Introduction
Within This Page
For the long–term operational success and viability of a new facility, operational efficiencies require attention and development during the design and construction phases which are heavily influenced by the high pressures imposed for schedule and budget compliance. If not planned well in advance, the transition from construction to operation can be chaotic. A predictable opening day that can confidently deliver stable and reliable building performance is dependent on three key components: facility readiness, people readiness, and information readiness.
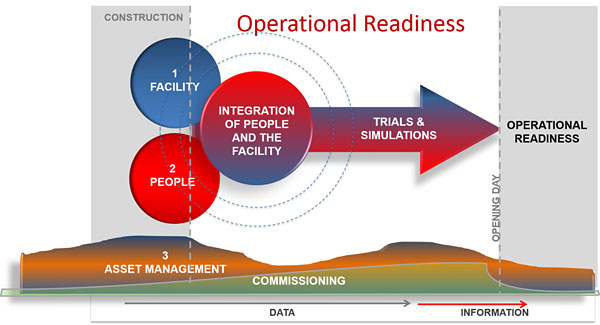
Operational Readiness diagram. Courtesy of Jacobs.
Description
Bringing a new facility to life and integrating with an existing asset portfolio, can be a stressful endeavor for the receiving organization expected to operate, manage, and maintain the building with finite resources. Value engineering may have saved considerable construction dollars, but may have also affected life–cycle costs and maintainability. Owners of newly constructed facilities can be faced with a building that underperforms, requires unplanned downtime, additional rework, or provides a lesser occupant or visitor experience.
For a new facility to reach its full potential and deliver the maximum value to occupants and owners, it must perform as intended and deliver the expected physical environment for the organization, employees, visitors, and occupants. A predictable opening day that can confidently deliver the intended environment, whether it is focused on production or customer service, is dependent on three primary factors: workforce planning; effective facility transition planning; and transference of relevant facility asset information.
Workforce Planning
The identification of training needs for operating, maintaining, and managing the new facility is essential for preparing the facility operations and maintenance workforce for the transition. Staffing requirements should be determined based on best practices for organizational processes and maintenance procedures, including response times, maintenance levels, reliability goals, preventive maintenance frequencies, and predictive maintenance practices. Staff preparedness requires advanced training for building systems, applicable codes and regulations, building familiarization and wayfinding, scenario planning and testing of emergency procedures, awareness of locations for critical spare parts, and vendor contact information.
Opening day risks associated with workforce preparation can be limited to chaos finding tools, or can be as impactful as negatively affecting the customer or user experience if issues such as room temperatures, lighting, or access cannot be quickly resolved. A fully staffed response team should be deployed for opening day to quickly respond to any customer or employee initiated requests to adjust facility components for occupant comfort including air quality, noise and potential odors.
Now that the staff is prepared, is the building prepared?
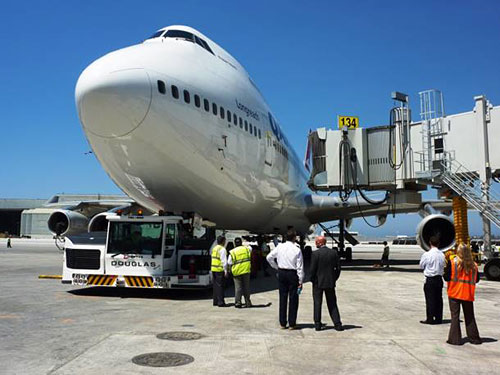
A trial at LAX international Airport where an airplane was pulled into a new gate to test the locations of fuel pits and to make sure the boarding bridges reach the doors. Photo credit: Jacobs.
Facility Transition Planning to Asset Management
For the long–term operational success and viability of a new facility, asset management requires attention and development during the design and construction phase where the focus is predominantly on building the physical assets, driven by the high pressures imposed for schedule and budget compliance. If not planned, the baton pass from construction to occupancy and asset management can be less efficient and less effective.
Transitioning from a construction zone to an occupied facility requires a series of validations that building systems and equipment are operating as designed and within efficient tolerance levels as specified by the design and commissioning teams. A building monitoring system will provide valuable insight into the overall performance and efficiency of the building, while allowing fine-tuning and adjustments during the system stabilization period. Including engineering and maintenance teams in the performance validations will offer early training and understanding of any potential systems that may require additional monitoring and adjusting to ensure operational efficiency during and after the stabilization and equipment burn-in phase. A smooth baton handoff during the commissioning and stabilization phase will ensure the facility management teams are not stumbling to balance building systems when customers, visitors, or staff are in the building. Ideally, the engineering and maintenance team should be fully trained and capable of operating the facility prior to the relinquishment of the site by the construction and commissioning teams.
A seamless transition from construction to operations with asset management will reduce startup costs and provide a higher quality occupant and user experience from opening day. A defined plan that addresses organizational needs for asset information and implemented business processes will frame the transition and improve reliability and maintainability. Shifting the focus to long-term maintainability and asset management early in the design and construction phase will enhance cost reductions throughout the life of the facility and ease the transition from construction to asset management.
Engagement of the operations and support teams, including security, environmental health safety and security, facility management, and engineering and maintenance, throughout the system startup and commissioning phases will have staff better prepared to accept full operations and maintenance responsibility during the transition to a fully operational facility with the ability to support the owning organization in a productive and safe environment.
Transference of Relevant Facility Asset Information
The ability to respond quickly to unplanned events is frequently dependent on accessible, reliable, and accurate information about the building; including as built plans, building systems information, and real time system performance. Additional information, such as warranty documentation, performance specifications, inspection records, permits, critical spare parts, manufacturer make and model, year of installation, and expected life cycle are valuable attributes to proactively manage the building assets through the use of an integrated work management system (IWMS).
Establishing a document library early in the process that organizes and tracks information received throughout the construction and commissioning process will help to identify any documentation gaps at final acceptance of the new facility. This process can be streamlined by pre-determining relevant information for the facility and systems that will need to be captured during the design, construction, and commissioning phases. If an enterprise asset management system (EAMS) is being used to manage the building portfolio, then data can be mapped for direct transference from the design and construction software such as building information models, CAD tables, progress photo databases, inspection reports, commissioning data, etc.
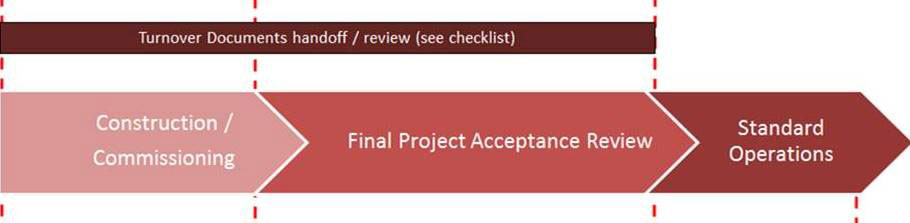
Operational Readiness Flow Diagram. Courtesy of Jacobs.
Understanding the potential risks and cost overruns associated with transitioning a new facility can enable the owning organizations to effectively and predictably plan for smooth transitions from construction to operational readiness and long term asset management that contribute to lower O&M costs, increased facility longevity and a superior customer or occupant experience. With an increase in the level of technology in facilities coming online in the near future, it is imperative that the transition planning, workforce preparation, and data transference are consistent and reliable for organizations expanding their portfolio and seeking an integrated operations and asset management program from opening day of a new facility.
Additional Resources
Publications
- Operations and Maintenance Best Practices Guide Release 3.0, Chapter 7: Commissioning Existing Buildings
General Services Administration (GSA)
National Institute of Building Sciences Facility Maintenance and Operations Committee