joints or penetrations. In cold climates, if warm humid interior air reaches the interior face of the outer sheathing layer it can condense, causing rot and deterioration. Frequently this outer layer is OSB, which is particularly susceptible to moisture damage.
Proper joint design should be given special attention, and if properly executed in the field, will eliminate the air infiltration problems. The primary joint design generally includes seals within the thickness of the panel, typically spray foam or gaskets. There should be an overflow seeping of the spray foam at the joints to indicate a full depth joint seal as shown in the figures below. An additional secondary seal air seal of tape or gasket should be provided at the interior face of the panel, especially in cold climates.
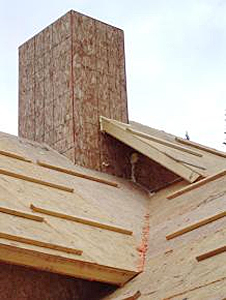
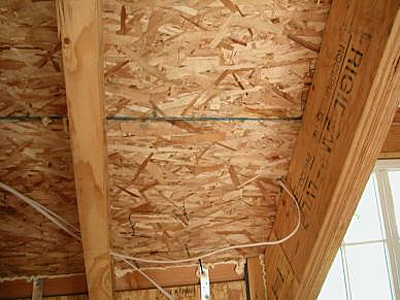
Figure 5: Example of SIPs used for roof panels showing seeping of sealant at SIP joint, Breckenridge, CO. Photo Credit: CW Associates, PLLC, (CWA Architecture)
Figure 6: Example of SIPs used for wall and roof panels showing seeping of sealant at SIP joints, Winter Park, CO. Photo Credit: CW Associates, PLLC, (CWA Architecture)
Two of the most widely used panel joint connections are the surface spline and the block spline. The surface spline joint connection consists of strips of OSB or plywood inserted in slots in the foam just inside each skin of the SIP. The block spline is a thin and narrow SIP assembly that is inserted into recesses in the foam along the panel edges. The surface spline connection and the block spline connection result in a continuous foam core across the panels, eliminating air infiltration at the joints. If structurally required, panel joints can be reinforced with one or more 2x lumber studs or Laminated Veneer Lumber (LVL) along the edges of the two panels to be connected. One disadvantage of this type of connection is that a thermal bridge is created at the joint. Another joint connection, mechanical Cam locks, create a tighter joint between panels, but make up only a small percentage of the market. In addition, Cam locks can only be set in PUR because the locks require a higher tensile strength than provided by other foams and the foam needs to expand and set around the lock's flanges. In any type of connection, the seam along the sheathing must be covered with a continuous line of foam sealant and/or panel tape.
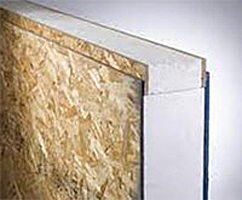
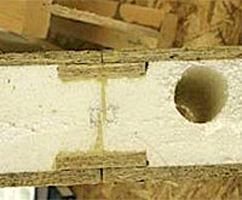
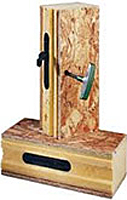
Figure 7: Block Spline
Figure 8: Surface Spline
Figure 9: Cam Lock
Openings can occur anywhere within the panel, including at the edges and corners. The panel foam can be recessed to accept 2x lumber headers. However, panels can be reinforced at headers so that additional structure is not required during construction. The inside panel and foam can be subtracted to provide beam pockets for roof and floor joists. Any opening within the SIPs that accepts another enclosure element must be properly sealed.
Plumbing chases are usually located in furred out framing or conventional framing should be used for plumbing walls.
Electrical chases 1-inch to 1-1/2 inches in diameter can be incorporated into the SIPs during the manufacturing stage. Foam is applied in any gaps resulting after the installation of electrical wiring.
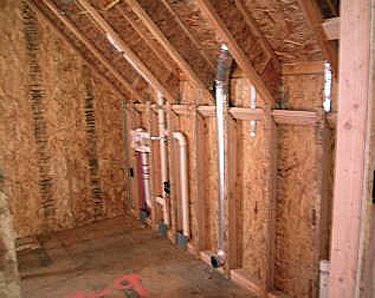
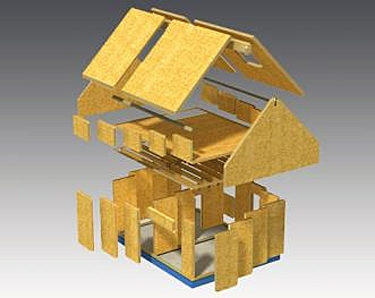
Figure 10: Example of SIPs used for wall and roof panels and a furred out wall at exterior panel for vents and plumbing, Tabernash, CO. Photo Credit: CW Associates, PLLC, (CWA Architecture)
Figure 11: Exploded Axonometric of a SIPs Building. Source: www.sun-spaces.com
Other unexpected penetrations made in the panels during construction should be made 1-inch larger in diameter than the penetrating pipe to allow for the application of foam sealant.
