Introduction
Within This Page
Many buildings constructed today extend one or several floors below grade level. These below grade areas provide functional spaces for uses such as storage, office space, mechanical/electrical rooms, parking, tunnels, crawlspaces, etc. While below grade areas in buildings provide important critical functions for the building, the subject of below grade building enclosure systems, although widely addressed during construction practices is not always wholly understood. The below grade portion of the building enclosure is seldom analyzed numerically in design. Acceptance of poor performance of the below grade building enclosure is typical and historically not questioned. Leaking into basement areas is a common problem for building operators and managers. Air quality, such as radon, and conditioning in terms of humidity levels are often a concern.
Durability of design and materials is mandatory with below grade enclosure systems. Unlike some other building components that might be designed to be replaced several times within the overall building service life, below grade systems need to be built to approximate overall service life. Below grade systems are often inaccessible for repairs and extremely costly if repairs or modifications are necessary. For below grade enclosure systems design and materials must not focus on the first initial cost but consider the life cycle costs of various design options, especially costs to repair or replace systems that are buried.
Buildings frequently have plazas, vaults, tunnels or extensions below grade. The planning, development, detailing and construction of waterproofing for such features are significant. Although much more complex and far more maintenance intensive, these features are generally not treated with the same detailing attention that roof assemblies receive. Protection, drainage and isolation along with thermal considerations must be incorporated into the design. Requirements for overhead waterproofing in tunnels or building obtrusions are significant and need to be treated accordingly. Design of plaza surfaces, green-scape and tree or soil planter features, above the buried element also requires special design consideration.
Over the past two decades, plazas and special use features (fountains, planters and even athletic function) have become a more common and complex element in structure design. Tunnels and vaults, although a historic feature, are also experiencing increased design demand as they are upgraded to higher levels of service to accommodate utilities, mechanical services or signal and communication conduits.
Plaza decks, tunnels and vaults are subject to some of the most accelerated and vigorous deterioration and distress of any structural system. Harsh exposure conditions from exposure, moisture, thermal effects, weathering, and traffic often reduce these systems serviceability at a rate even surpassing that of parking and bridge deck slabs. Accordingly, special analysis of plazas, tunnels and vaults aesthetic, wearing, moisture protection and isolation, and structural support systems, should be performed.
Plaza systems generally disintegrate and become unserviceable for three reasons:
- Ineffective design
- Poor construction
- Abnormal "unexpected" loadings.
Other common causes of plaza deterioration or failure are: severe exposure (including freeze thaw), chemical applications, overload, and/or improper materials selection and application.
The design of tunnels and vaults, although not specifically discussed, is similar to the design of plaza decks, foundation walls, and slabs on grade which are discussed below and in the related sections.
Readers are advised to obtain expert advice when designing systems which are below the water table or which are enclosing particularly vulnerable occupancies. Expert advice may also be necessary when dealing with field conditions.
Description
These Design Guide sections describe the basic components of below grade enclosure systems and categorize its functions, provide guidelines for design considerations, and provide details for adaptation for actual building projects. The scope of these sections is limited to the enclosure elements of the below grade portion of the building and does not consider interior elements. Below grade enclosures are typically comprised of three main elements:
For each of the three elements the following items are discussed:
- Introduction—Overall Discussion
- Description—Elements and Properties
- Fundamentals—Principles of Design
- Applications—Ranges or Uses, Climates, Risk
- Details—Construction Details with Commentary
- Emerging Issues—Research and Development
- Codes/Standards—Allowances and Limitations
- Resources—Documents, Associations and Web Sites
Figure 1 graphically illustrates the three main elements and the typical loadings for below grade building enclosure systems.
