Overview
Within This Page
Aircraft hangars are commonly referred to as "glorified garages" for airplanes. They can vary from simple "shade" structures that protect all or parts of the aircraft from the elements to complicated environmentally controlled maintenance facilities in which robots apply radar absorbing coatings. However, since planes are designed to fly, it is essential to minimize their maintenance time in the hangar and maximize their availability to fly.
The Armed Services have developed definitive designs for hangar facilities to house and maintain their aircraft. Many of these definitive designs are shown in UFC 4-211-01N Aircraft Maintenance Hangars: Type I, Type II and Type III. Much of the criteria for the design comes from AFM 32-1084 Facility Requirements.
In the commercial aircraft sector the designer needs to rely on Facility and Planning Criteria that are issued by the aircraft manufacturers for their aircraft or a third party compilation of data. For example, the Boeing aircraft characteristics can be found on the company's website. The designer must follow local building codes and integrate the characteristics of all possible aircraft that can populate the hangar to develop the space requirements for the intended use of the hangar.
There are five types of spaces in hangar facilities:
- Hangar Area
- Shops Area
- Warehouse Area
- Office/Administration and Specialty Areas
- Building Utilities Area
Careful analysis of the following will allow designer to determine the space needs for general spaces listed above common to aircraft hangars.
- Identification of the type of aircraft that will populate the hangar.
- Identification of the aircraft mix that will populate the hangar.
- Identification of the aircraft maintenance functions that will be performed in the facility.
- Estimation of the type and amount of shop area required to perform the maintenance functions.
- Estimation of the type and amount of warehouse space required to support the maintenance effort.
- Estimation of the floor space required for Office and Administration Area.
- Identification of special purpose areas such as locker rooms, toilets, personnel berthing area, dining areas and public lobbies to name a few.
- Estimation of the floor space required for the Building Utilities Area.
Building Attributes
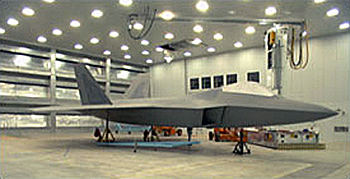
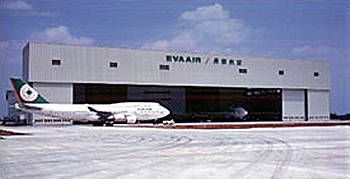
F22 Fighter Aircraft Robotic Coating Facility, Lockheed Martin Aeronautical Systems Company—Marietta, Georgia Photo Credit: Burns & McDonnell
160–meter clear span Aircraft Maintenance Facility for Evergreen Airways in Taiwan, Republic of China Photo Credit: Burns & McDonnell
Determine Facility Space Requirements
Step 1: Determine the types and number of aircraft which populate the hangar.
During this initial stage, input is needed from the hangar's future owner about his aircraft fleet. Information such as the following:
- Type of aircraft in the fleet
- Number of each type of aircraft in the fleet
- Mix of aircraft that will populate the hangar
- Allowance for future aircraft that may populate the hangar
Step 2: Determine the Maintenance Function of the Hangar Facility.
Input is needed from the owner with regards to the maintenance that will be performed on the aircraft in the hangar. This can vary from no maintenance at all to complete overhaul of the aircraft. Different levels of maintenance are required by the Federal Aviation Administration for certain aircraft currently in operation.
Step 3: Compile the Aircraft Characteristics
Some references to obtain physical characteristics and maintenance requirements of aircraft are as follows:
- Jane's All the World's Aircraft
- Burns & McDonnell Aircraft
- Airbus
- Boeing
- Cessna
- Gulfstream
- Piper
- Raytheon Aircraft Company
Step 4: Determine Hangar Space Requirements
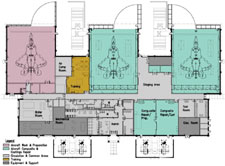
Coating /Composite Restoration Facility for Fighter Aircraft at Langley AFB View enlarged plan Photo Credit: Burns & McDonnell
To determine the most efficient use of hangar space use templates representing the aircraft and floor plans drawn at the same scale. Arrange the templates in various combinations to the make the most efficient use of space and permits maintenance operations.
Minimum separation distances between aircraft and minimum distances between the aircraft and other obstructions are defined in some building codes and in AFM 32-1084Facility Requirements.
Another factor to consider in sizing the hangar space is the fire protection requirements. The National Fire Protection Association standard, NFPA 409: Standard on Aircraft Hangars establishes four different groups of hangars based on their size and construction type. In general, the smaller the hangar space the less expensive the fire protection and utility requirements.