Typical wall panel thicknesses are 4-1/2 inches and 6-1/2 inches. The largest panel size to date is 9' x 24'. Curved panels are possible although not common and it is often more practical to use stud framing for non-orthogonal geometries.
Roof panels are typically 10-1/4 inches and 12-1/4 inches thick. Roof panel thickness depends upon the required R-value and span. EPS and XPS panels can be made up to 12-1/4 inches thick. PUR and PIR panels can be made up to 8-1/4 inches thick. End wall panels for various roof profiles can be achieved with SIPs.
Performance Issues
Thermal Performance: The quality of a building's envelope is measured by its ability to prevent infiltration of outside air. Recent energy code standards require an air tight building envelope, and a SIPs building with properly sealed panel joints is inherently airtight. The results of blower door tests on a room with SIPs walls and ceilings, one window, one door, and pre-routed wiring chases and electrical outlets compared to a identical room of 2x6 studs, OSB sheathing, fiberglass insulation, and drywall showed the SIPs structure to leak 90 percent less than the stud structure. (SIPA, ORNL)
The Whole Wall R-Value of a wall assembly is currently the most accurate method of quantifying its thermal performance. The Whole Wall R-Value takes into account the resistance of heat flow through an opaque cross sectional area of the insulation and structure while accounting for the loss of energy at the interfaces of the wall with the roof and floor and at corners and fenestrations. The Whole Wall R-value of a 4-inch SIP wall is 14. The Whole Wall R-value of a 2x4 wall is less than 10. The Whole Wall R-value of a 2x6 wall is between 11 and 13.7 depending on the quality of the installation of batt insulation. The elimination of thermal bridging and a more air tight envelope contribute to the higher Whole Wall R-Value of SIPs walls when compared to conventional metal and wood stud walls. (SIPA, ORNL)
Table 4: Typical SIP Whole Wall R-values
Thickness | EPS | XPS | PUR |
---|---|---|---|
Density in Panel (lb/ft3) | 0.90 | 1.5 | 2.3-2.5 |
4-1/2" | 13.1 | 17.7 | 22.7 |
6-1/2" | 19.9 | 27.2 | 35.1 |
8-1/4" | 26.0 | 35.5 | 46.0 |
10-1/4" | 32.9 | 45.0 | NA |
12-1/4" | 39.8 | 54.6 | NA |
Table 4 Notes:
- Based on 8-ft wall with single bottom plate double top plate and single 2X band around rough openings.
- Based on Spline, Block Spline, or Cam lock panel joint connections.
- Values are for the panels only and do not include contribution from finish materials.
- Values will vary depending on wall height and number of rough openings.
- In roof applications, the use of wood splines will reduce these values.
Moisture Protection: Since the SIPs' foam core acts as a vapor barrier, the weather barrier must be permeable in order to allow the SIPs sheathing panels to dry outward. A continuous air space, between the drainage plane and the exterior cladding, and vented openings at the top and bottom of the walls to allow for convective air flow is recommended to ensure adequate drying of the SIPs. This also applies to SIPs used as roof structure. Air should be able to flow under the roofing material between the eave and the ridge. In addition, all panel joints, openings around windows and doors, and other chases should be properly sealed and/or flashed to prevent moisture infiltration.
Particular attention to details that ensure that interior air infiltration never reaches the outer sheathing layer is imperative.
For areas subject to flooding, waterproof sheathing materials such as cementitious skins or thermoplastic skins are an ideal alternative to OSB. (Uddin) However, if SIPs with OSB sheathing come into contact with water, the structural integrity of the panels can be saved if the OSB is quickly exposed to allow to dry.
Fire Safety: Since the majority of SIPs construction is for Type V construction where the SIP walls are load bearing, NFPA 285 compliance does not apply. At this time, there appears to be no NFPA 285 tests that have been performed for SIPs wall construction. Refer to a Building Envelope Consultant if you plan to use SIPs construction where the NFPA 285 test may be required.
Acoustics: SIPs insulate against high frequency noise better than low frequency noise. SIPs are not recommended to use as floors over an open interior space without the application of a sound barrier.