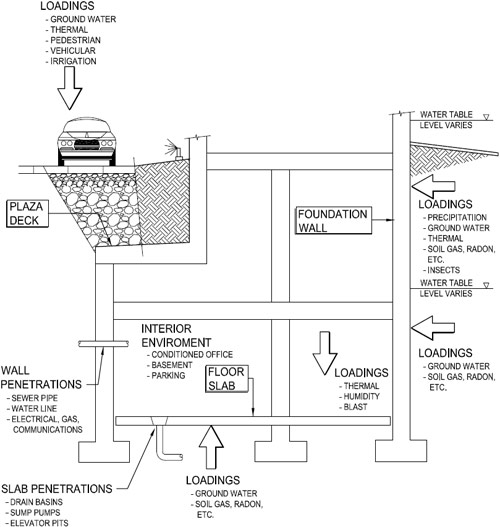
Fig. 1. Below Grade Building Systems Schematic
Fundamentals
As with other building enclosure systems the functions of each of the elements of the below grade building enclosure can be grouped into four categories, as follows:
-
Structural Support Functions—to support, resist, transfer and otherwise accommodate all the structural forms of loading imposed by the interior and exterior environments, by the enclosure and by the building itself. The below grade enclosure is often part of the buildings superstructure.
-
Environmental Control Functions—to control, regulate and/or moderate all the loadings due to the separation of the interior and exterior environments; largely the flow of mass (air, moisture, etc.) and energy (heat, sound, etc.).
-
Finish Functions—to finish the enclosure surfaces—the interfaces of the enclosure with the interior and exterior environments. Each of the two interfaces must meet the relevant visual, aesthetic, wear and other requirements.
-
Distribution Functions—to distribute services or utilities such as power, communication, security, water in its forms, gas, and air conditioned air to, from and within the enclosure itself.
The four function categories, i.e. Structural Support, Environmental Control, Finish and Distribution, are expanded in general terms for each of the three elements of below grade enclosures.
Applications
The success of below grade building enclosure systems is largely dependent on the ability to control moisture. The control of moisture can only be achieved with proper investigation, design and construction practices. Also of importance is to understand where problems are likely to occur. Kubal suggests the following principle:
"The 90% / 1% Principle: As much as 90 percent of all water intrusion problems occur within 1 percent of the total building or structure exterior surface area."
Therefore, attention to detail, particularly at penetrations and termination (connections to adjacent elements) is critical to the performance of below grade enclosure systems. Kubal suggests another principle that is equally important:
"The 99% Principle: Approximately 99 percent of waterproofing leaks are attributable to causes other than material or system failures."
Failures typically occur from improper design or construction practices not material failure itself. Putting these two principles together Kubal states:
"By considering these two principles together, it can be expected that 1 percent of a building's exterior area will typically involve actual and direct leakage and that the cause will have a 99 percent chance of being anything but material failure."
The success of waterproofing systems is very dependent on applicator skill and attention to detail. Recognizing that the performance of below grade building systems relies so heavily on design and construction aspects, it is critical to discuss the overall design and construction process.
The process can be divided into three (3) phases:
- Investigation Phase
- Design Phase
- Construction Administration Phase
Troubleshooting following construction when leakage occurs is also considered as a closing section of this guideline.
Through rigorous application of the criteria and design features presented the overall performance requirements of the system for characteristics including moisture, thermal, air quality, fire safety, and acoustics can be determined.
A waterproofing assembly should be designed after a number of criteria have been carefully considered, including:
- Climate and geographic location
- A building's intended used and design life expectancy
- Exterior and interior temperature, humidity and use conditions
- Code requirements
- Type and condition of substrate, including soil
- Structural system
- Slope and drainage
- Waterproofing system type including overburden
- Accessibility and building configuration
- Building movement
- Type and amount of insulation/protection/drainage needed
- Compatibility with adjacent building and/or system components
- Construction sequencing
- Worker safety
- Potential building additions
- Odors generated by certain system application methods
- Need for ventilation during installation
- Water table
- Construction traffic
- Penetrations
These criteria play important roles in the ultimate success or failure of a waterproofing assembly and should be considered by a designer to determine the appropriate components of a waterproofing assembly, applicable products and specifications, and construction details to be used.
In addition, a designer should be certain requirements of waterproofing material manufacturers, applicable insurance underwriters, and building codes and/or other regulatory agencies are taken into account. It is recommended that material manufacturers' published specifications and details be consulted during the design of a waterproofing assembly.