When sizing the hangar space, do not overlook tail heights, the height and width of the hangar door openings, the structural depth of columns and trusses and the turning radius of tow vehicles connected to aircraft. Also in larger hangars, distance to means of egress become a concern and should be laid out to meet local codes and NFPA 101: Life Safety Code.
Step 5: Determine space needs for the Maintenance Shops and Warehouse
The maintenance shops and warehouse provide space and storage for required maintenance activities such as fabrication shops, airframe repair, engine repair, aerospace systems repair, battery servicing area, cryogenics maintenance, interior finishes repair and nondestructive testing laboratory.
For Air Force Facilities, AFM 32-1084 Facility Requirements lists maintenance shop space requirements for different squadrons of aircraft. Similar rational should be used in the commercial arena with input from aircraft manufacturers.
The Federal Aviation Administration mandates procedures to be followed by operators when establishing aircraft inspection intervals and overhaul times.
Step 6: Determine space needs for the Office/Administration Area
The space needs in the Office/Administration area are similar to those required in any office building. The general rule of thumb according to Office Finder is 175 to 250 square feet of useable space per person.
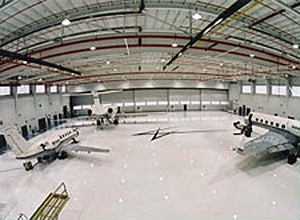
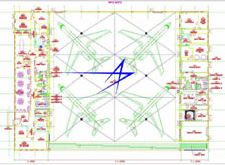
Lockheed Martin Corporate Hangar Facility—Baltimore, Maryland Photo Credit: Burns & McDonnell
Mechanical System Requirements
Determining the space need for the utility systems is highly dependent on the hangar maintenance function and the available utilities. In some corrosion control hangars the HVAC requirements are so stringent that the mechanical rooms can be as large as the hangar space itself. Also in corrosion control hangar spaces the mechanical rooms should be located adjacent to the hangar space and with an exterior wall for outside air requirements. The HVAC in the hangar space must be integrated with the fire detection system to shut down in case of a fire.
In general, the hangar space usually requires fire protection using water mixed with an Aqueous Film Forming Foam (AFFF). This can be applied by an overhead system or water cannons mounted near the floor. If the existing fire water pressure isn't adequate, the fire protection system may require a reservoir and booster pumps to satisfy the demand of the hangar space. The National Fire Protection Association standard, NFPA 409: Standard on Aircraft Hangars establishes fire protection criteria for hangars based on their size and construction type. Another resource is the owner's insurance carrier who should have input into the fire protection and detection systems.
Electrical System Requirements
The electrical requirements of the hangar facility should meet the requirements of NFPA 70: National Electrical Code®. The hangar space should be classified as hazardous or nonhazardous according to NFPA 70 and the electrical installations designed accordingly. Electrical equipment in the hangar space should be waterproof, NEMA Type 4 (minimum rating) when deluge sprinkler protection is provided. Various power supply voltages and frequencies are required in the facility because Aircraft and Ground Support Equipment operate on different voltages and frequencies than normally provided by the public utilities.
Hangar Doors
One of the largest single design elements to be selected is the type of hangar door to be utilized. There are several different types (sliding, vertical lift, bifolding, fabric, etc) and each type has advantages and design implications for the overall structure.
Emerging Issues
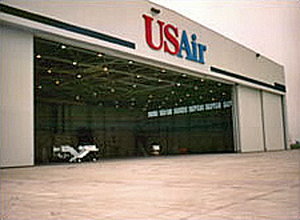
412–foot Clear Span Maintenance Hangar for US Airways in Indianapolis, Indiana Photo Credit: Burns & McDonnell
Sustainable Design
Sustainable design should be incorporated into every building design so the building can perform efficiently without wasting energy during its lifetime. The hangar area is particularly susceptible to heat loss as the hangar doors are opened for aircraft movement.
Aircraft Metrics
The next generation of aircraft is larger and heavier than current aircraft that will make many existing hangar facilities obsolete. For a primer see Burns & McDonnell's Special Report to the Airline Industry, How Will New Large Aircraft Affect Your Airport Facilities .
New Technologies
As Aircraft manufacturers move towards composite materials and avionics become more sophisticated, the hangar maintenance facility will need to respond to the new requirements. The aircraft maintenance facility will resemble an industrial facility which will require remediation of toxic effluents, air pollution permits, safety standards for working in hazardous areas and a high tech facility with laboratories and clean rooms.
Physical Security
The aviation industry is a high profile industry and is a target for terrorist attacks. Future building designs will incorporate higher levels of security and force protection/anti-terrorism standards.
Relevant Codes and Standards
- ICC IBC International Building Code or other state mandated building code
- Local Building and Zoning Codes
- Air Force
- Army Corps Of Engineers
- Department of Defense
- National Fire Protection Association