Material/Finish Durability: The fastener requirements for exterior cladding and interior finishes are specific to the panel manufacturer; consult the manufacturer's specifications for this information. It is recommended that a ventilation space is created with furring strips between the exterior face of the panel and the exterior cladding. This allows for the panels to dry out when water vapor enters the panel.
Maintainability: The quality of SIPs is set in the manufacturing stage. Proper lamination and smooth surfaces and edges will ensure that the SIPs can endure long-term use as long as the structural skins are properly protected from degradation. It is important to note that if moisture causes deterioration of the skins, then there is a structural issue that must be repaired. Repairs can require replacement of a much larger area than the just the deteriorated portion.
Foam insulation is subject to insect and rodent infestation. Insecticides are added to the panels during manufacturing or later on site.
General Detail Principles
- The SIP exterior design building envelope form is only limited to the design imagination. (See Figures 1, 12 & 13)
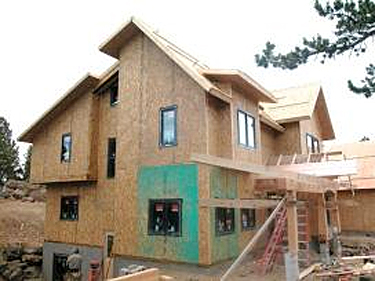
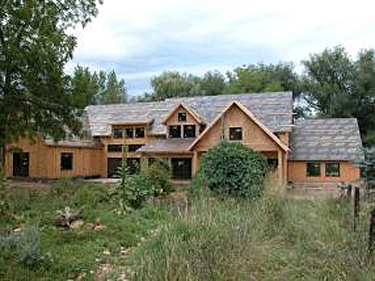
Figure 12: Example of SIPs used for wall and roof panels in a complicated architectural form, Nederland, CO. Photo Credit: CW Associates, PLLC (CWA Architecture)
Figure 13: Example of SIPs used for wall and roof panels in a complicated architectural form, Boulder, CO. Photo Credit: CW Associates, PLLC, (CWA Architecture)
- SIPs can accept any type of properly designed exterior cladding.
- SIP panel joints, voids, and penetrations to be provided with an airtight seal by continuous foam sealant, gaskets, and SIP tapes. Continuity of the inner air seal is imperative to long-term performance.
- Verify SIP span and structural limit requirements. (See Figures 1, 14, 16, & 17)
- Verify SIP nail, screw, and Cams - attachment patterns, fasteners types, and spacing requirements. (See Figures 14, 15, 16, & 17)
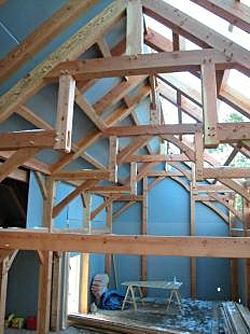
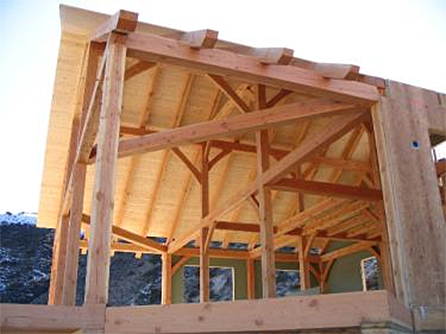
Figure 14: Example of SIPs used for wall and roof panels with drywall on a timber frame structure, Breckenridge, CO. Photo Credit: CW Associates, PLLC (CWA Architecture)
Figure 15: Example of SIPs used for wall panels with drywall and roof panels with tongue and groove (T&G) decking, Lake Alcova, WY. Photo Credit: CW Associates, PLLC, (CWA Architecture)
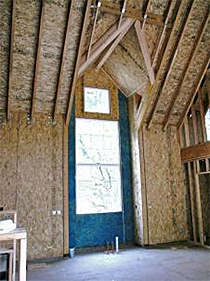
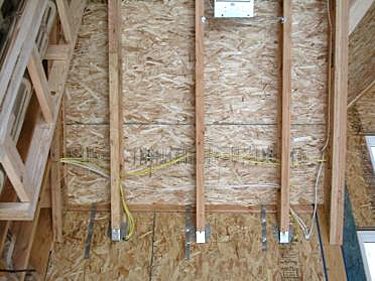
Figure 16: Example of SIPs used for wall and roof panels in a dormer with truss joist framing, Boulder, CO. Photo Credit: CW Associates, PLLC, (CWA Architecture)
Figure 17: Example of SIPs used for wall and roof panels showing microlam and truss joist hanger connections and strapping, along with wiring, Glacier Park, CO. Photo Credit: CW Associates, PLLC, (CWA Architecture)
- Provide exterior roof and wall ventilation/drainage plane systems.