A. Investigation Phase
The investigation phase deals primarily with determining the site conditions prior to the design development. For virtually all construction projects, soil specimens are taken that provide basic information concerning soil conditions. These soil conditions once combined with water table information can identify the ground water characteristics in the vicinity of the site. It is these ground water characteristics taken as a benchmark that govern and contribute heavily to the success or failure of the below grade building enclosure system design.
Interpretation of site boring (and other site related) information should be made considering of the time of year borings were taken. For example, evaluating soil-boring conditions with respect to ground water could produce one result if samples were extracted during the spring months and under conditions of heavy rain or run-off from snowmelt. Similar samples taken at a later time in the year such as August or September following a dry season could result in different ground water conditions. Consult with a qualified geotechnical engineer to provide interpretation of soils investigations and recommendations for waterproofing systems.
Site work should also consider the conditions in the vicinity associated with surface characteristics; drainage slope, permeability, and other utilities or other features. Underground storage tanks, sewer lines, reservoirs, water ways or water shed paths need all be examined when considering the overall site conditions.
Structure Use Requirements—Following the site assessment, the structure use requirements concerning the need for absolute dryness or hundred (100%) percent waterproofing should be considered. Structures have variable demand for underground services. Structure utilization is a significant element of the original investigation process and should be fully considered during development of the criteria for moisture capture, moisture capture and overall water management system that affect waterproofing system design and selection.
Following the assessment of usage, a system for subsurface water management should be examined. There are both internal water management techniques, such as sump pumps or dewatering systems in the basement, or external foundation drains that all need to be coordinated to achieve effective water management at the time of design. Once again, the requirements for specific needs and features of the building basement and sub-basement system must be fully considered in order to achieve the desired result.
B. Design Phase
The design of the waterproofing system must follow the selected structural design system. Until the structural system is selected and certain features of the design established, it is not practical to develop an effective waterproofing system or water management system other than at a conceptual level. The sub-chapters on foundation walls, slabs-on-grade, and decks/plazas/tunnels/vaults provide information on waterproofing systems under the topic, "Environmental Control Functions." This document develops the concepts, principals and standards as opposed to specific detailing for each condition. Common details are provided for features of water management, waterproofing protection and the basics of system installation. Sound engineering judgment and expertise is needed to apply these guidelines and procedures to a particular project.
Clear definition of the penetrations required in the structural wall or floor system must be established. Detailing of these penetrations to make them water tight under all conditions of use are paramount to the success of below grade enclosure systems.
Proper specifications to address the various issues associated with water management should be done consistent with the typical specifications format. Where special requirements occur to amplify or highlight certain needs for the structure in question, special notations or supplemental specifications should be drafted that address the waterproofing system characteristics and particulars. Such specifications are typically accompanied by detailing of the various aspects of the waterproofing installation. This detailing once established in concept and for intent for specification requirements (prescription vs. performance) can be supplemented by manufacturer details addressing the particulars of a given waterproofing system. These details commonly deal with such things as penetrations, joints, drains, sumps and moisture collection systems.
C. Construction Administration Phase
Adequate construction administration involving the review of material submittals and installation sequences are important to performance, as is on site observation by the design professional to verify that the construction is being completed in general accordance with the construction documents. A well planned design improperly implemented will not provide adequate performance.
With the construction process underway, steps must be taken to properly coordinate the waterproofing applications or waterproofing requirements with the general contractor's scheduling. It is frequently the case that schedules are compressed and the needs of waterproofing exterior walls once satisfactorily curing is achieved can produce kamikaze type efforts with respect to exterior wall waterproofing. The conditions under which waterproofing must be installed in order to be effective and meet the manufacturer specification for warranty must be clearly spelled out. Exterior wall drainage application and subdrain discharge must be complete at this time.
Coordination meetings at the time of construction that include the waterproofing subcontractor, waterproofing material manufacturer, and any sub-trades should also be identified and coordinated. Features and characteristics of each installation and system should be examined closely.