- Don't provide plumbing in the exterior SIP walls. (See Figure 10)
- Coordinate any in SIP electrical.
- Properly sealed SIPs will provide for the air, vapor, and thermal barriers.
- Detail for a continuous inner line of redundant air seal at all joints and penetrations using sealant, foams, tapes, and gaskets. (See Figures 4, 5, & 6)
- Provide for the exterior wall and roof (WRB) water resistance barriers. Note that the WRB should be vapor permeable and must make all joints water and airtight.
- Provide appropriate flashing systems at all exterior building envelope openings and penetrations.
- Properly designed HVAC systems are required to address the air tightness and energy efficiency inherent with SIP designed buildings.
General Assembly Principles
- Foundation and/or floor deck to be square and level within tight tolerances for effective SIP installation.
- Detail shop drawings shall be provided by the manufacturer for coordination and to address the General Detail Principles as mentioned above.
- SIP panel skins need to have solid full bearing support. Review the installation of the SIP bearing plates for this support.
- The project design team should review any field cutting of SIPs.
- Foam sealing of SIP panel joints shall be reviewed for continuous full deep sealing. Usually proper foam sealant installation can be observed by foam seeping at the joints that will need to be cleaned off the panel exterior surface. (See Figures 5, 6)
- The inner redundant air seal is commonly accomplished with gaskets placed over the bearing points, spray foam, and with tapes at exposed joints. Carefully select tapes and primers suitable for panel type for long-term adhesion to the panels. Note that OSB is particularly problematic for most common construction tapes. (See Figures 4, 5, & 6)
Lessons Learned
The Juneau, Alaska Roof Reports that have been published (see publications list below) described evidence that interior air infiltration thought the joints in the SIP roof panels indicated premature deterioration of the top of the OSB skin of the roof panel joints. The general conclusion the building science team reported was that the moisture damage was due to evidence of the lack of proper joint panel sealing.
Logistical and Construction Administration Issues
Service Life: The service life expectancy of components that are mated with the SIP assembly should match the service life expectancy of the SIP wall itself. Components include durable flashing materials, structural components in the SIP panel, sealants, foam, tape, gaskets, fasteners, etc.
Field Mock-up: A mock-up representative of the design assembly should be required for all SIP walls. This is best completed as a small chosen area of the construction prior to full construction production, so that there is an opportunity to make design changes based on the observation of the field mock-up.
Field Observation of SIP Walls: Require field observation for the installation of the SIP walls, and its components, for quality assurance of SIP wall fabrication and installation.
Shop Drawing Coordination: Require SIP wall installation shop drawings showing all adjacent construction and related work, including flashings, gaskets, sealants, structural components in the SIP's, attachments, and indicate sequencing of the work.
SIP wall systems require expertise on the part of the building designer, the manufacturer, the fabricator, and the installer. The Architect and Engineer of record may consider engaging an outside consultant, if such expertise is not available within the project team.
Other Considerations
Although the total time for manufacturing and assembling a SIPs structure is less than that of a framed structure, more time is required in planning. Openings in the panels, non-orthogonal designs, electrical, and AV coordination must be determined prior to the manufacturing of the SIPs.
Window installation is similar to that of wood frame construction. The manufacturer's specifications should be consulted to insure proper installation.
SIPs manufactured in the United States no longer use adhesives with urea-formaldehyde in OSB panels. The foam cores consist of 98-percent air and are made using non-CFC blowing agents.
A properly built SIPs structure will be airtight; therefore fresh-air ventilation is required of the mechanical system to prevent interior moisture problems and the build-up of indoor air pollutants.
The contractor and the installers should be experienced with SIPs and it is recommended they have become registered through SIPA and/or SIPschool or be trained by the Brotherhood of Union Carpenters to help prevent poor installation of SIPs by a crew that is not familiar with the product. The Architect and Engineer of record along with the SIP manufacturer should observe the construction of the SIPs for compliance with the approved project submittals.
Details
The details associated with this section of the BEDG on the WBDG were developed by committee and are intended solely as a means to illustrate general design and construction concepts only. Appropriate use and application of the concepts illustrated in these details will vary based on performance considerations and environmental conditions unique to each project and, therefore, do not represent the final opinion or recommendation of the author of each section or the committee members responsible for the development of the WBDG.