Care should be taken to inspect the substrate surfaces for the anticipated waterproofing to ensure that all deleterious materials, stains, coatings, previous waterproofing, concrete flaws such as honeycomb or fins or splatters or tie remnants are removed completely to the satisfaction of the waterproofing Manufacturer.
The substrate surfaces should be dry and cured according to the waterproofing manufacturer's specifications prior to waterproofing application, or until Manufacturer is satisfied by various moisture test methods, such as a poly barrier condensation test. Finally, an adhesion pull test should be administered to the initial application of waterproofing to verify the bond to the substrate.
D. Post-Construction
Troubleshooting of the system at the time of installation of waterproofing systems and performed in an integrity test at the completion of the waterproofing installation should be considered. See the Resource Page on Integrity Testing. A special interest for water testing or troubleshooting before the fact relates to overhead structures that must retain water but will be subsequently buried or backfilled following construction. All aspects of troubleshooting at the time of construction should be considered.
Details
The following details can be downloaded in DWG format or viewed online in DWF™ (Design Web Format™) or Adobe Acrobat PDF.
Details related to below grade building enclosure systems with commentary can be found in the following sections:
- Foundation Walls—CAD Details and PDFs
- Floor Slabs—CAD Details and PDFs
- Plazas Decks—CAD Details and PDFs
Emerging Issues
The following are emerging issues in below grade building enclosure systems:
- System monitoring during service (waterproofing, protection, drainage grids or boards, soil separator/ filter fabrics)
- Waterproofing
- Water transmission rates vs. age—against physical variables head, membrane type, ground water chemistry
- Elastomeric properties vs. age—against physical variables head, membrane type, ground water chemistry
- Protection layer breakdown vs. age
- Drainage layer effectiveness vs. age—against water table, applied loads, soil separator type
- Soil filter/separator fabric type vs. permeability when used with various backfills
- Leak detection systems
- Designing for long term system Maintenance
- Injection grout systems for post construction leaks
- Wall weep ports to discharge impounded water
- Internal contained leak collection system at wall floor interface
- Interior positive side water proofing protection/membrane systems
- External secondary perimeter drain fields
- Service life prediction from below grade waterproofing
- Getting the maximum service-life from exterior systems
- Integration of existing systems with new adjacent (newly constructed) facilities
- Solving continuity problems
- Enhancing systems in place
- How to extend the existing system with targeted maintenance
- What options are available
- How can they be adapted to existing constructed systems
- Data utilization considerations
Relevant Codes and Standards
Conform to local codes and ordinances with regard to groundwater situations except where provisions provided in this document are more stringent or complete.
Additional Resources
WBDG
Products and Systems
See appropriate sections under applicable guide specifications: Unified Facility Guide Specifications (UFGS), VA Guide Specifications, Federal Guide for Green Construction Specifications, MasterSpec®
Publications
- Carmody, John, Christian, Jeffrey, Labs, Kenneth, Builder's Foundation Handbook , Oak Ridge National Laboratory, Oak Ridge, Tennessee, May 1991.
- Dworkin, Joseph F., "Waterproofing Below Grade," The Construction Specifier, March 1990.
- Gregerson, John, "'Airtight Approaches to Below-Grade Waterproofing," Building Design & Construction, June 1994.
- Griffin, C.W., Fricklas, Richard, The Manual of Low-Slope Roof Systems, Third Edition, The McGraw Hill Companies, Inc., 1996.
- Henshell, Justin, The Manual of Below-Grade Waterproofing Systems
, John W. Wiley & Sons, Inc., 1999.
- Kubal, Michael T., Construction Waterproofing Handbook, The McGraw Hill Companies Inc., 2000.
- Lstiburek, Joseph, Carmody, John, Moisture Control Handbook, Oak Ridge National Laboratories, Oak Ridge, Tennessee, October 1991.
- Ruggerio, S. S., Rutilia, D.A., "Principles of Design and Installation of Building Deck Waterproofing," Building Deck Waterproofing, ASTM STP 1084, L.E. Gish Editor, American Society for Testing and Materials, Philadelphia, PA, 1990, 5-28.
NOTE: Photographs, figures, and drawings were provided by the original author unless otherwise noted.