The details, graphics, and related information shown in the details are intended to illustrate basic design concepts and principles only and should be considered collectively with the appropriate narrative sections of the Whole Building design Guide (WBDG). The information contained therein is not intended for actual construction, and is subject to revision based on changes and or refinements in local, state, and national building codes, emerging building envelope technologies, and advancements in the research and understanding of building enclosure failure mechanisms. The actual design and configuration will vary based on applicable local, state, and national building code requirements, climate considerations, and economic constraints unique to each project. Full compliance with manufacturers' recommendations and recognized industry standards is recommended, and should be reflected in the appropriate sections of the project specifications.
The following details can be viewed online in Adobe Acrobat PDF by clicking on the PDF icon to the right of the drawing title. Download Adobe Reader.
Emerging Issues
SIPA recently completed Technical Bulletin 008, Wall Aspect Ratios for SIPs, which provides the necessary data for compliance with the IRC and IBC requirements.
SIPA and APA (The Engineered Wood Association) recently completed tests to measure the effect of moisture exposure on the structural strength of the panels. Findings are published in Technical Bulletin 009 of the Structural Insulated Panel Association.
Relevant Codes and Standards
- APA Structural Insulated Panels Product Guide, APA, The Engineered Wood Association
- ANSI/APA PRS 610.1 Standard for Performance Rated SIPs in Wall Applications
- ASTM Standard has been proposed to address limit state design.
- American Society of Testing and Materials (ASTM) C393-06 "Standard Test Methods for Flexural Properties of Sandwich Construction."
- American Society of Testing and Materials (ASTM) E1803-06 "Standard Test Methods for Determining Structural Capacities of Insulated Panels."
- American Society of Testing and Materials (ASTM) E455-11 "Standard Test Methods for Determining Structural Capacities of Insulated Panels."
- American Society of Testing and Materials (ASTM) E72 "Standard Test Methods of Conducting Strength Tests of Panels for Building Construction."
- American Society of Testing and Materials (ASTM) E84-04 "Standard Test Method for Surface Burning Characteristics of Building Materials."
- International Residential Code Section R610: Structural Insulated Panel Wall Construction
- NTA Inc., Listing Report SIPA120908-10, Evaluation of Code Compliance with International Building Code and International Residential Code
- Structural Insulated Panel Association, "SIPs in the IRC"
Additional Resources
Details
- APA CAD Details for Structural Insulated Panels
- International Residential Code: Section R610 Structural Insulated Panel Wall Construction Figures
- Structural Insulated Panel Association, SIPs Construction Details
Publications
- Analysis of the Seismic Performance of SIPs , Federation of American Scientists.
- BSI-028: Energy Flow Across Enclosures by Lstiburek, J. 2009.
- Builder's Guide to Structural Insulated Panels (SIPs) for all Climates by Lstiburek, J. Somerville, MA: Building Science Press, 2008.
- Building with Structural Insulated Panels by Morley, M. Newtown, CT.: The Taunton Press, 2000.
- A Journal of Contemporary Wood Engineering, Vol. 22, Number 1, Spring 2012.
- "Modeling Structural Insulated Panel (SIP) Flexural Creep Deflection" by Taylor, S.B., Manbeck, H.B., Janowiak, J.J., Hiltunum, D.R. Journal of Structural Engineering, Vol. 123, No. 12, December, 1997.
- "SIPA Technical Report-Juneau, AK, Roof Issue" by Joseph Lstiburek, Ph.D., P. Eng. Structural Insulated Panel Association."
- "SIP Solutions for Commercial Construction", Structural Insulated Panel Association.
- "Thermoplastic Composite Structural Insulated Panels (CSIPS) for Disaster Mitigation Construction." Multihazard Issues in the Central United States: Understanding the Hazards and Reducing the Losses by Uddin, N., Vaidya, A., Vaidya., U. Edited by James E. Beavers. Reston, Virginia: American Society of Civil Engineers, 2009.
Thermal Performance
- "Thermal Performance and Wall Rating" by Kosny, J., Christian, J.E. Oak Ridge National Laboratory, 2004.
Fire Safety
- ICC-Evaluation Service Report: ESR-2233 AFM Corporation, R-Control® Structural Insulation Panels (SIPS)
Organizations
- APA – The Engineered Wood Association
- Building Science Corporation
- Oak Ridge National Laboratory
- Structural Insulated Panel Association (SIPA)
- The SIPschool
NOTE: Photographs, figures, and drawings were provided by the original author unless otherwise noted.